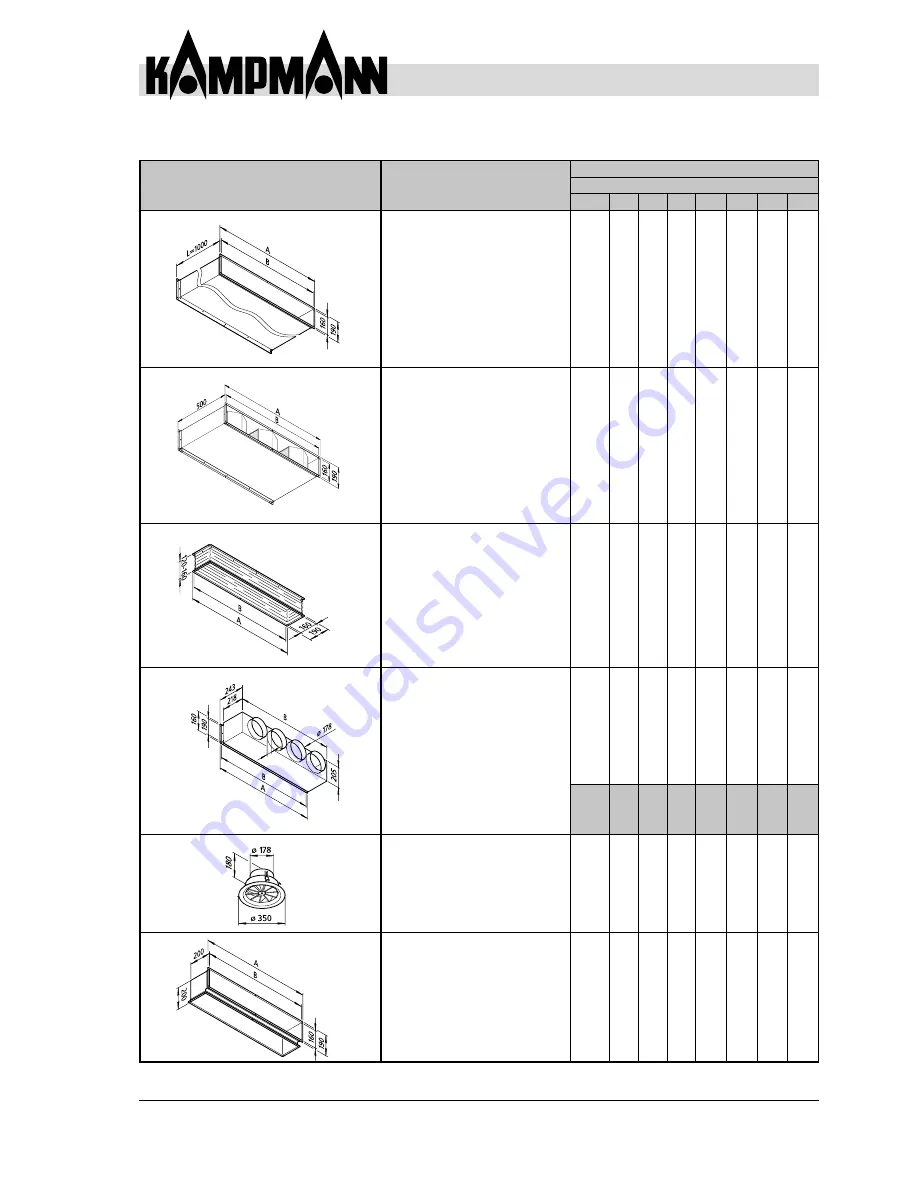
27
Venkon EC 115 V
27
Construction and Function
Air-side sheet steel accessories
Figure
Description
Dimensions [mm]
Model
1)
1
2
3
4
5
6
7
50
Air duct, type 148 35BB0B* 01
Standard length 1,000 mm,
Non-standard length on request
Weight (net) in kg
A
B
560
530
15
710
680
18
860
830
24
1010
980
29
1160
1130
29
1310
1280
29
1710
1680
29
50
Silencer, type 148 35BB0B* 06
Splitter silencer,
Non-standard length 500 m
Weight (net) in kg
A
B
560
530
11
710
680
13
860
830
17
1010
980
22
1160
1130
25
1310
1280
30
1710
1680
30
50
Flexible connection,
type 148 35BB0B* 04
With frame on both sides and flexible
canvas connection for structure-
borne noise decoupling and length
compensation of on-site dimensional
inaccuracies;
install. Length: 120-160 mm
Weight (net) in kg
A
B
560
530
2
710
680
2
860
830
2
1010
980
6
1160
1130
6
1310
1280
6
1710
1680
6
50
round pipe connection unit,
type 148 35BB0B* 05
For Venkon fan coil with flexible pipe
connection sockets for ø 180 mm
Weight (net) in kg
A
B
560
530
5
710
680
7
860
830
8
1010
980
9
1160
1130
10
1310
1280
12
1710
1680
15
Number
of
adap-
tors
2
3
3
4
4
4
5
50
Ceiling swirl diffuser,
type 148 37BB0B* 01
Round, coated white, for connection
to a flexible pipe, ø 180 mm
Weight (net) in kg
4
4
4
4
4
4
4
50
Air duct angled section 90°,
type 148 35BB0B* 03
Short bend, e .g . with ceiling arrangement
as a transition from horizontal to vertical
ductwork
Weight (net) in kg
A
B
560
530
5
710
680
5
860
830
7
1010
980
8
1160
1130
9
1310
1280
10
1710
1680
12
1) Insert model for *
Содержание Venkon EC
Страница 2: ...Venkon EC 115V 2 2 ...
Страница 81: ...81 Venkon EC 115 V 81 ...
Страница 82: ...Venkon EC 115V 82 82 ...
Страница 83: ...83 Venkon EC 115 V 83 ...