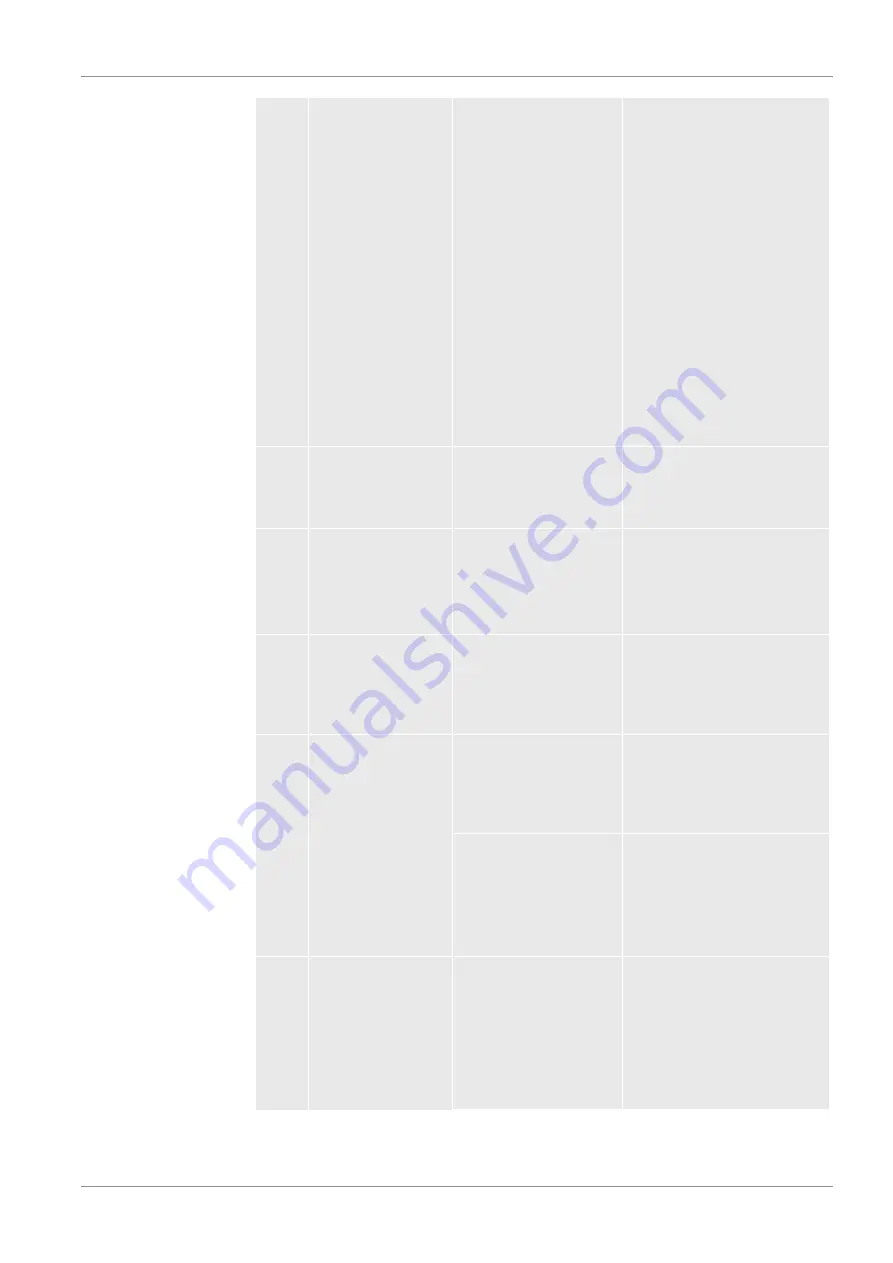
INFICON
Warning and error messages | 10
T-Guard2_Operating-instructions-jina85en1-13-(2009)
77 / 90
W45
He concentration
too high
At the time of the purge
procedure, there is too
much helium before or
in the measurement
line.
The device interrupts
the purge procedure
prematurely to protect
the sensor.
The measurement
chamber was not
sufficiently purged
before the
measurement.
Purge the measurement
chamber with outside air or
nitrogen and initiate another
sensor purge procedure
using the PLC input or the
RS232 command.
Purge the measurement
chamber more intensively
before the measurement.
W50
No I•Stick available
I•Stick was not
connected at start-up
I•Stick is defective
Switch the device off and
back on again, this time with
the I•Stick inserted
W52
I•Stick parameter
lost!
Check the settings!
I•Stick removed during
operation
I•Stick is defective
Check your settings
Switch the device off and
back on again, this time with
the I•Stick inserted
W59
Overflow of
EEPROM
parameter queue!
May occur if a software
update to an older
version is carried out
Restart the device.If the
problem still exists, contact
the INFICON customer
service.
W60
All EEPROM
parameters lost!
Check your
settings!
New EEPROM was
installed, EEPROM on
the system board is not
programmed.
All settings in the software
menu are reset to factory
settings. Modify your settings
again.
If the message occurs
constantly during start-
up, the EEPROM on the
system board is
defective.
Contact INFICON customer
service.
W61
EEPROM
parameter
initializing!
Software update carried
out and new
parameters introduced
Warning, newly
introduced parameters
listed below.
Confirmation required
Содержание 540-200
Страница 2: ...INFICON GmbH Bonner Strasse 498 50968 Cologne Germany ...
Страница 86: ...15 China RoHS INFICON 86 90 T Guard2_Operating instructions jina85en1 13 2009 15 China RoHS ...
Страница 89: ......
Страница 90: ......