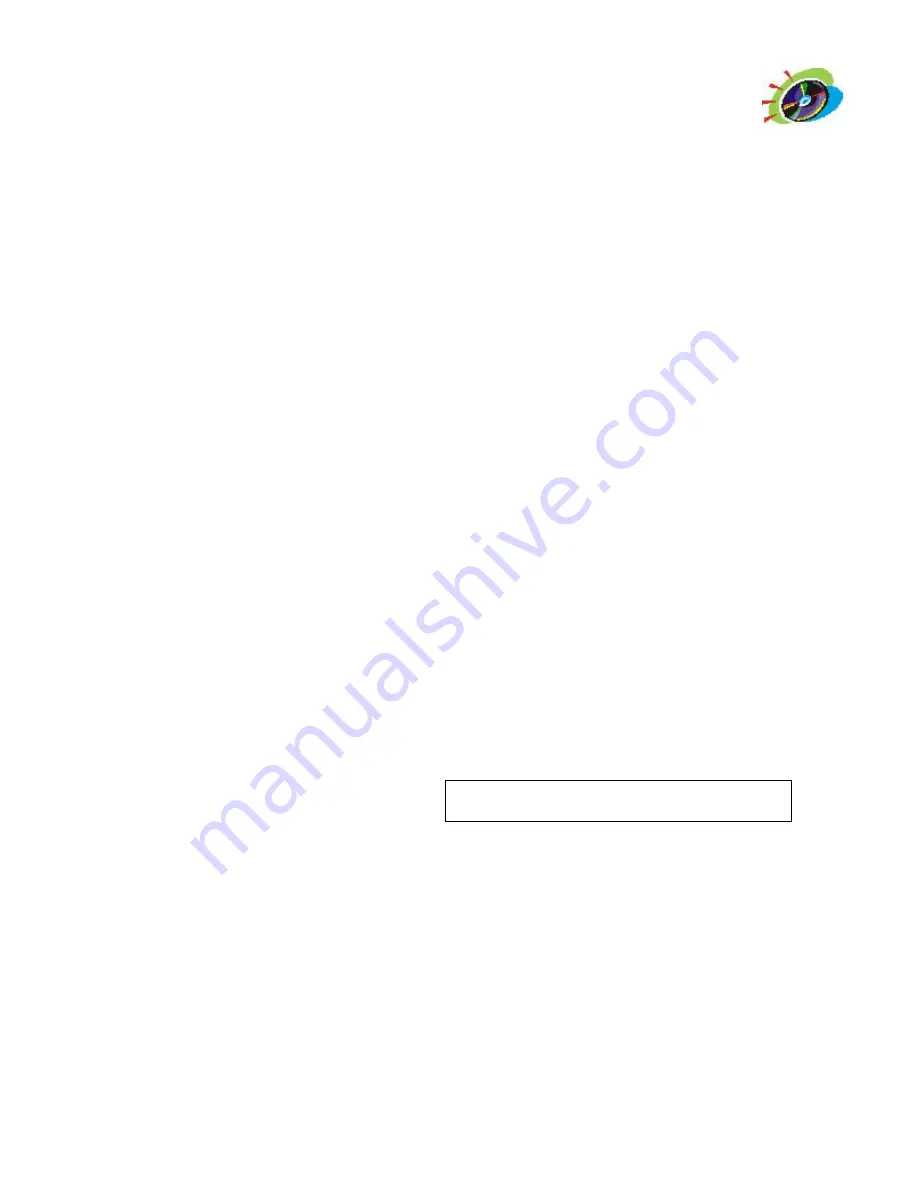
704-0101-761
Autobend 6
Installation Manual
Revision E
November, 1999
Installation Manual
Autobend 6
This manual pertains to the Autobend Control System:
(Record Serial Number here)
Hurco Companies, Inc. reserves the right to incorporate any modifications
or improvements in machines and machine specifications which it
considers necessary, and does not assume any obligation to make any said
changes in machines or equipment previously sold.
Hurco products and services are subject to Hurco’s then current prices,
terms, and conditions, which are subject to change without notice.
Содержание AB6
Страница 3: ...iv Revision E Hurco...
Страница 5: ...vi Revision E Hurco...
Страница 13: ...Installation Manual xiv Revision E Hurco...
Страница 39: ...Installation Manual 1 24 Revision E Hurco...