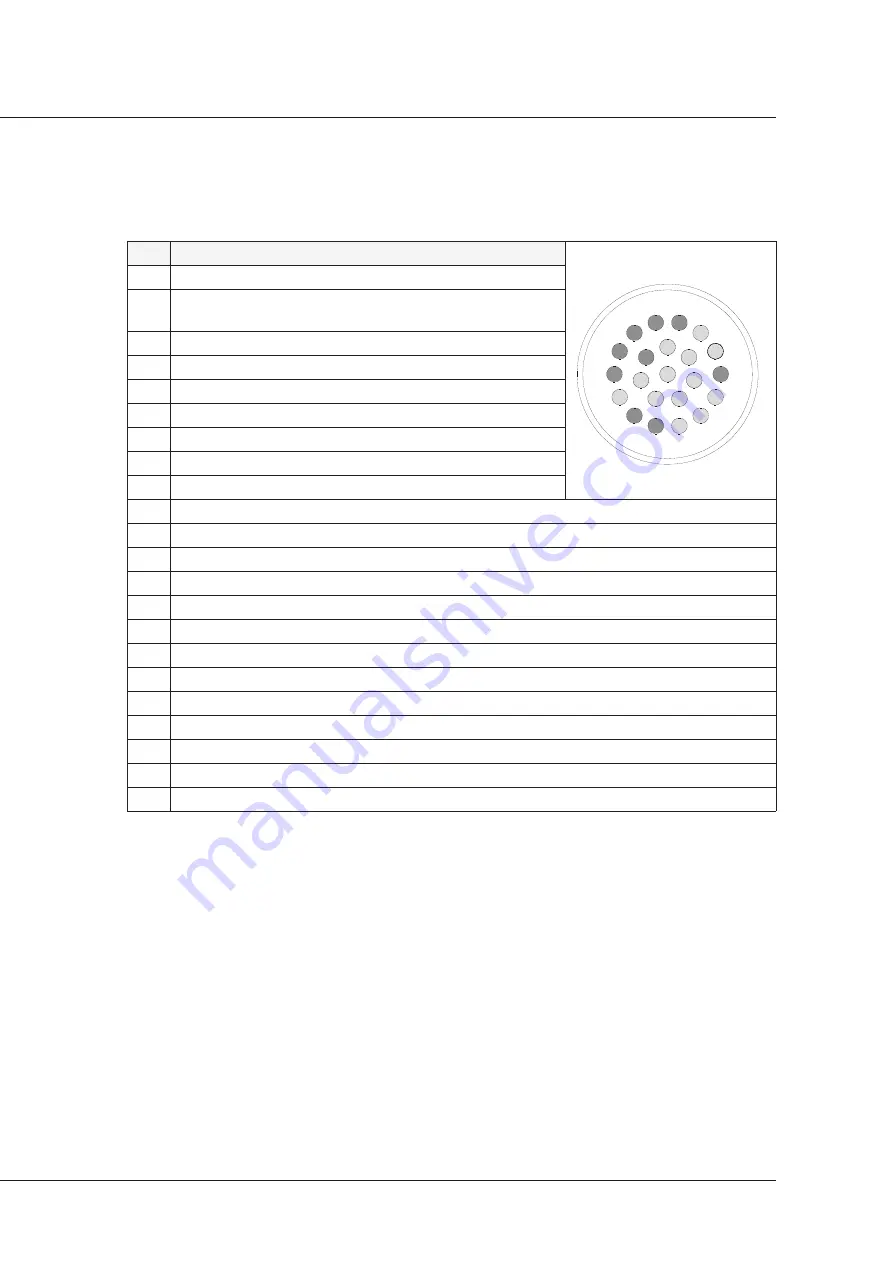
5 Installation and commissioning
HSD S.p.A. © - h0104k01a.fm120718
113
Signal connector diagram (fixed part)
PIN
DESCRIPTION
user side view
1
Sensor S2 output
2
ISO versions: sensor S1 output
HSK versions: sensor S1+S4 output
3
Sensor S3 output*
*
Present in certain versions only.
4
+24V
DC
power supply to S1, S2, S3*
5
+24V
DC
power supply to button indicator light
6
0V power supply to S1, S2, S3*
7
+24V
DC
power supply to button
8
Button output
9
Not used
10
Not used
11
0V power supply to button and indicator light
12
Not used
13
Not used
14
For HSK versions only: sensor S1 output
15
A+ encoder*
16
A- encoder*
17
B- encoder*
18
0V encoder*
19
Z+ encoder*
20
Electricity supply** to encoder*
**
For the encoder supply voltage, refer to the electrospindle technical datasheet.
21
B+ encoder*
22
Z- encoder*
7
14
1
2
13
15
12
3
16
8
21
22
20
4
17
11
18
5
19
10
6
9
Содержание ES779
Страница 2: ......
Страница 4: ...Information about the publication 4 HSD S p A H5801H0118 fm120718 ...
Страница 12: ...Table of contents 12 HSD S p A H5801H0118TOC fm120718 ...
Страница 13: ...Preliminaries ...
Страница 14: ......
Страница 27: ...Descriptions ...
Страница 28: ......
Страница 88: ...3 Technical specifications and main parts 88 HSD S p A h0102k01a fm120718 ...
Страница 121: ...Adjustment and Maintenance ...
Страница 122: ......
Страница 186: ...9 Replacing components 186 HSD S p A h0108k01a fm120718 ...
Страница 187: ...Appendices ...
Страница 188: ......
Страница 196: ...C Disposal 196 HSD S p A h0109k00a fm120718 ...
Страница 199: ......