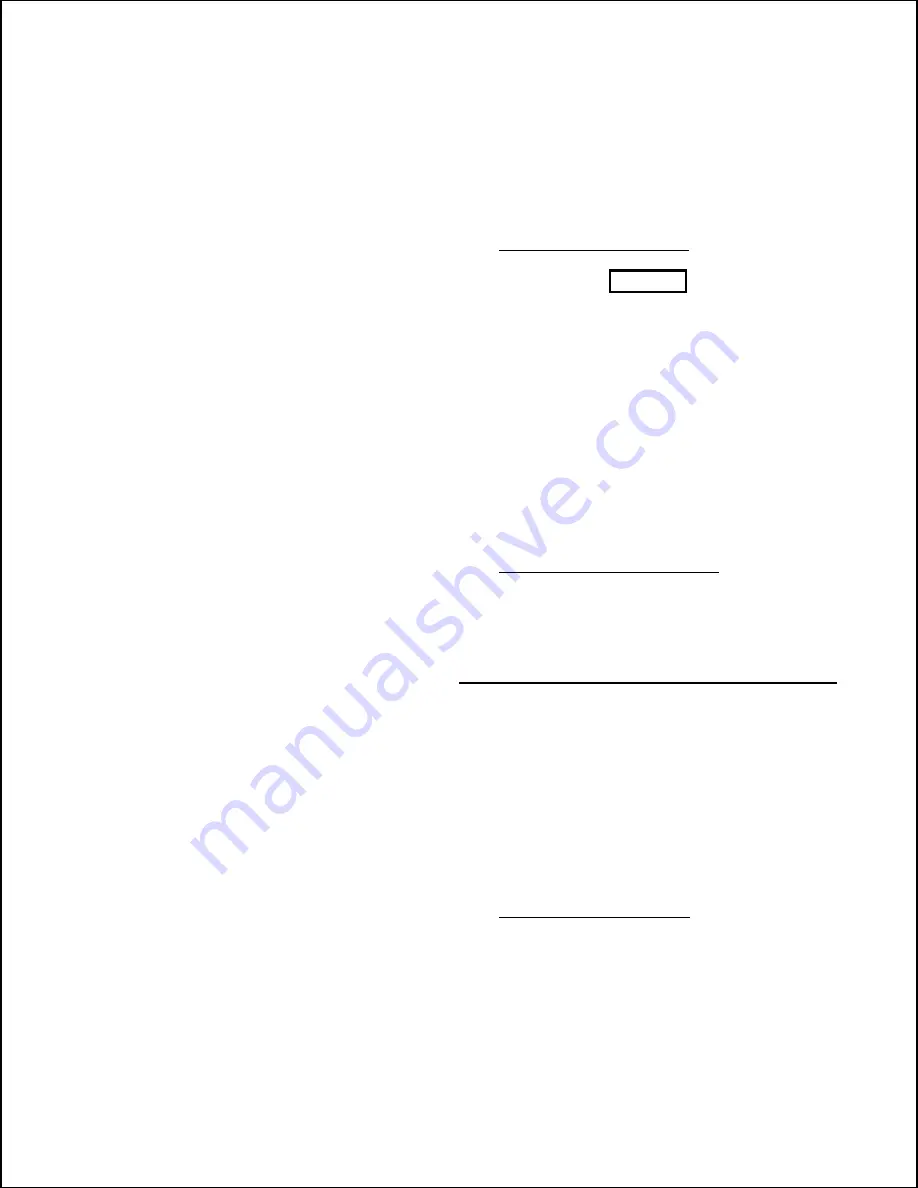
The following test applies to all MOSFET’s used in the transmit-
ter, but is not necessarily applicable to MOSFET’s used in other
equipment.
The MOSFET’s used in the transmitter may be checked with an
Ohmmeter. However there is a requirement which restricts the
use of some Ohmmeters. If the battery voltage is too low (under
3V) or too high (over 20V) the Ohmmeter cannot be used. A
battery voltage less than 3V will not give an operational check
of the transistor and a battery voltage greater than 20V may result
in damage to the transistor under test. A Simpson 260, which uses
a 9V battery on the Rx10k scale works quite well.
This test will show how a MOSFET can be switched “on” and
“off” by charging and discharging the gate of the MOSFET.
Connect the positive lead of the Ohmmeter to the drain or case
of the transistor. Connect the negative lead to source. Alternately
touch a jumper from gate to source and then from gate to drain.
The Ohmmeter should read towards infinity or at least 2M Ohms
when the MOSFET is switched off and less than 90k Ohms when
the MOSFET is switched on. (To switch the MOSFET on hard,
near zero Ohms, use +5 VDC gate to source signal.) When doing
this test, lay the MOSFET on a flat surface or hold sides of the
case. The resistance of your finger tips and skin will affect the
readings when you touch the leads.
5.4.3.3
Replacing MOSFET’s
When repairing an RF amplifier, it is recommended that all four
MOSFET’s of the failed half of the RF amplifier be replaced.
Even though only one or two of the four MOSFET’s are found
to be shorted, the remaining MOSFET’s may have been stressed
internally and may fail when supply voltage is reapplied. The
repair process would then have to be repeated which can be very
frustrating. A Blown fuse on one half of the amplifier does not
affect the other half of the amplifier.
MOSFET’s that appear to be undamaged after testing should be
kept as spares for use if new replacements are not available. Also
keep in mind that the amplifiers used in the Driver stage and
Power Amplifier stage are identical except that the Driver Mod-
ules operate at half voltage. This allows you to rotate a repaired
RF amplifier into a Driver position if so desired.
NOTE
In most cases, the transistor will stick to the heatsink because of
seal created by the transistor pad. This seal will have to be bro-
ken before a heatsink can be removed. Pry the transistor out,
away from its heatsink. DO NOT TRY TO PRY THE HEATSINK
AWAY FROM THE PC BOARD WITH TRANSISTORS STUCK
TO THE HEATSINK OR THE PC BOARD MAY BE DAMAGED
AND THE HEATSINK MAY DISTORT. Sometimes the transistor
pad will tear when the seal is broken. Remove stuck pieces and
replace the pad.
a. Remove all the screws from heatsinks and transistors.
b. Remove the heatsinks one at a time starting with the outer
most sink. Break seals on transistor pads as each pair is
exposed.
c. Replace failed transistors. Save and reuse the ferrite bead
on the center leads of Q3/Q10 and Q4/Q11. Do not solder
leads until heatsinks are in place.
d. Reattach heatsinks in reverse order as they were removed.
Tighten heatsink and pc board screws first and then tighten
transistor screws (torque to 3 inch-lbs).
e. Make sure the ferrite beads are on the center leads of
Q3/Q10 and Q4/Q11.
f. Solder transistor leads and trim.
g. Replace blown fuse(s).
5.4.4
RF Drive Splitter Removal
WARNING
ENSURE ALL PRIMARY AC VOLTAGE HAS BEEN REMOVED
FROM TRANSMITTER AND A GROUNDING STICK IS USED TO
GROUND ALL POINTS WHERE AC OR RF POWER HAS BEEN
APPLIED BEFORE PROCEEDING WITH THE FOLLOWING PRO-
CEDURE.
a. Remove the Driver Compartment rear door.
b. Remove all RF drive cable assemblies from the RF Drive
Splitter.
c. With a 9/16" socket wrench, remove the bolt that connects
the splitter to the Driver Combiner output rod.
d. Remove the standoffs for the cable support ring in the four
corners of the splitter and remove the splitter.
5.4.5
RF Drive Splitter Replacement
Replacement of the RF Drive Splitter is the reverse of the removal
process. Make sure all drive cables are fully inserted and locked
into their sockets.
5.5
Boards Which Require Preset Switch
Settings or Jumper Plug Positions
The following boards have no adjustments, but may have jump-
ers or switches that can be preset to match the settings on the
board being replaced.
•
Modulation Encoder (A37)
•
Controller (A38)
•
Driver Combiner/Motherboard (A14)
•
Binary Combiner/Motherboard (A8)
•
Main Combiner Motherboards (A5-A7)
5.5.1
Modulation Encoder (A37)
When replacing the Modulation Encoder A37, make sure that
binary output jumpers are all in place. Make sure the gold
jumpers for Big Step encoder signals 33 through 96 (P-1 through
P-6) are in place. A FlexPatch™ jumper should be in place from
P-15 to P-10. Make sure that P20 is connected between J20-1&2
and P21 is connected between J21-1&2. Extra FlexPatch™
jumpers can be stored in P9.
NOTE
To assure the proper connections for J1 through J8, consult
drawing number 839-7855-151.
DX-25U
5-4
888-2297-002
Rev. Z1: 06-02-00 Additional info to ECN 46105
WARNING: Disconnect primary power prior to servicing.
Содержание DX 25U
Страница 2: ......
Страница 10: ......
Страница 28: ......
Страница 32: ......
Страница 46: ......
Страница 58: ......
Страница 82: ......
Страница 150: ......
Страница 158: ......
Страница 166: ......
Страница 174: ......
Страница 176: ......
Страница 196: ......
Страница 206: ......
Страница 212: ......
Страница 218: ......
Страница 270: ......