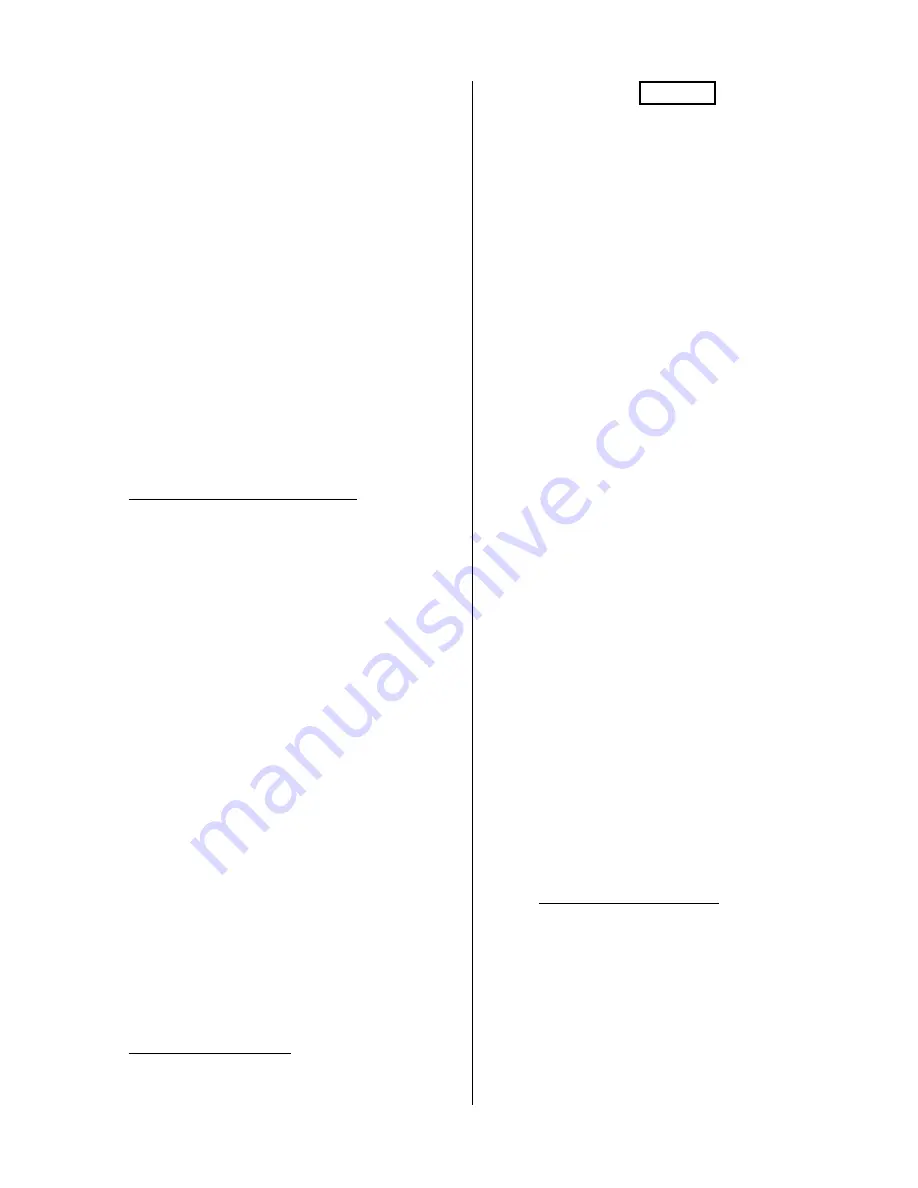
d. Insert the free end of the FlexPatch™ cable into the
INPUT signal side from where the jumper plug was
removed for step RF90.
CAUTION
WHEN USING FlexPatch™ WITH THE TRANSMITTER OPERAT-
ING, MAKE SURE THE FlexPatch™ CABLE IS INSERTED FIRST
INTO THE INPUT JACK OF THE MODULE TO BE SUBSTITUTED.
THEN INSERT IT INTO THE JACK OF THE STEP 90 AMP. THIS
WILL PREVENT INADVERTENT TURN-ON AND POSSIBLE FAIL-
URE OF THE RF AMPLIFIER SHOULD THE FlexPatch™ JUMPER
INADVERTENTLY TOUCH ANOTHER COMPONENT ON THE
MODULATION ENCODER.
If additional RF amplifiers need to be substituted, the next
lowest “Big Step” is selected. Example: Three FlexPatch™
substitutions would use steps RF90, RF89, and RF88 as the
substitute amps.
6.31.5
Using FlexPatch™ for Isolating Modulation
Encoder/RF Amplifier Problems
The FlexPatch™ feature can also be useful in determining
where a fault exists if the fault is not made apparent by an
illuminated LED on an RF amplifier. For example during trou-
bleshooting higher than normal distortion, it is discovered that
on the demodulated audio signal, a missing step is noted at Step
6. See paragraph entitled “Finding A Missing Step.” The LED
on the Step 6 RF amplifier is not illuminated, indicating that it
is at fault. The next step is to physically exchange it with a spare
module. If this does not fix the problem and the fault still exists
at Step 6, the gold jumpers are now removed from the Modula-
tion Encoder for Step 5 and Step 6. Jumper the left hand side
(Encoder output) of the step 6 jack to the right hand side (rf
amplifier input) of the step 5 jack. Connect the step 5 encoder
output (left) to the step 6 RF amplifier input jack (right). Refer
to the Modulation Encoder schematic. Note on the schematic
that the RF amplifier input side of the FlexPatch™ jacks does
go through some driver circuitry on the Modulation Encoder.
After performing this patching, it is noted that the error on the
envelope now occurs at the Step 5 interval and not Step 6. This
indicates that the modulation encoder drive signal for Step 5 that
is now going to the Step 6 RF amplifier through the Modulation
Encoder drive circuitry, is not operating. This says that the
Modulation Encoder drive circuitry for Step 6 has failed. The
most likely suspect is U5-4.
In conclusion, by using the Modulation Encoder schematic,
with careful thought, it is possible to troubleshoot the circuitry
further with FlexPatch™ before attempting time consuming
substitutions or circuit measurements.
6.31.6
Measuring Drive Level
This procedure is used to measure the RF drive levels to the PA
Modules. This should be done if problems are suspected to be
caused by improper drive level.
WARNING
ENSURE ALL AC PRIMARY POWER IS REMOVED FROM
TRANSMITTER AND THAT THE GROUNDING STICK HAS BEEN
USED TO DISCHARGE ANY RESIDUAL POTENTIAL WHERE
POWER HAS BEEN APPLIED BEFORE PERFORMING THE FOL-
LOWING STEPS.
a. Remove all primary AC power from the transmitter. Re-
move the rear access panel from the RF Amp Compart-
ment and remove fuses F1 through F9 on the A24 Fuse
Board, F1 through F8 on the A25 Fuse Board and F20 on
transformer T1.
b. Locate RF amplifier RF33 (bottom left RF amplifier). Use
a 10x scope probe with an extended tip, Harris part
#610-1131-000, and connect it to the anode of CR3
through the interlocked inner door. Connect the ground
clip of the probe to the interlocked door.
c. Reapply primary AC power and turn the Low Voltage on
with CB1 and CB2. Depress the LOW power button and
note that the PA Power Supply energizes, as indicated on
the front panel multimeter, but no RF power or PA current
is indicated.
d. With the scope DC coupled, note that an RF sine wave is
now displayed on the scope. The waveform should normally
measure from 21 to 24 Vp-p and should be centered on the
0.0VDC line of the scope. The drive level may be lower than
20Vp-p at this time. If the waveform falls totally below the
0.0VDC line of the scope, the amplifier is turned OFF. See
Figures 6-4 and 6-5 for drive waveforms.
NOTE
When measuring RF amplifier drive amplitudes or phasing, the
amplifier to be measured must be turned “ON” to give a correct
drive measurement. The drive waveform of an “OFF” amplifier
will be below 0.0VDC and the peaks will probably be clipped.
Place P1 on the Analog Input Board in the TEST position and
depress the RAISE button until all PA Modules are “ON”.
e. Now that a measurement of the RF drive to RF33 has been
made, the RF drive of any other RF amplifier that needs
to be measured can be performed by repeating the above
steps. Remember that the anode of CR3 is the RF drive
on the “A” side of the amplifier and the anode of CR4 is
the RF drive to the “B” side of the amplifier. Refer to
SECTION V, Maintenance, for additional information on
RF drive characteristics.
6.31.7
Measuring Drive Phasing
This procedure is used to measure the RF drive phase on the RF
amplifiers. This should be done any time the frequency is
changed or any time problems caused by improper RF drive
phasing are suspected. There are two sections on each RF
amplifier and each section has an individual drive signal. For
proper transmitter operation, the drive phasing on the RF am-
plifiers should be /-5 degrees. Measure the RF drive
phasing with all amplifiers ON as in “Measuring RF Drive
Level.”
a. Set the oscilloscope to DC coupled, 5 Volts per division,
and the trace at the center of the screen.
Section VI - Troubleshooting
Rev. R: 11-11-96
888-2297-002
6-19
WARNING: Disconnect primary power prior to servicing.
Содержание DX 25U
Страница 2: ......
Страница 10: ......
Страница 28: ......
Страница 32: ......
Страница 46: ......
Страница 58: ......
Страница 82: ......
Страница 150: ......
Страница 158: ......
Страница 166: ......
Страница 174: ......
Страница 176: ......
Страница 196: ......
Страница 206: ......
Страница 212: ......
Страница 218: ......
Страница 270: ......