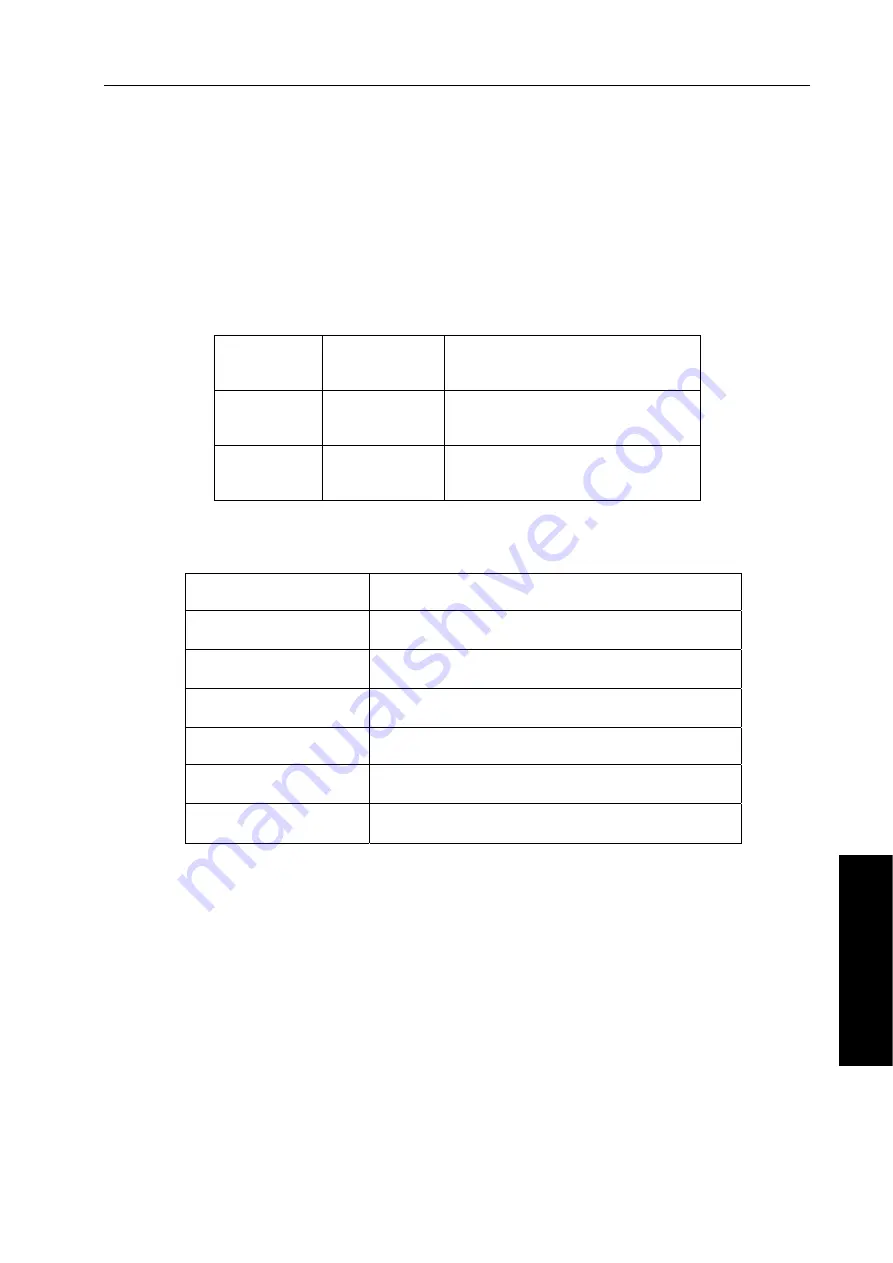
Appendix 8 Stored Pitch Error Compensation Function
347
Appendi
x
set -3 as the compensation amount in the range -40000
~
-50000;
set +7 as the compensation amount in the range -30000
~
-40000;
set 0 as the compensation amount in the range -20000
~
30000;
set -2 as the compensation amount in the range -10000
~
20000
When the X axis moves from -40000 to the reference point, the total pitch error compensation amount
is
(
+3
)
+
(
-7
)
+
(
0
)
+
(
2
)
=
(
-2
)
(3)
Pitch error compensation of rotary axis
When the pitch error compensation is performed for the 4th axis (when it is rotary axis), the
parameters are set as follows:
Parameter
No.
Contents
Parameter Setting Value
42 Compensation
origin point
0
166 Compensation
interval
6000
The compensation error origin point is 0; compensation interval is 6000. Divide the circle into 60
equal sections, so the compensation can be made every 6 deg. The compensation value is set at
the following 61 compensation points:
Parameter No.
Parameter Setting Value
4000
Compensation amount set between -6°
~
0°
4001
Compensation amount set between 0°
~
6°
4002
Compensation amount set between 6°
~
12°
┆
┆
4059
Compensation amount set between 348°
~
354°
4060
Compensation amount set between 354°
~
360°
The value set by parameter No. 4000 and parameter No. 4060 can be the same. The pitch error
compensation of rotary axis is performed at the speed 110000deg/min(31.2r/min) or below.
The sign “+” or ”-” of pitch error compensation value depends on the moving direction, which
means when the compensation value is “+”, the movement amount adds one compensation value;
when the compensation value is ”-”, the movement amount minus one compensation value. That is,
when the mechanical movement amount contains a error (“+” or ”-”) comparing with the movement
command, a compensation value (“+” or ”-”) is set.
When the error is “+” (excessive movement), the compensation value is ”-”.
When the error is “-” (insufficient movement), the compensation value is ”+”.
(Example)
Содержание GSK983Ma
Страница 124: ......
Страница 130: ...GSK983Ma Milling Machine Center CNC System User Manual 118 Part 1 Programming Rapid traverse Cutting feed ...
Страница 133: ...Chapter Three Programming 121 Part 1 Programming Rapid traverse Cutting feed 6 G82 Drilling cycle boring ...
Страница 143: ......
Страница 185: ......
Страница 209: ...Chapter Four Operation 197 Part 2 Operation ...
Страница 239: ...Chapter Four Operation 227 Part 2 Operation ...
Страница 242: ......
Страница 279: ......
Страница 296: ...GSK983Ma Milling Machine Center CNC System User Manual 284 Part 2 Operation ...
Страница 297: ...Appendix 285 APPENDIX Appendix 1 System Version Display The system version is displayed immediately after power on ...
Страница 371: ...Appendix 11 USB Interface Parameter Transfer Operation ...