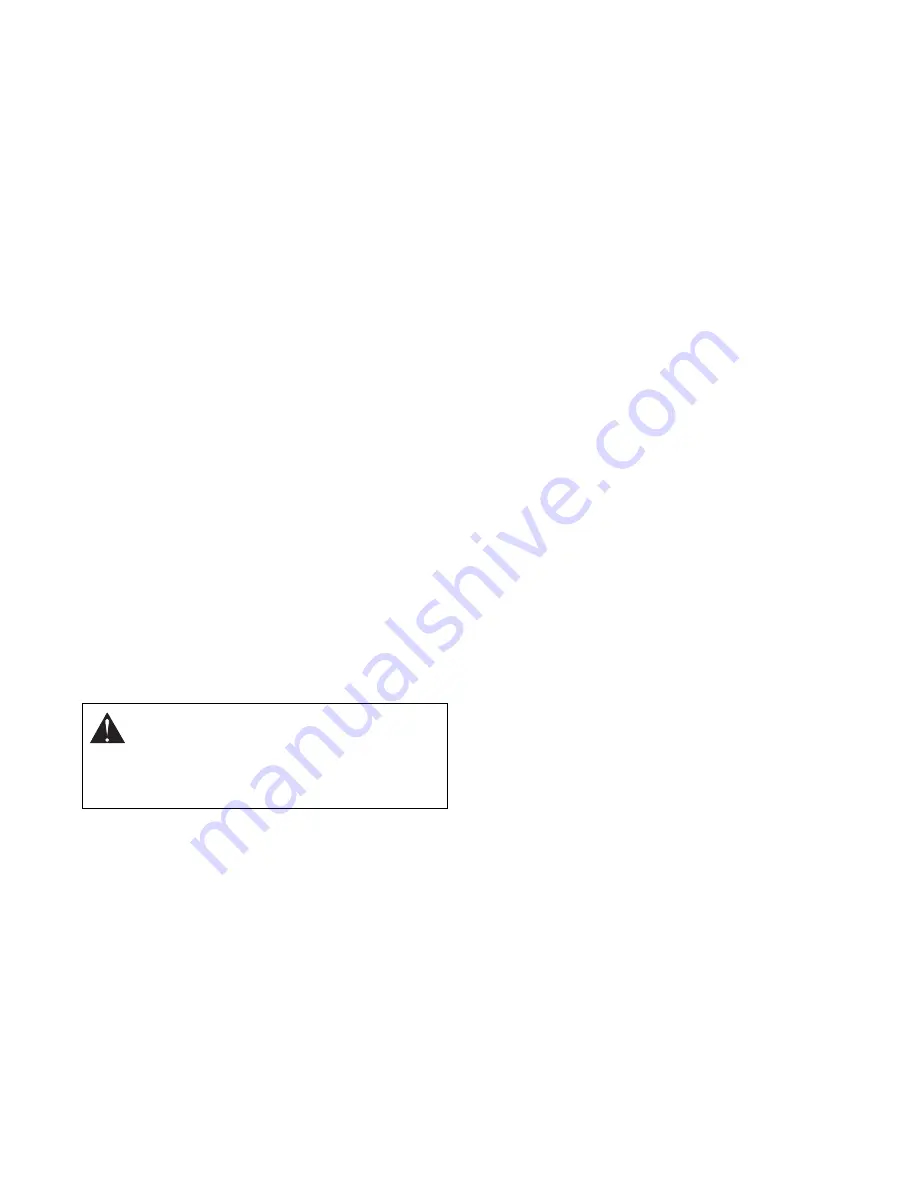
6 - 37
3. Apply a small amount of clean grease to a new dirt
and water seal (20) and press it into the housing
(18) outer bearing counterbore.
4. The large Frame Series ME Torqmotor dirt and
water seal (20) must be pressed in with the lip
facing out and until the seal is flush to 020 inches
(1.51 mm) below the end of housing.
5. Place housing (18) assembly into a soft jawed vice
with the coupling shaft bore down, clamping
against the mounting flange.
6. Assemble a new backup washer (17) and a new
seal (16) with the seal lip facing out, into their
respective counter bores in housing (18). If they
were not assembled in procedure 2.
7. Large Frame, Series ME Torqmotor housing (18)
that did not require replacement of the bearing
package will require that the two “captured” thrust
washers (14) and thrust bearing(15) be unseated
and vertical to the counterbore and that the new
backup washer (17) and new seal (16) be worked
around the thrust bearing package and placed into
their respective counter bores. The seal lip must
face out of the seal counterbore. Be sure the thrust
bearing package is seated correctly after assembly
of the seal and backup washer.
8. Apply masking tape around spines or keyway on
shaft (12) to prevent damage to seal.
9. Be sure that a generous amount of clean corrosion
resistant grease has been applied to the lower
(outer) housing bearing/bushing (19). Install the
coupling shaft (12) into housing (18), seating it
against the second thrust washer (14) in ME Series
housings.
NOTE: The coupling shaft (12) will be flush or just
below the housing wear plate surface on Small Frame,
Series MG and MF Torqmotors when properly seated
while the coupling shaft (12) on large Frame, Series
MB and ME Torqmotors will be approximately .10 inch
(2.54 mm) below the housing wear plate surface to
allow the assembly of thrust bearing (11). The coupling
shaft must rotate smoothly on the thrust bearing
package.
10.Install thrust bearing (11) onto the end of coupling
shaft (12) when servicing an ME Series Torqmotor.
11.Apply a small amount of clean grease to a new
seal ring (4) and insert it into the housing (18) seal
ring groove.
NOTE: One or two alignment studs screwed finger tight
into housing (18) bolt holes, approximately 180
degrees apart, will facilitate the assembly and
alignment of components as required in the following
procedures. The studs can be made by cutting off the
heads of either 318.24 UNF 2A or 5116-24 UNF 2A
bolts as required that are over .5 inch (12.7 mm) longer
than the bolts (1,1A, 1B or 1C) used in the Torqmotor.
12.Install drive link (10) the long splined end down into
the coupling shaft (12) and engage the drive link
splines into mesh with the coupling shaft splines.
NOTE: Use any alignment marks put on the coupling
shaft (12) and engaged the drive link splines into mesh
with the coupling shaft splines.
NOTE: Use any alignment marks put on the coupling
shaft and drive link before disassembly to assemble the
drive link splines in their original position in the mating
coupling shaft splines.
13.Assemble wear plate (19) over the drive link(10)
and alignment studs onto the housing (18).
14.Apply a small amount of clean grease to a new
seal ring (4) and assemble it into the seal ring
groove on the wear plate side of the rotor set stator
(8B).
15.Install the assembled rotor set (8) onto wear plate
(9) with rotor (8A) counterbore and seal ring side
down and the splines into mesh with the drive link
splines.
NOTE: It may be necessary to turn one alignment stud
out of the housing (18) temporarily to assemble rotor
set (8) or manifold (7) over the drive link.
NOTE: The rotor set rotor counterbore side must be
down against wear plate for drive link clearance. A rotor
set without a counterbore and that was not etched
before disassembly can be reinstalled using the drive
link spline pattern on the rotor splines if apparent, to
determine which side was down. The rotor set has a
seal ring groove on the wear plate contact side of the
stator (8B)
16.Apply clean grease to a new seal ring (4) and
assemble it in the seal ring groove in the rotor set
contact side of manifold (7).
NOTE: The manifold (7) is made up of several plates
bonded together permanently to form an integral
component. The manifold surface that must contact the
rotor set has it’s series of irregular shaped cavities on
the largest circumference or circle around the inside
diameter. The polished impression left on the manifold
by the rotor set is another indication of which surface
must contact the rotor set.
17.Assemble the manifold (7) over the alignment
studs and drive link (10) and onto the rotor set. Be
sure the correct manifold surface is against the
rotor set.
CAUTION: The outer bearing (19) is not
lubricated by the system’s hydraulic fluid. Be
sure it is thoroughly packed with the
recommended grease, Ross Gear grease
specification #045236, E/M lubricant #K-70M.
Содержание 950001
Страница 1: ......
Страница 11: ......
Страница 15: ......
Страница 16: ......
Страница 19: ......
Страница 65: ...8 65...
Страница 66: ...8 66...