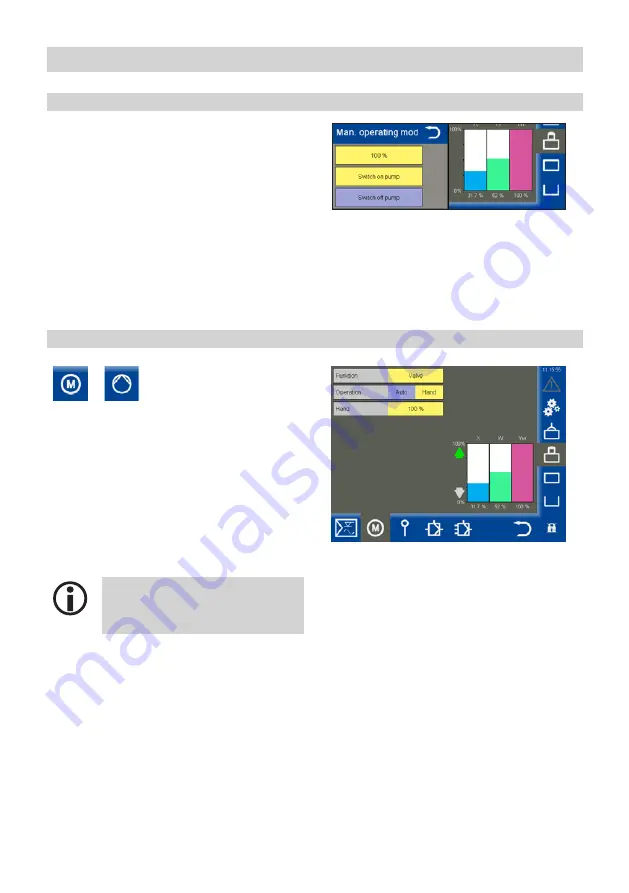
43
URB 60 - Installation & Operating Manual -
819699-00
Tap “Hand” (Manual) to enable manual control.
Then, in the list box, set the control point for man-
ual operation and switch the pump on or off.
Configuring the level controller
Setting manual control or the control point for manual pump operation
Switching actuator operation between automatic and manual
or
Open the
menu.
One of the icons is displayed, depending on which
function is enabled.
Description of parameters:
■
■
Operation (Auto/Manual)
In manual mode, the drive can be operated
manually.
■
■
Hand (= Manual)
Set the drive or valve as desired.
The system automatically switches
back to automatic mode when you
close this window.
Содержание URB 60
Страница 1: ...Original Installation Operating Manual Visual Display and Operating Unit URB 60 819699 00 E N English ...
Страница 65: ...65 URB 60 Installation Operating Manual 819699 00 For your notes ...
Страница 66: ...66 URB 60 Installation Operating Manual 819699 00 ...
Страница 67: ...67 URB 60 Installation Operating Manual 819699 00 ...