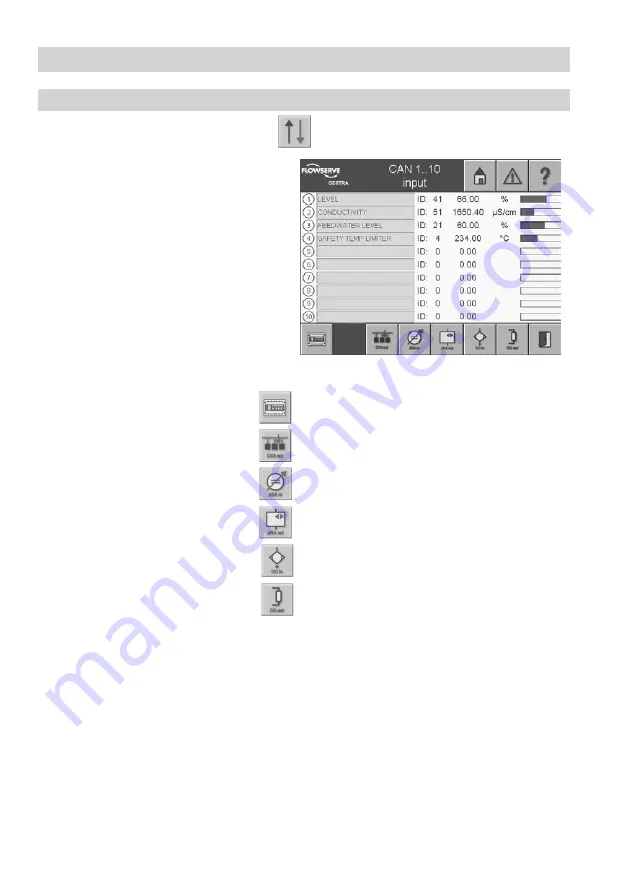
30
Menus of Inputs/Outputs
CAN 1...10 input
To adjust the inputs/outputs, press the button
in the menu
Overview
.
1. The green input fields list the names of the
current CAN inputs. Active inputs are indi-
cated on the left by a yellow number. A node
ID conflict is indicated by a mark at the left
side of the ID setting. To the right of this, the
currently measured value, the associated unit
and the graphical representation are shown.
Current alarms are indicated for each indi-
vidual input by a mark at the left side of the
graphical representation.
2. To change or set the node ID, select the
green input field. A pulldown menu appears
with the possible CAN participants.
If an input is already configured, the name is
shown in the input field. Select the input
field to call up the corresponding menu directly.
n
To show the control equipment, press
n
To call up the CAN outputs, press
n
To show the analogue inputs, press
n
To call up the analogue outputs, press
n
To show the digital inputs, press
n
To call up the digital outputs, press
Содержание SPECTORcontrol
Страница 82: ...82 For your notes ...
Страница 83: ...83 For your notes ...