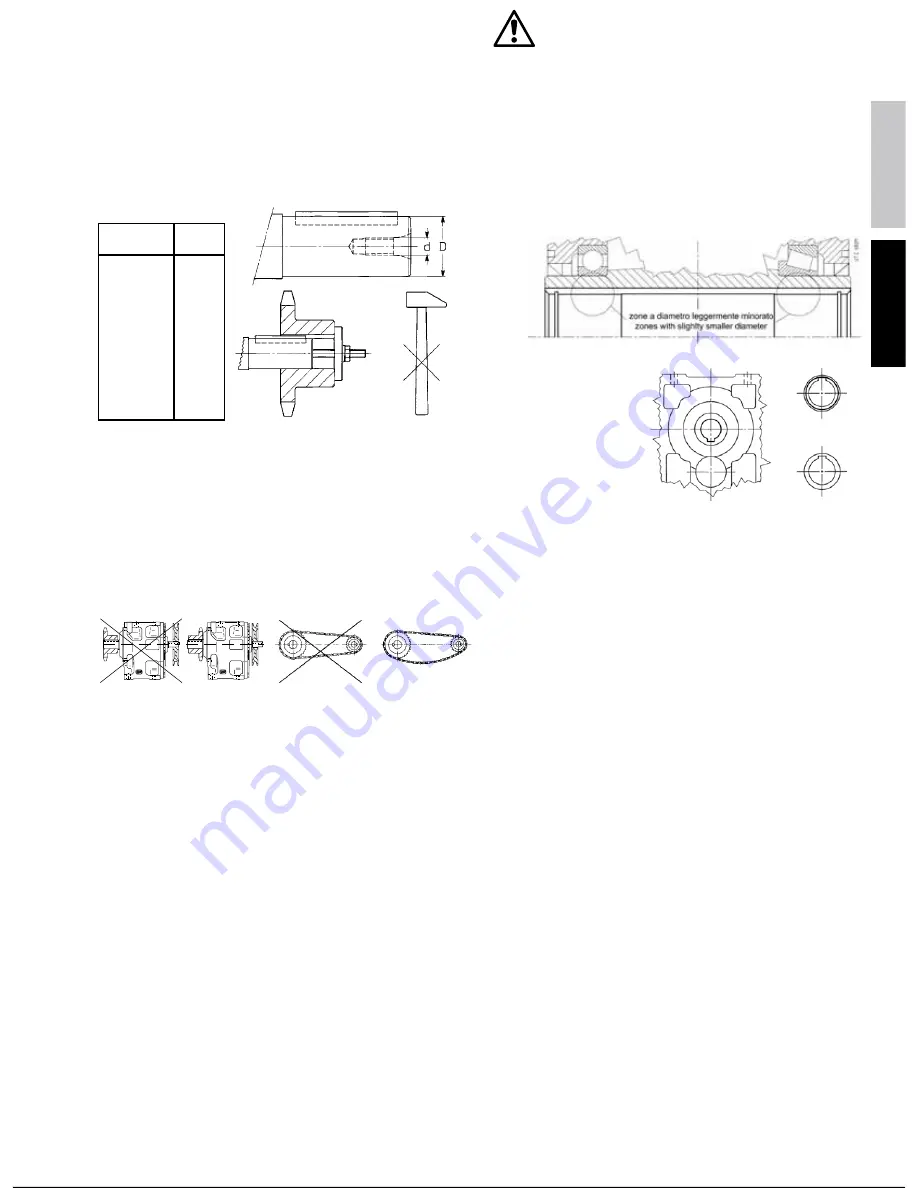
IT
EN
5.2 - Fitting of components to shaft ends
It is recommended that the holes of parts keyed onto shaft ends
should be machined to H7 tolerance; for high speed shaft ends hav-
ing D
ù
55 mm, tolerance G7 is permissible provided that the load
is uniform and light; for low speed shaft end having D
ø
180 mm,
tolerance must be
K7
if load is not uniform and light.
Before mounting, thoroughly clean mating surfaces and lubricate
against seizure and fretting corrosion.
Attention!
Installing and removal operations should be carried out
with the aid of
jacking screws
and
pullers
using the tapped hole at
the shaft butt-end (see table in fig. 2) taking care to avoid impacts
and shocks which may
irremediably damage
the
bearings,
the
circlips
or other parts, for H7/m6 and K7/j6 fits it is advisable that the
part to be keyed is preheated to a temperature of 80
4
100 °C.
The couplings having a tip speed on external diameter up to 20 m/s
must be statically balanced; for higher tip speeds they must be
dynamically balanced.
Where the transmission link between gear reducer and machine or
motor generates shaft end loads, (see fig. 3), ensure that:
– loads do not rise above catalogue values;
– transmission overhang is kept to a minimum;
– gear-type transmissions must guarantee a minimum of backlash
on all mating flanks;
– drive-chains should not be tensioned (if necessary – alternating
loads and/or motion – foresee suitable chain tighteners);
– drive-belts should not be over-tensioned.
5.3 - Shaft-mounting
When shaft mounted, the gear reducer must be supported both axially
and radially (also for mounting positions B3 ... B8) by the machine shaft
end, as well as anchored against rotation only, by means of a reaction
having
freedom of axial movement
and sufficient
clearance in its
couplings
to permit minor oscillations always in evidence without
provoking dangerous overloading on the gear reducer.
Lubricate with proper products the hinges and the parts subject to
sliding; when mounting the screws it is recommended to apply
lock-
ing adhesives
.
For the mounting of the “kit using reaction disc springs” (sizes
ø
125
parallel shafts) use the tapped butt end hole on the shaft end of the
driven machine and the flat machined chamfered surface for com-
pressing and fitting the disc springs into the reaction recess.
Concerning the reaction system, follow the project indications sta-
ted in the technical catalogues Rossi. When-ever personal injury or
property damage may occur, foresee
adequate supplementary
protection devices
against:
– rotation or unthreading of the gear reducer from shaft end of driven
machine following to accidental breakage of the reaction arrange-
ment;
– accidental breakage of shaft end of driven machine.
5.4 - Hollow low speed shaft
For machine shaft ends onto which the hollow shafts of gear reduc-
ers are to be keyed, h6, j6, and k6 tolerances are recommended,
according to requirements.
Important!
The shoulder diameter of the shaft end of the driven
machine abutting with the gear reducer must be at least 1,18
4
1,25
times the internal diameter of hollow shaft. For other data on
machine shaft end, in case of standard hollow low speed shaft,
stepped shaft, with locking rings or bush, with shrink disc see Rossi
technical catalogues.
Attention!
For
vertical ceiling-type
mounting and only
for gear reducers equipped with locking rings or bush, gear
reducer support is due only to friction, for this reason it is
advisable to provide it with a fastening system.
When
installing
and
removing
gear reducers and gearmotors with
hollow low speed shaft incorporating a circlip groove – whether
with keyway or shrink disc – proceed as per fig. 4a and 4b, respec-
tively, on page 12.
Warning
. Even if low speed shafts are principally machined within
H7 tolerance, a check using a plug could detect two areas with
slightly smaller diameters
(see Fig. 5a): this reduction is inten-
tional and does not affect the
quality of keying
- which in fact
will be
improved
in terms of
duration
and
precision
- and it does
not represent an obstacle to the assembly of a machine shaft end
executed according to the usual methods, such as to the one shown
on Fig. 4a.
In order to remove the hol-
low low speed shaft of the
parallel and right angle
shaft gear reducers (this is
the first operation to per-
form when disassembling
the gear reducer) turn the
shaft until the keyway is fac-
ing the intermediate shaft
as indicated in fig. 5b and
push the shaft from the ref-
erence groove side (circum-
ferencial keyway on shaft
shoulder).
The system shown in fig. 4c and 4d, page 12, is good for
axial fas-
tening
; when the shaft end of the driven machine has no shoulder
(as in the lower half of the drawing) a spacer may be located
between the circlip and the shaft end itself. Parts in contact with the
circlip must have sharp edges.
The use of
locking rings
(fig. 4e, page 12) or
locking bush
(fig.
4f
page 12),will permit easier and more accurate installing and removing
and eliminate backlash between the key and keyway.
The locking rings or bush are fitted after mounting and after having
carefully degreased the coupling surfaces. Do not use molybdenum
bisulphide or equivalent lubricant for the lubrication of the parts in
contact. When tightening the bolt, we recommend the use of a
lock-
ing adhesive
.
Respect the tightening torques stated in the table on page 20.
In case of axial fastening with locking rings or bush – especially
when having heavy duty cycles, with frequent reversals – verify,
after some hours of running, the bolt tightening torque and eventu-
ally apply the locking adhesive again.
When fitting with
shrink disc
(fig. 4g, page 12) proceed as follows:
– carefully degrease the surfaces of hollow shaft and shaft end of
driven machine to be fitted;
– mount the gear reducer onto the shaft end of driven machine fol-
lowing the method indicated in fig. 4a, page 12;
– gradually and uniformly tighten the screws of shrink disc by a
continuous sequence (not crossing) and during several phases up
to a torque stated in the table on page 20;
– at operation end verify the screw tightening torque by means of a
dynamometric key (flat, when it is mounted onto machine end).
D
d
Ø
Ø
11
4
00
M 5
14
4
19
M 6
24
4
28
M 8
30
4
38
M 10
42
4
55
M 12
60
4
75
M 16
80
4
95
M 20
100
4
110
M 24
125
4
140
M 30
160
4
210
M 36
240
4
320
M 45
Shaft ends
Fig. 2
U
T.C
886
Fig. 3
Incorrect
Correct
Incorrect
Correct
U
T.C
666
groove side
d
opposite side to groove
Fig. 5b
UT.C 322
UT.C 117
Fig. 5a
Содержание Ariete NS3015P
Страница 1: ...Revision Instructions Manual Translation of the original instructions Ariete NS3015P 13490 0...
Страница 12: ...GEA Niro Soavi...
Страница 19: ...0 0 12 3 3 3 3 4 5 5 6 7 3 8 9 7...
Страница 89: ...GEA Niro Soavi S p A 3C090E0C DOC 3 9 1 3 9 SPECIAL FEATURES OF NON STANDARD MACHINES BLANK PAGE...
Страница 171: ......
Страница 173: ......
Страница 175: ......
Страница 177: ......
Страница 181: ......
Страница 182: ...E E F E F E F E F E E E 79 6 09 10 6 09 10 3 0 60 9 B 01 607 06 10 9 1 6 09 9 6 7 0 706 9 0...
Страница 183: ......
Страница 184: ......
Страница 186: ......
Страница 188: ...PHONE 39 0 521 965411 FAX 39 0 521 242819...
Страница 190: ......
Страница 192: ......
Страница 194: ......
Страница 196: ......
Страница 198: ......
Страница 200: ......
Страница 201: ......
Страница 204: ......
Страница 205: ......
Страница 206: ......
Страница 207: ......
Страница 208: ......
Страница 209: ......
Страница 210: ......
Страница 211: ......
Страница 212: ......
Страница 213: ......
Страница 214: ......
Страница 215: ......
Страница 216: ......
Страница 221: ...GEA Niro Soavi Ref Part Code Description Description 7 01 1 9564 9000 002 MOTORE MOTOR...
Страница 222: ...GEA Niro Soavi Ref Part Code Description Description 7 01 2 9565 2316 562 MOTORE MOTOR...
Страница 275: ...55 PYCCKN PYCCKN...
Страница 276: ...56...
Страница 277: ...57 PYCCKN...
Страница 278: ...58...
Страница 280: ...60...
Страница 281: ...61 PYCCKN...
Страница 282: ......
Страница 284: ...GEA Niro Soavi Ref Part Code Description Description 7 01 3 9533 3011 011 TRASDUTTORE TRANSDUCER...
Страница 289: ...GEA Niro Soavi Ref Part Code Description Description 7 01 4 9533 3012 011 TRASDUTTORE TRANSDUCER...
Страница 294: ...GEA Niro Soavi Ref Part Code Description Description 7 01 5 9533 4064 000 RIDUTTORE GEARBOX...
Страница 296: ......
Страница 316: ...IT EN 1RWH 1RWHV...
Страница 320: ...IT EN...
Страница 322: ...GEA Niro Soavi Ref Part Code Description Description 7 01 6 9550 0000 150 CENTRALINA LUBRICATION UNIT...