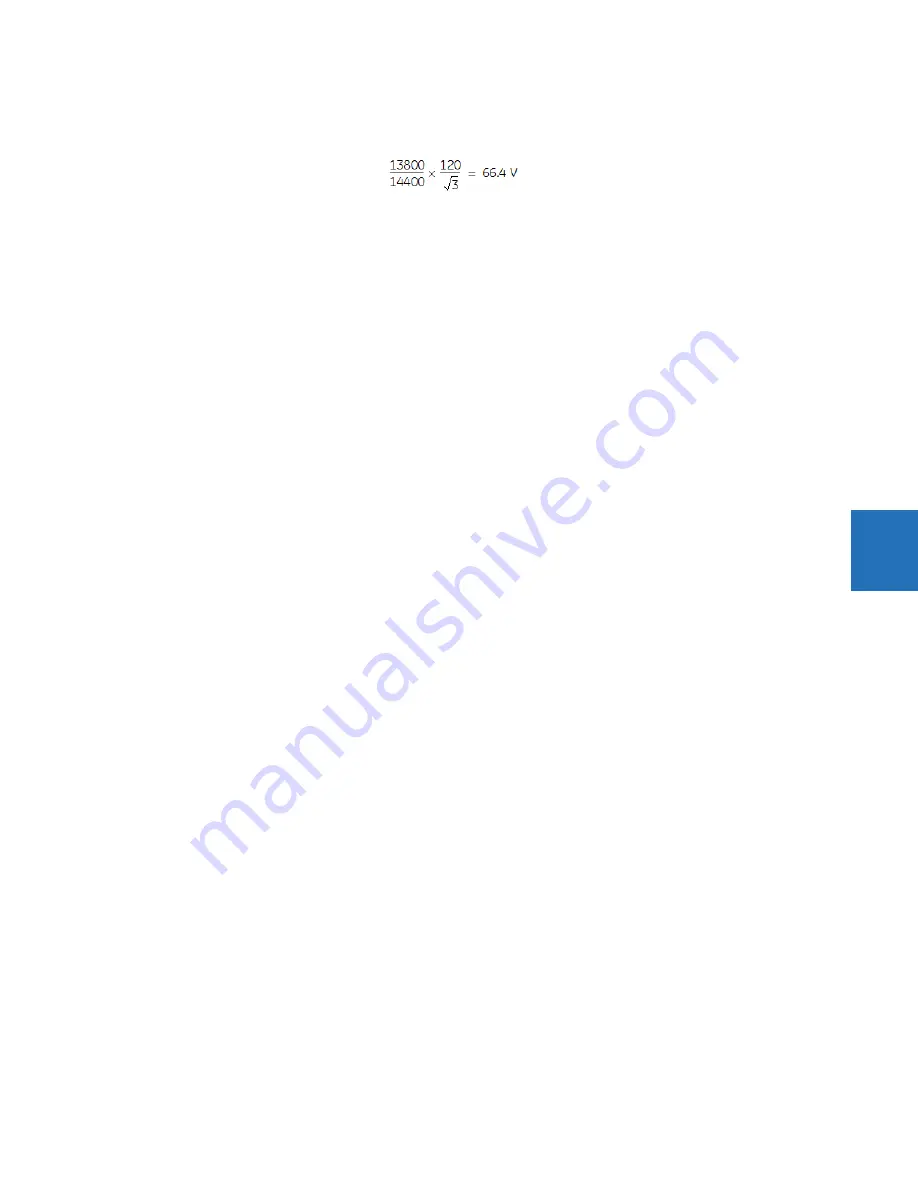
CHAPTER 5: SETTINGS
OVERVIEW
F35 MULTIPLE FEEDER PROTECTION SYSTEM – INSTRUCTION MANUAL
5-5
5
For wye-connected VTs, the primary and secondary base quantities are as before, but the secondary voltage setting (here
a phase-to-ground value) is:
Eq. 5-2
Many settings are common to most elements, outlined as follows:
•
FUNCTION setting
— This setting programs the element to operate when selected as “Enabled.” The factory default is
“Disabled.” Once “Enabled,” any element associated with the function becomes active and all options become
available.
•
NAME setting
— This setting is used to uniquely identify the element.
•
SOURCE setting
— This setting is used to select the AC source to be monitored. See the Introduction to AC Sources
section later.
•
PICKUP setting
— For simple elements, this setting is used to program the level of the measured parameter above or
below which the pickup state is established. In more complex elements, a set of settings can be provided to define the
range of the measured parameters that cause the element to pick up.
•
PICKUP DELAY setting
— This setting sets a time-delay-on-pickup, or on-delay, for the duration between the pickup
and operate output states.
•
RESET DELAY setting
— This setting is used to set a time-delay-on-dropout, or off-delay, for the duration between the
operate output state and the return to logic 0 after the input transits outside the defined pickup range.
•
BLOCK setting
— The default output operand state of all comparators is a logic 0 or “flag not set.” The comparator
remains in this default state until a logic 1 is asserted at the RUN input, allowing the test to be performed. If the RUN
input changes to logic 0 at any time, the comparator returns to the default state. The RUN input is used to supervise
the comparator. The BLOCK input is used as one of the inputs to RUN control.
•
TARGET setting
— This setting is used to define the operation of an element target message. When set to "Disabled,"
no target message or illumination of a front panel LED indicator is issued upon operation of the element. When set to
“Self-Reset,” the target message and LED indication follow the operate state of the element and self-resets once the
operate element condition clears. When set to “Latched,” the target message and LED indication remains visible after
the element output returns to logic 0 until a RESET command is received by the relay.
•
EVENTS setting
— This setting is used to control whether the pickup, dropout, or operate states are recorded by the
event recorder. When set to “Disabled,” element pickup, dropout, or operate are not recorded as events. When set to
“Enabled,” events are created for
<Element> PKP (pickup)
<Element> DPO (dropout)
<Element> OP (operate)
The DPO event is created when the measure and decide comparator output transits from the pickup state (logic 1) to
the dropout state (logic 0). This can happen when the element is in the operate state if the reset delay time is not zero.
Not every operand of a given element in a UR relay generates events, only the major output operands. Elements,
asserting output per phase, log operating phase output only, without asserting the common three-phase operand
event.
5.2.2 Introduction to AC sources
5.2.2.1 Background
A mechanism called a
source
configures the routing of CT and VT input channels to measurement sub-systems. Sources, in
the context of UR series relays, refer to the logical grouping of current and voltage signals such that one source contains all
the signals required to measure the load or fault in a particular power apparatus. A given source can contain all or some of
the following signals: three-phase currents, single-phase ground current, three-phase voltages, and an auxiliary voltage
from a single VT for checking for synchronism.
Содержание F35
Страница 12: ...1 4 F35 MULTIPLE FEEDER PROTECTION SYSTEM INSTRUCTION MANUAL FOR FURTHER ASSISTANCE CHAPTER 1 INTRODUCTION 1 ...
Страница 202: ...4 88 F35 MULTIPLE FEEDER PROTECTION SYSTEM INSTRUCTION MANUAL FLEXLOGIC DESIGN USING ENGINEER CHAPTER 4 INTERFACES 4 ...
Страница 562: ...6 30 F35 MULTIPLE FEEDER PROTECTION SYSTEM INSTRUCTION MANUAL PRODUCT INFORMATION CHAPTER 6 ACTUAL VALUES 6 ...
Страница 576: ...7 14 F35 MULTIPLE FEEDER PROTECTION SYSTEM INSTRUCTION MANUAL TARGETS CHAPTER 7 COMMANDS AND TARGETS 7 ...
Страница 650: ...A 38 F35 MULTIPLE FEEDER PROTECTION SYSTEM INSTRUCTION MANUAL FLEXANALOG ITEMS APPENDIX A FLEXANALOG OPERANDS A ...
Страница 658: ...C 6 F35 MULTIPLE FEEDER PROTECTION SYSTEM INSTRUCTION MANUAL COMMAND LINE INTERFACE APPENDIX C COMMAND LINE INTERFACE C ...
Страница 666: ...iv F35 MULTIPLE FEEDER PROTECTION SYSTEM INSTRUCTION MANUAL ABBREVIATIONS ...
Страница 682: ...xvi F35 MULTIPLE FEEDER PROTECTION SYSTEM INSTRUCTION MANUAL INDEX ...