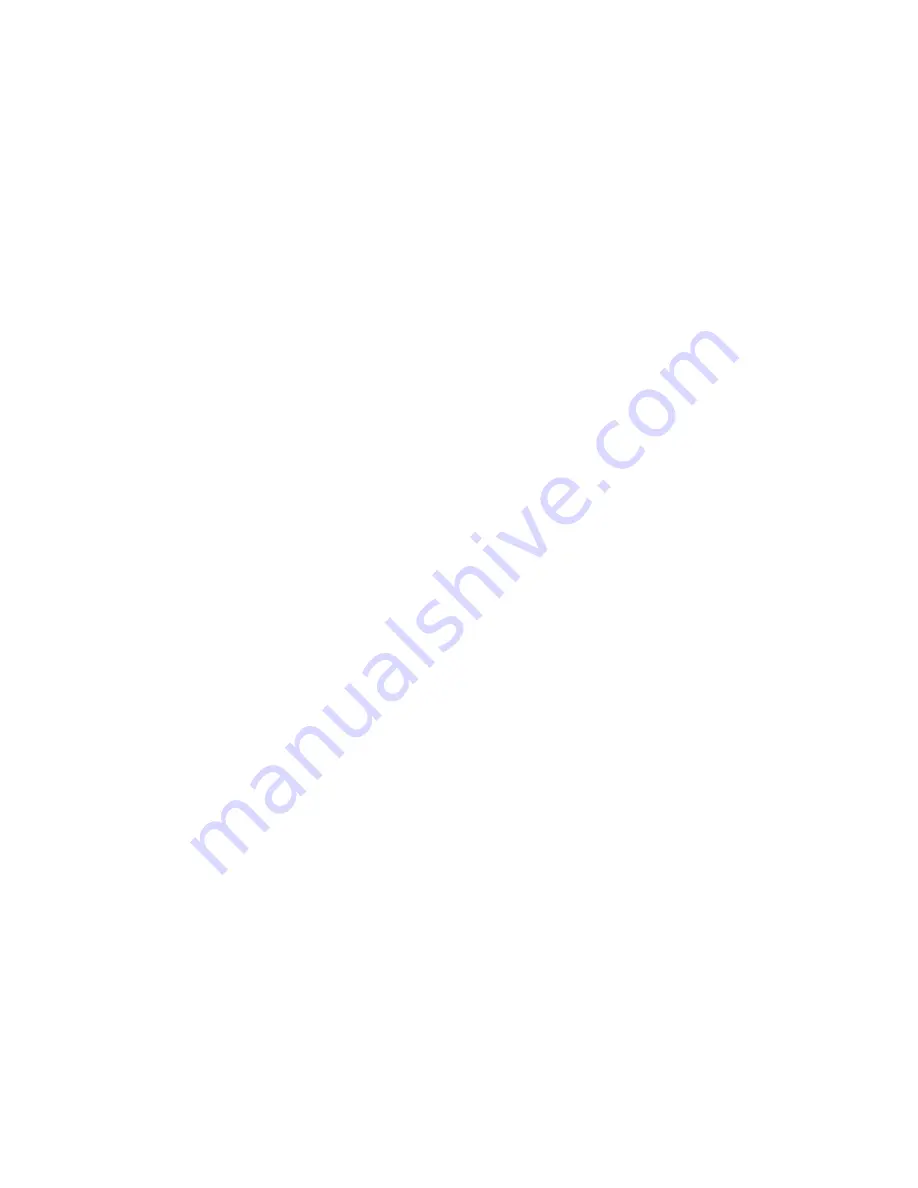
517766
March 2003
- 38 -
Secondary Source:
Motor.
Action
1)
Measure/check the motor harness, connectors and motor for shorts. This
can be done by taking a resistance measurement between phases of the
motor harness at the Motor Control module end. Nominal resistance should
be around 12.2 ohm for Phase 2, 3 & Phase 4. For Phase 5 and 6 Smart
Drive the nominal resistance should be around 32 ohms.
2)
Check the Rotor Positional Sensor, Stator brass bridge terminal point and
associated harness for water, mechanical damage or corrosion.
Tertiary Source:
Motor Controller module.
Action
If all the above show no signs of fault then replace the Motor Controller module.
Also check for water leaks from the cooling chamber or valves that could possibly
come in contact with the Motor Controller and fix the leak before replacing with new
Motor Controller module.
133.
(10000101) Phase 1 to 4 - Repetitive Current Trip
The Motor Controller has detected excess current in the motor or electronic
switches. This fault is a more severe occurrence than Fault Number 132 but has
identical fault sources and fault service procedure.
134.
(10000110) Phase 4 - Single Current Trip & Rotor Position Error
The Motor Controller module has detected an excessive motor current and a Rotor
Position Sensor error simultaneously. See fault codes 130 and 132 for service
procedure.
136.
(10001000) Phase 1 to 6 - Motor Stall
The Motor Controller has been unable to start the motor. Possible causes of this
fault are: Faulty motor harness, faulty or jammed motor, seized bearings or seals,
faulty Motor Controller module, faulty Rotor Position Sensor or harness.
Primary Source:
Wiring.
Action:
Measure / check the motor harness, connectors and motor for discontinuity. This
can be done by taking a resistance measurement between phases of the motor
harness at the Motor Controller module end. Nominal resistance should be around
12.2 ohm for Phase 2,3 & Phase 4
.
For
Phase 5 and 6 onwards the nominal
resistance should be around 32 ohms.
Secondary Source:
Motor.
Action:
1)
Check free rotation of the agitator and basket by rotating by hand. Bearings
and seals may be seized.
2)
Check the Rotor Position Sensor and associated harness for water,
mechanical damage or corrosion.
Tertiary Source:
Motor Controller module.
Action:
If the primary and secondary checks pass inspection then replace the Motor
Controller module.
144.
(10010000) Phase 1 – Motor Controller Software Trap
The Motor Controller has developed a fault.
Содержание ecosmart GWL11
Страница 2: ...517766 March 2003 ...
Страница 21: ...517766 March 2003 21 17 WIRING DIAGRAM ...