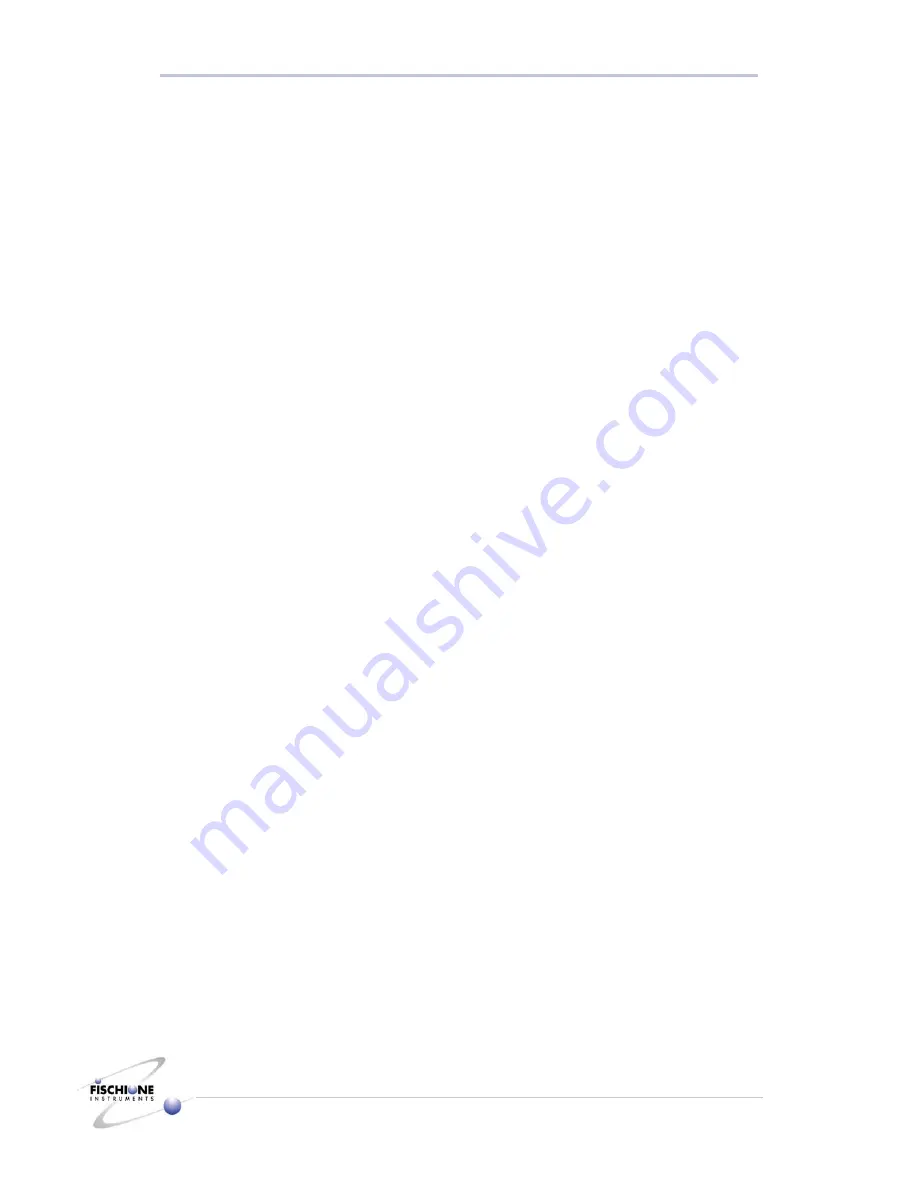
S y s t e m O v e r v i e w
7
Model 1010 Ion Mill
Standard Magnification Version
Gas Flow
The Model 1010 contains an internal, automatic gas control system. Process gas (usually
argon) is connected to the bulkhead fitting located on the rear of the instrument. The
purity of argon should be equal to or greater than 99.998% and supplied at a pressure of
10 psi (69 Mpa).
Two independently controlled mass flow controllers, located in a feedback control loop,
supply the appropriate amount of argon flow to the ion sources (between 0.4 sccm and
1.0 sccm). An internal pressure regulator is pre-set to provide the proper supply pressure
to the mass flow controllers.
The computer continuously monitors ion source performance and provides the
appropriate control signal to the flow controllers. The controllers are supplied with an
inlet voltage of +15 vdc and the control signal is 0-5 vdc proportional.
Water Flow
The high ion energies associated with the HAD (Hollow Anode Discharge)
ion source
benefit from water cooling which both enhances performance and increases the time
interval between routine source maintenance. Cooling water circulates through the
alignment flange, which contains and is in thermal contact with the ion source cartridge.
Water enters the instrument though a bulkhead fitting on the rear panel. A solenoid valve
located within the instrument enclosure is normally closed. When the ion sources are
energized, the solenoid valve opens allowing water flow into the alignment flanges, thus
cooling the ion sources. A solenoid valve conserves water by only permitting flow when
required to cool an energized ion source.
The temperature of the inlet water is not critical but should be maintained b5
°
C
and room temperature. Water flow of approximately 0.5 lpm is recommended. In the
unlikely event of the drain line becoming obstructed, the Model 1010 will not sense the
loss of flow. Therefore, periodically during operation, confirm that water is being drained
from the instrument.
Sample Cooling Capability (Optional)
A sample can be milled in the Model 1010 while actively being cooled to temperatures
approaching that of liquid nitrogen. The source of this cooling capability is an insulated
vessel (or “Dewar”) containing liquid nitrogen. A thermal path is provided by a
conduction rod passing through the Dewar to the rear of the sample stage. The maximum
temperature allowed during milling is selectable. It is selectable through the “Thermal
Safeguard” in the Ion Milling program.
To optimize the sample cooling capability, a vacuum must be maintained in the space
between the walls of the Dewar. Periodically the sample stage heater may need to be
activated to remove absorbed moisture and regenerate the Zeolite® desiccant. These
processes are controlled by the Dewar Bakeout program.
Endpoint Detection Capability (Optional)
The Model 1010 can be programmed to automatically de-energize the ion sources when
either a perforation in the sample is achieved or when the sample permits the
transmission of laser light. The detector circuitry is designed with a variable sensitivity