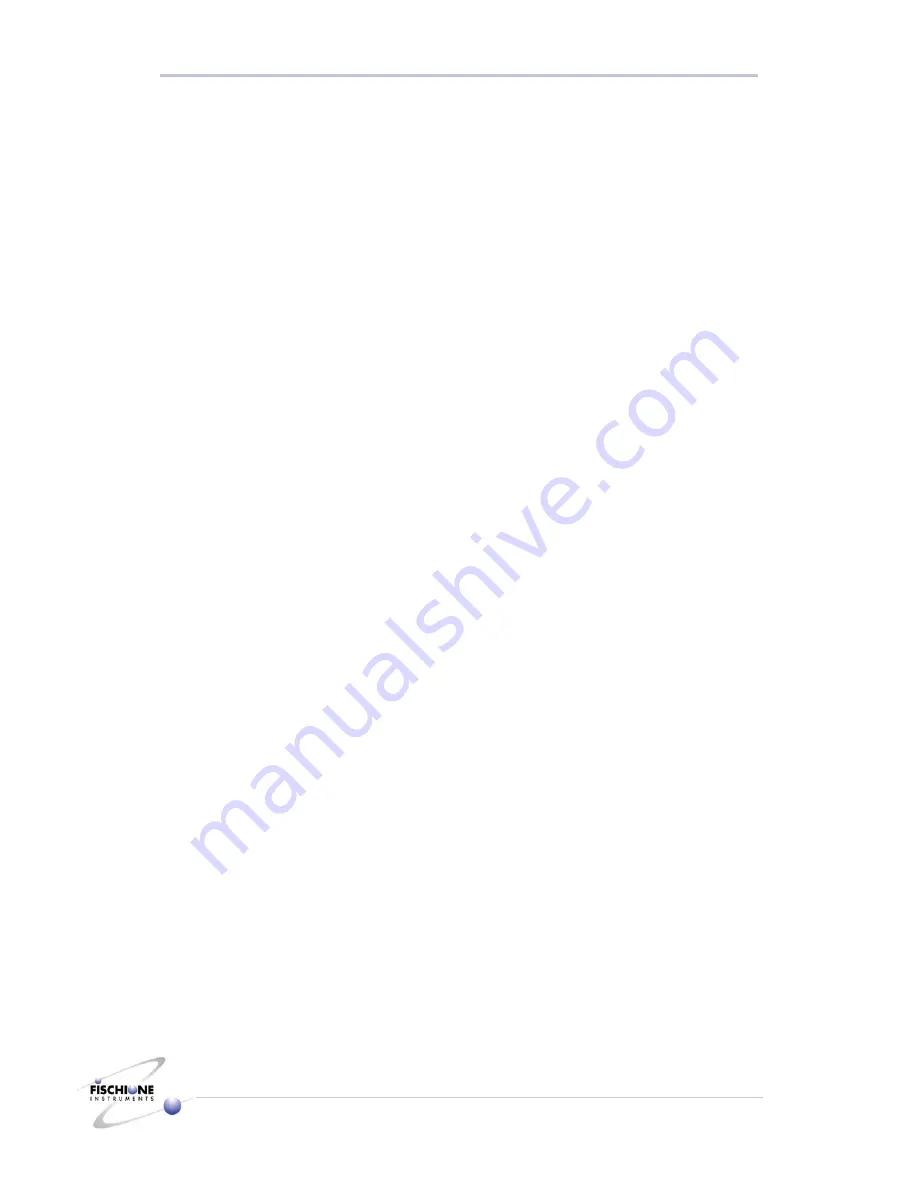
S y s t e m O v e r v i e w
6
Model 1010 Ion Mill
Standard Magnification Version
●
The specimen rotation drive motor.
●
The angle adjustment drive motor.
●
The vacuum pumping port for the liquid nitrogen Dewar flask.
●
The optical pick-up and encoder, which provides the milling angle indication.
Top:
The top chamber surface includes:
●
The top light assembly
Front:
The front of the chamber includes:
•
The electro-mechanical leak valve
•
The chamber access door
Vacuum System
The Model 1010 is equipped with a 70 lps (minimum) turbomolecular vacuum pump. A
fan creates a constant air flow across the turbo pump cooling vanes to minimize the heat
associated with maintaining a vacuum under gas flow conditions. The Model 1010 also
includes an external rough pump. This is a diaphragm pump that provides backing
vacuum for the turbomolecular pump.
With no gas flow, ultimate chamber vacuum is 1 x 10
-6
torr. Under normal milling
conditions, the system vacuum is between 1 x 10
-4
and 2 x 10
-5
torr. Total pump down
time is typically less than four minutes, although this time may vary based on ambient
temperature and relative humidity as well as the length of time that the chamber front
access door was open exposing the chamber to ambient conditions. Pump down times are
also increased following ion source cleaning or chamber maintenance.
The turbomolecular pump is directly mounted to the chamber by two bolts. An inlet
protection screen prevents debris from entering the pump and damaging the turbine
blades.
An electro-mechanical vent valve is installed directly onto the chamber and all venting is
controlled through the computer. Vacuum is sensed by a Pirani gauge and is continuously
indicated in the Ion Milling Program screen. In order to improve ion source performance,
argon flows through the ion sources during the venting process.
The specimen chamber vents through the normally closed solenoid valve located on the
front of the chamber. When the vacuum system is de-energized, both the diaphragm and
the turbomolecular pumps are turned off and voltage is applied to the vent valve. The
vent valve slowly bleeds ambient air into the chamber over approximately 20 seconds to
minimize stress on the rotary turbine blades in the turbo pump.
When liquid nitrogen is being used, venting will not occur until the specimen stage
temperature r10
°
C, to prevent contamination of the specimen.
If the main instrument power switch is turned off while the vacuum system is energized,
the vacuum will be maintained, keeping the chamber sealed and free from ambient
contamination.