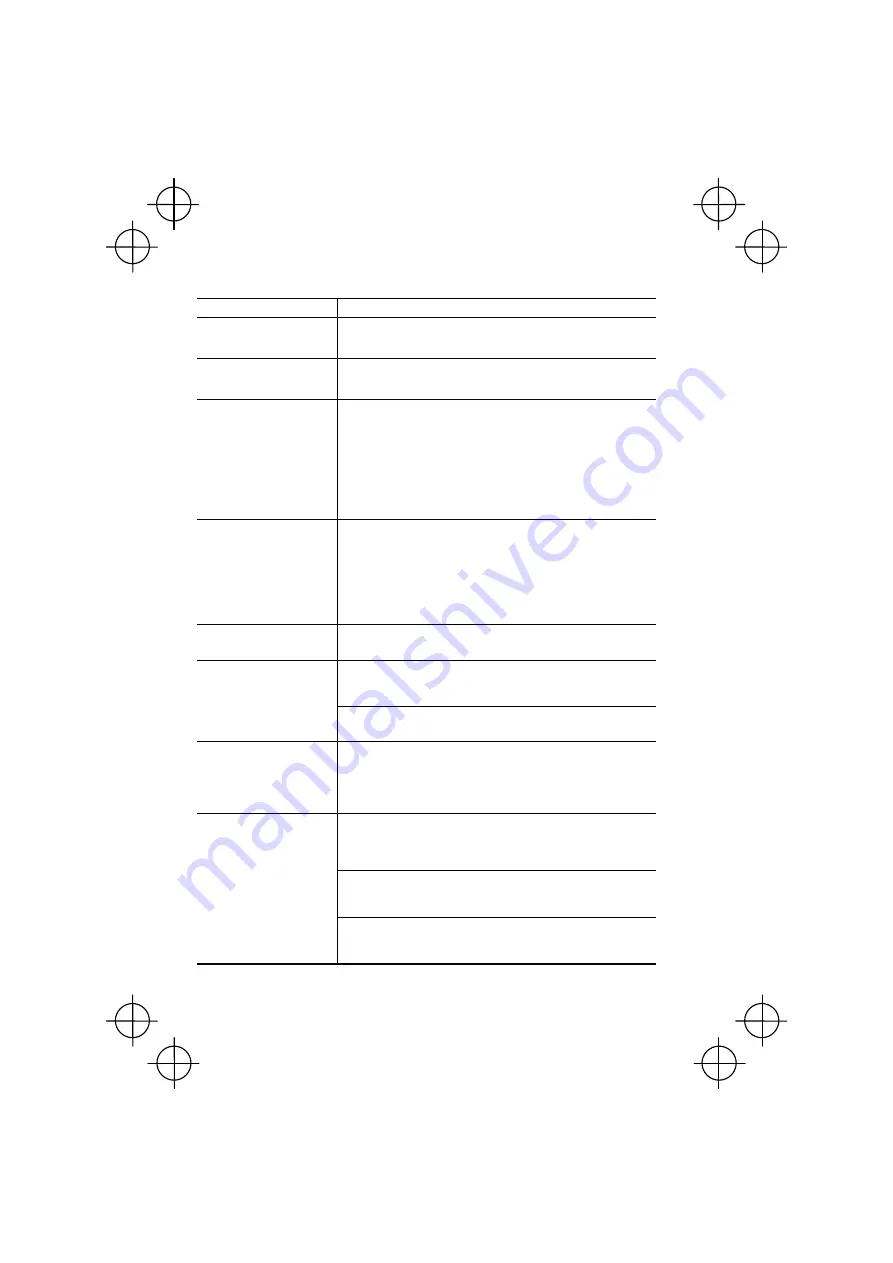
6-4
[ 2 ] The motor rotates, but the speed does not increase.
Possible Causes
What to Check and Suggested Measures
(1) The maximum frequency
currently specified was
too low.
Check the data of function code F03 or A01 (Maximum frequency).
Î
Correct the F03 or A01 data.
(2) The data of frequency
limiter currently specified
was too low.
Check the data of function code F15 (Frequency limiter (High)).
Î
Correct the F15 data.
(3) The reference frequency
currently specified was
too low.
Check the signals for the frequency command entered via the
analog input terminals, using Menu #4 "I/O Checking" on the
keypad.
Î
Increase the reference frequency.
Î
Inspect the external frequency command potentiometers, signal
converters, switches, or relay contacts. Replace any ones that
are faulty.
Î
Connect the external circuit wires to terminals [13], [12], [11], and
[C1] correctly.
(4) A frequency command
(e.g., multistep
frequency or via
communications link)
with higher priority than
the one expected was
active and its reference
frequency was too low.
Check the data of the relevant function codes and what frequency
commands are being received, through Menu #1 "Data Setting,"
Menu #2 "Data Checking" and Menu #4 "I/O Checking," on the
keypad, referring to the block diagram of the drive frequency
generator*.
*Refer to the FRENIC-Mini User's Manual, Chapter 4.
Î
Correct any incorrect data of function code (e.g. cancel higher
priority run commands, etc.).
(5) The acceleration time
was too long or too short.
Check the data of function codes F07 and E10 (Acceleration time).
Î
Change the acceleration time to match the load.
Measure the output current.
Î
Reduce the load (Adjust the dumper of the fan or the valve of the
pump). (In winter, the load tends to increase.)
(6) Overload
Check whether any mechanical brake is activated.
Î
Release the mechanical brake.
(7) Mismatch with the
characteristics of the
motor.
If auto-torque boost or auto-energy saving operation is under way,
check whether the data of P02, P03, P06, P07, and P08 (A16, A17,
A20, A21, and A22) agrees with the parameters of the motor.
Î
Perform auto-tuning of the inverter for every motor to be used.
Make sure that F43 (Current limiter (Mode selection)) is set to "2"
and check the setting of F44 (Current limiter (Level)).
Î
Correct the data of F44. Or, if the current limiter operation is not
needed, set F43 to "0" (disable).
Decrease the value of torque boost (F09), then run the motor again
and check if the speed increases.
Î
Adjust the value of the torque boost (F09).
(8) The current limiting
operation did not
increase the output
frequency.
Check the data of function codes F04, F05, H50 through H53 to
ensure that the V/f pattern setting is right.
Î
Match the V/f pattern values with the motor ratings.