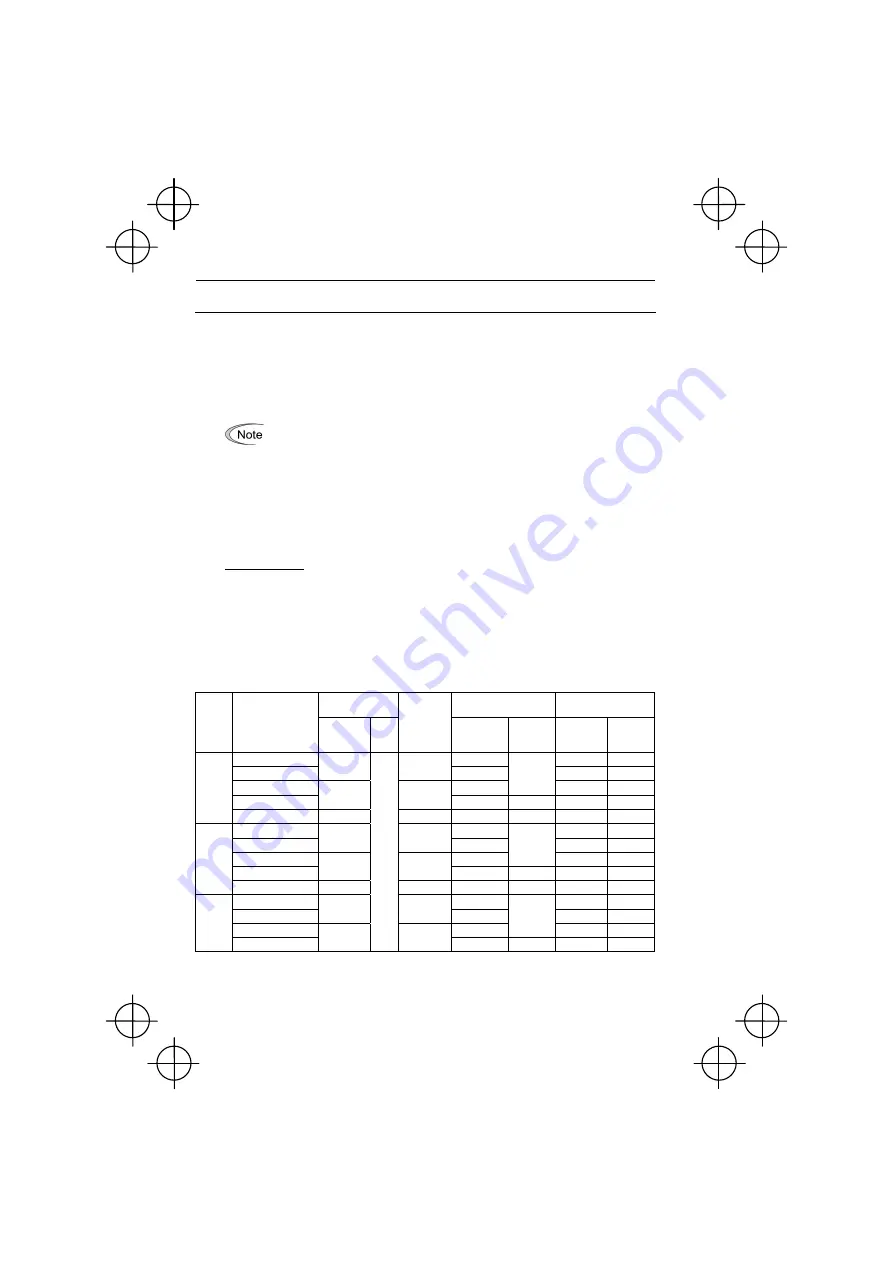
5-43
F50, F51
Electronic Thermal Overload Protection for Braking Resistor
(Discharging capability and Allowable average loss)
A braking resistor can be mounted on inverters of 0.4 kW or above.
These function codes specify the electronic thermal overload protection feature for the
braking resistor.
Set F50 and F51 data to the discharging capability and allowable average loss, respectively.
Since those values differ depending on the specifications of the braking resistor, refer to the
tables given below or calculate them according to the expressions given in the FRENIC-Mini
User's Manual (24A7-E-0023), Chapter 9 "FUNCTION CODES."
Depending on the thermal marginal characteristics of the braking resistor, the
electronic thermal overload protection feature may act so that the inverter issues
the overheat protection alarm
dbh
even if the actual temperature rise is not
enough. If it happens, review the relationship between the performance index of the
braking resistor and settings of related function codes.
The tables below list the discharging capability and allowable average loss of the braking
resistor. These values depend upon the inverter and braking resistor models.
External Braking Resistors
Standard models
The thermal sensor relay mounted on the braking resistor acts as a thermal protector of the
motor for overheat, so assign an "Enable external alarm trip" terminal command
THR
to any of
digital input terminals [X1] to [X3], [FWD] and [REV] and connect that terminal and its common
terminal to braking resistor's terminals 2 and 1.
To protect the motor from overheat without using the thermal sensor relay mounted on the
braking resistor, configure the electronic thermal overload protection facility by setting F50
and F51 data to the discharging capability and allowable average loss values listed below,
respectively.
Braking resistor
Continuous braking
(100% braking torque)
Intermittent braking
(Period: 100 s or less)
Power
supply
voltage
Inverter type
Type Qty.
Resistance
(
Ω
)
Discharging
capability
(kWs)
Braking
time
(s)
Allowable
average loss
(kW)
Duty
(%ED)
FRN0004C2S-2
9
0.044
22
FRN0006C2S-2
DB0.75-2 100
17 0.068
18
FRN0010C2S-2
34
45
0.075 10
FRN0012C2S-2
DB2.2-2 40
33 30
0.077
7
Three-
phase
200 V
FRN0020C2S-2
DB3.7-2
33
37
20
0.093
5
FRN0002C2S-4
9
0.044
22
FRN0004C2S-4
DB0.75-4 200
17 0.068
18
FRN0005C2S-4
34
45
0.075 10
FRN0007C2S-4
DB2.2-4 160
33 30
0.077
7
Three-
phase
400 V
FRN0011C2S-4
DB3.7-4
130
37
20
0.093
5
FRN0004C2S-7
9
0.044
22
FRN0006C2S-7
DB0.75-2 100
17 0.068
18
FRN0010C2S-7
34
45
0.075 10
Single-
phase
200 V
FRN0012C2S-7
DB2.2-2
1
40
33 30
0.077
7
Note: A box (
) in the above table replaces A, C, E, or U depending on the shipping destination. For three-phase 200 V
class series of inverters, it replaces A or U.