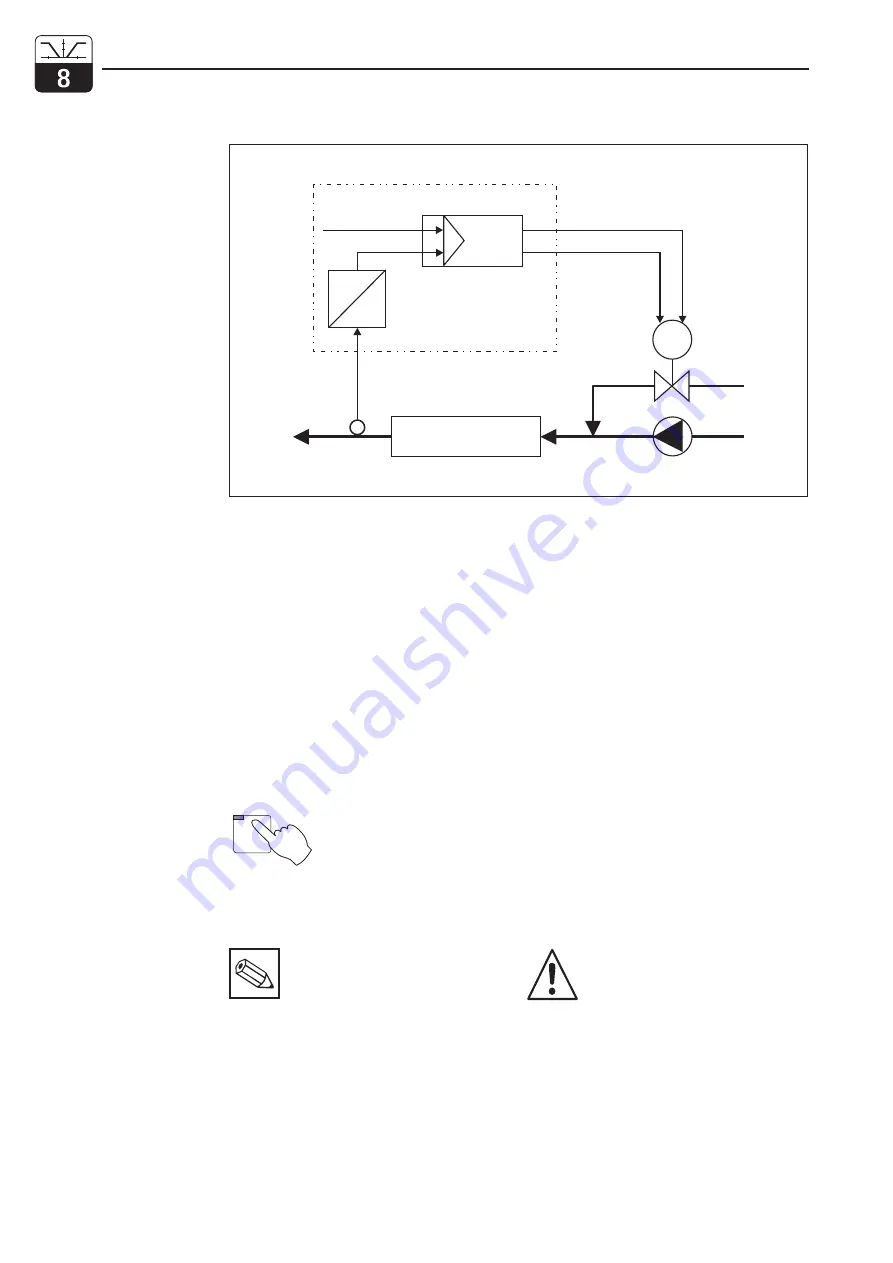
Three-point step controller
Three-point step controllers are used in
connection with integrally acting actuating
drives like motor valves and adjustable-lift
diaphragm pumps. In combination with these
actuating drives, the PD and PDT1 controllers
act like PI and PIT1 units. Parameter setting is
carried out via the control gain K
P
and the
integral action time T
n
(as is the case with PI
controllers). Since three-point step control is
carried out without position feedback, the
motor running time T
m
is required as well, in
which the drive goes through the whole of the
actuating range.
The adjustable neutral zone makes it possible
to suppress unnecessary setting movements
in the range of the specified value (Y = 0).
2 control contacts are needed to activate the
actuating drives (open / close).
The control contact 1 is activated for positive
output values while automatic operation and
by pressing the
↑
key while manual operation.
The control contact 2 is activated for negative
output values while automatic operation and
by pressing the
↓
key while manual operation.
8.2
Instruments with two contacts
8.2.1
Limit contactor (standard equipment)
Note:
The option »limit value + controller«
has to be chosen before in the menu
»commissioning / system set-up /
output relays« (see chapter 7.1.3).
Either a limit contact
or
a controller
can be set.
If a controller is supposed to be set
and a limit contactor has been set
beforehand, the limit contactor has
to be switched off (and vice-versa).
Warning:
The type of contact is maintained
after an output is switched off and
the control contact moves to its
home position (e.g. type of contact
»N.O.«: control contact open)
M
W
X
pH/mV
DPS
control contact 1 »open«
CPM 152
Mixing pipe
control contact 2 »close«
3-point step
controller
Fig. 8.6
Process control with a
three-point step controller
→
Commissioning
→
Controllers
→
Limit contactor
☞
8.2.1
→
Control contact
☞
8.2.2
PARAM
Controller configuration
mycom CPM 152
50
Hauser