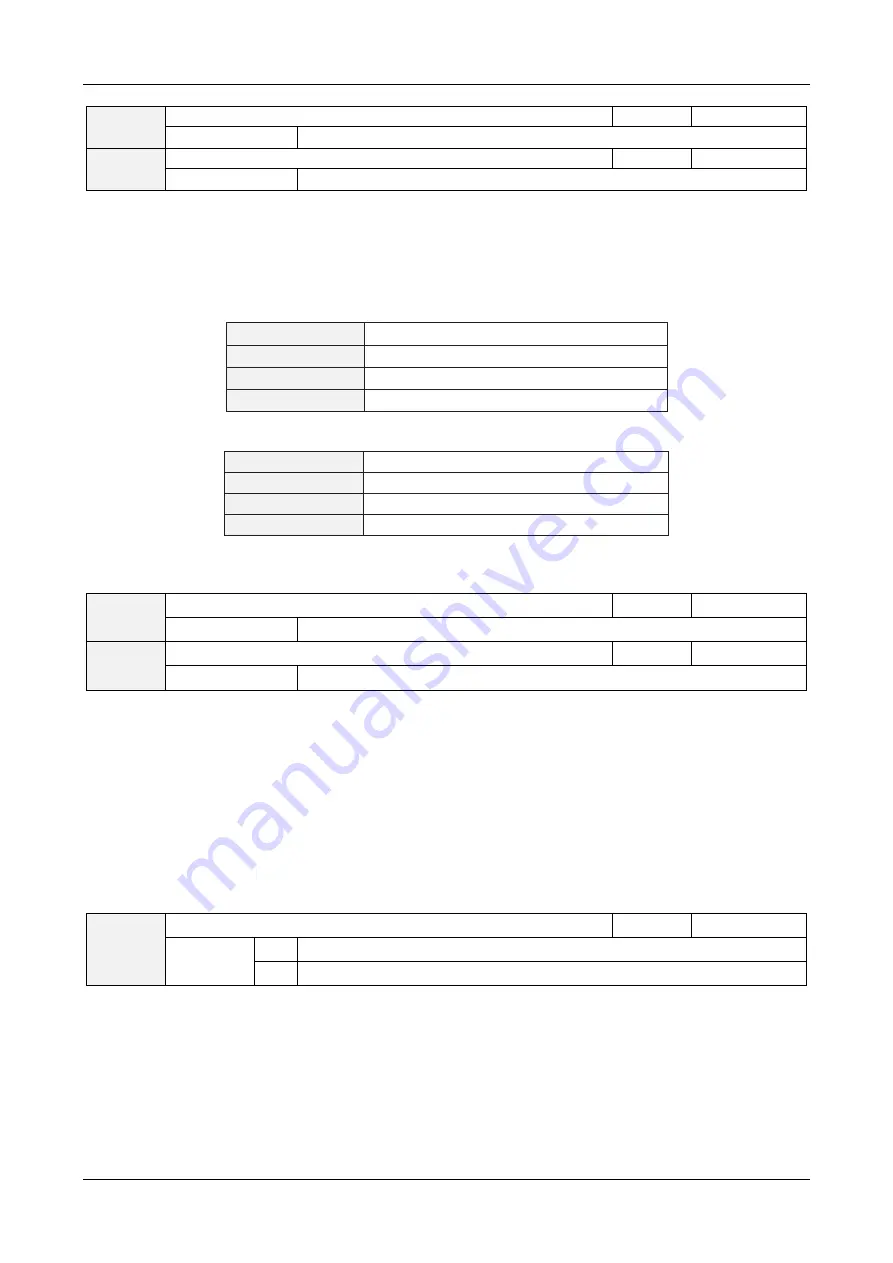
EM15 User’s Manual
5. Description of Function Codes
41
b1-03
Startup frequency
Default
0.00 Hz
Setting Range
0.00~10.00 Hz
b1-04
Startup frequency holding time
Default
0.0s
Setting Range
0.0s~100.0s
To ensure the motor torque at frequency inverter startup, set a proper startup frequency. In addition, to build
excitation when the motor starts up, the startup frequency must be held for a certain period.
The startup frequency (b1-03) is not restricted by the frequency lower limit. If the setting target frequency is lower
than the startup frequency, the frequency inverter will not start and stays in the holding state.
During switchover between forward rotation and reverse rotation, the startup frequency holding time is disabled. The
holding time is not included in the acceleration time but in the running time of simple PLC.
Example 1:
b0-03 = 0
The frequency source is digital setting.
b0-12 = 2.00 Hz
The digital setting frequency is 2.00 Hz.
b1-03 = 5.00 Hz
The startup frequency is 5.00 Hz.
b1-04 = 2.0s
The startup frequency holding time is 2.0s.
In this example, the frequency inverter stays in the holding state and the output frequency is 0.00 Hz.
Example 2:
b0-03 = 0
The frequency source is digital setting.
b0-12 = 10.00 Hz
The digital setting frequency is 10.00 Hz.
b1-03 = 5.00 Hz
The startup frequency is 5.00 Hz.
b1-04 = 2.0s
The startup frequency holding time is 2.0s.
In this example, the frequency inverter accelerates to 5.00 Hz at 2s, and then accelerates to the set frequency 10.00
Hz.
b1-05
Startup DC braking current/ Pre-excited current
Default
0%
Setting Range
0%~100%
b1-06
Startup DC braking time/ Pre-excited time
Default
0.0s
Setting Range
0.0s~100.0s
Startup DC braking is generally used during restart of the frequency inverter after the rotating motor stops.
Pre-excitation is used to make the frequency inverter build magnetic field for the asynchronous motor before startup
to improve the responsiveness.
Startup DC braking is valid only for direct start (b1-00 = 0). In this case, the frequency inverter performs DC braking
at the setting startup DC braking current. After the startup DC braking time, the frequency inverter starts to run. If the
startup DC braking time is 0, the frequency inverter starts directly without DC braking. The larger the startup DC
braking current is, the larger the braking force is.
If the startup mode is pre-excited start (b1-00 = 3), the frequency inverter firstly builds magnetic field based on the
set pre-excited current. After the pre-excited time, the frequency inverter starts to run. If the pre-excited time is 0, the
frequency inverter starts directly without pre-excitation.
The startup DC braking current or pre-excited current is a percentage of motor rated current.
b1-07
Stop mode
Default
0
Setting
Range
0
Decelerate to stop
1
Free stop
0: Decelerate to stop
After the stop command is enabled, the frequency inverter decreases the output frequency according to the
deceleration time and stops when the frequency decreases to zero.
1: Free stop
After the stop command is enabled, the frequency inverter immediately stops the output. The motor will free stop
based on the mechanical inertia.