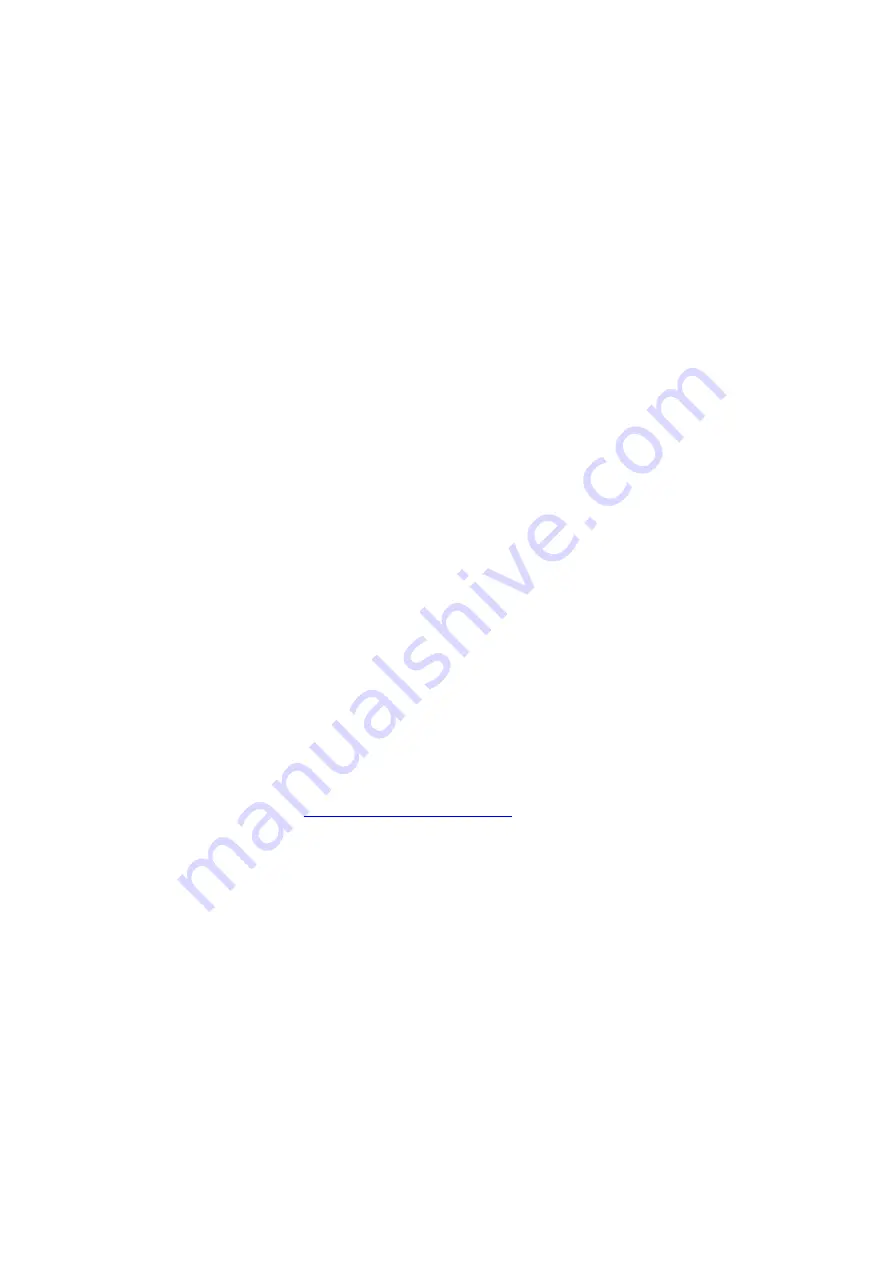
1 Rapid Link system 5
1.9 Storage
30
Rapid Link 5 · RAMO5 · RASP5
10/19 MN034004EN
www.eaton.com
1.9 Storage
Whenever RAMO5 or RASP5 devices are to be stored before use, it must be
ensured that there are adequate ambient conditions at the site of storage:
•
Storage temperature: -40 - +70 °C
•
relative average air humidity: < 95 %, non-condensing (EN 50178)
•
Store the devices only in closed original packaging.
•
Degree of protection IP65 is obtained only with plug connectors.
Only for RASP5:
•
In order to prevent damage to the DC link capacitors in RASP devices,
storage periods longer than 12 months should be avoided (see above:
Section "Internal DC link capacitors in RASP5").
1.10 Service and warranty
If you have any problem with a RAMO5 or RASP5 device, please contact your
local distributor.
When you call, have the following data ready:
•
the exact part no.
•
the date of purchase,
•
a detailed description of the problem which has occurred with RAMO5
or RASP5.
If some of the information printed on the rating plate is not legible, please
state only the data which are clearly legible.
Information concerning the warranty can be found in the Eaton Industries
GmbH Terms and Conditions.
24-hour hotline: +49 (0) 1805 223 822
Email:
Содержание Rapid Link RAMO5
Страница 1: ...Manual Rapid Link 5 RAMO5 RASP5 10 19 MN034004EN ...
Страница 4: ...II ...
Страница 10: ...6 Rapid Link 5 RAMO5 RASP5 10 19 MN034004EN www eaton com ...
Страница 122: ...4 Operation 4 3 Manual control 118 Rapid Link 5 RAMO5 RASP5 10 19 MN034004EN www eaton com ...
Страница 136: ...5 RAMO5 Motor starter 5 7 Configure special settings 132 Rapid Link 5 RAMO5 RASP5 10 19 MN034004EN www eaton com ...
Страница 158: ...8 PC tool 8 2 Parameter Editor 154 Rapid Link 5 RAMO5 RASP5 10 19 MN034004EN www eaton com ...
Страница 164: ...9 Control Unit 9 2 Extended parameter set 160 Rapid Link 5 RAMO5 RASP5 10 19 MN034004EN www eaton com ...
Страница 194: ...10 Parameter list 10 4 Parameter groups for RASP 190 Rapid Link 5 RAMO5 RASP5 10 19 MN034004EN www eaton com ...
Страница 208: ...11 Communications 11 5 OP Bus 204 Rapid Link 5 RAMO5 RASP5 10 19 MN034004EN www eaton com ...
Страница 216: ...12 Error messages 12 3 RASP Error list 212 Rapid Link 5 RAMO5 RASP5 10 19 MN034004EN www eaton com ...