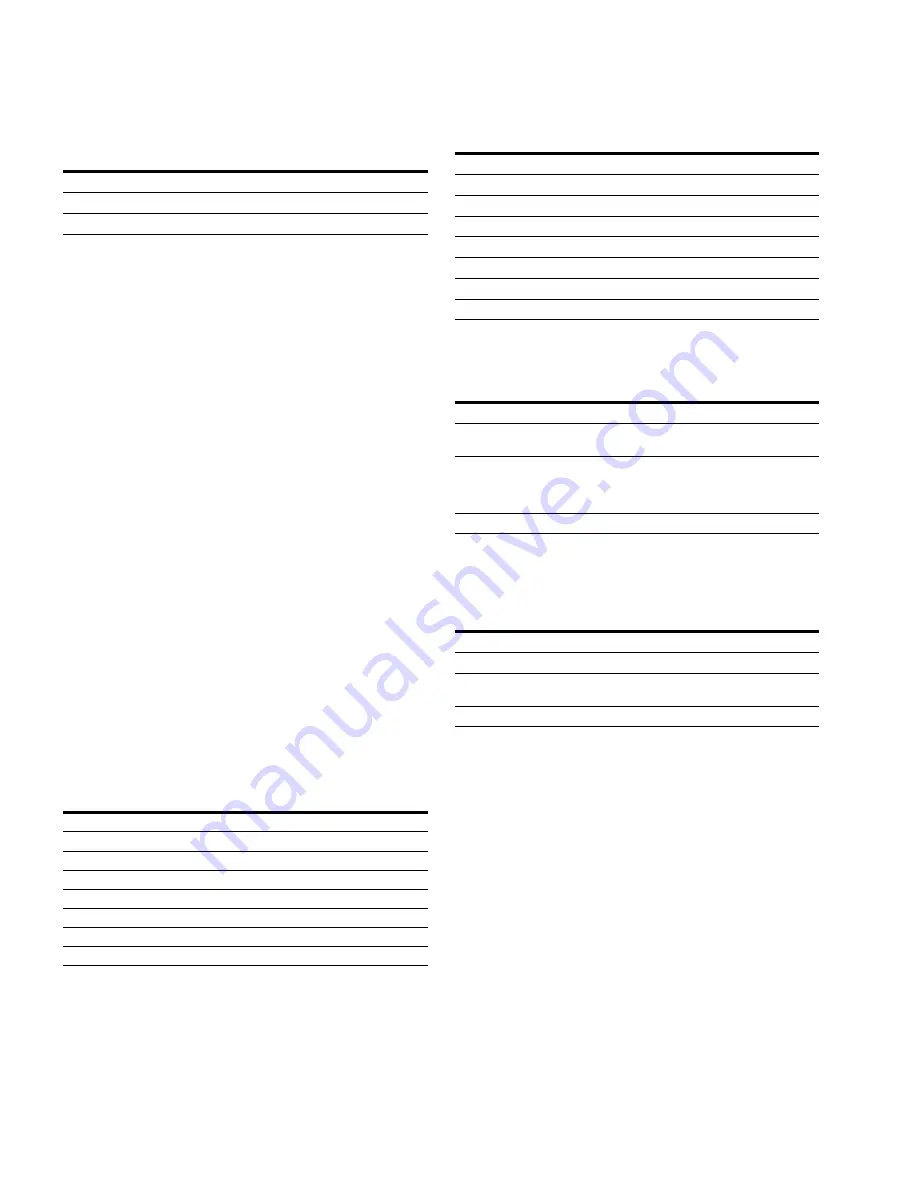
62
9. Ethernet/IP
Dual port ethernet option board installation manual
MN032004EN October 2017 www.eaton.com
Table 131. Fault history object – number of instances
Drive
Maximum number of faults
Eaton MMX
10
Eaton SPX
10
Eaton SPX
10
9.2.3.4.3. Instance attributes
Instance attribute “FaultCode”
The value returns the fault code of a fault entry which is
represented by the Fault History Object instance.
Instance attribute “FaultID”
The value returns the fault ID of a fault entry which is
represented by the Fault History Object instance. This value
more exactly specifies which kind of fault is in question.
In case of SVX/SPX, the FaultID is the subcode of the fault.
Instance attribute “FaultMillisAfterMidnight”
The attribute contains the number of milliseconds after
midnight when the fault is time-stamped. The purpose
of this format is to provide high accuracy and give you
the possibility of representation according to 24-hour or
12-hour clock.
9.2.3.4.4. Class services
Class service “reset”
This service is used to reset the fault history of the drive.
9.3 Assembly instances implemented by OPTE9
9.3.1 ODVA I/O Assembly instances for AC/DC Drive
The OPTE9 supports the Output Assembly Instances 20,
21, 23 and 25, and the Input Assembly Instances 70, 71, 73
and 75.
The control word bits are mapped to the object data
according to the table below.
Table 132. CIP Control word mapping to object data
Bit
Bit name
Object
Attribute name Attribute ID
0
RunFwd
Control supervisor object
Run1
3
d
1
RunRev
Control supervisor object
Run2
4
d
2
FaultRst
Control supervisor object
FaultRst
12
d
3
–
–
–
–
4
–
–
–
–
5
NetCtrl
Control supervisor object
NetCtrl
5
d
6
NetRef
AC/DC drive object
NetRef
4
d
7
NetProc
AC/DC drive object
NetProc
5
d
The status word bits are mapped to the object data
according the table below.
Table 133. CIP Status word mapping to object data
Bit
Bit name
Object
Attribute name Attribute ID
0
Faulted
Control supervisor object
Faulted
10
d
1
Warning
Control supervisor object
Warning
11
d
2
Running1
Control supervisor object
Running1
7
d
3
Running2
Control supervisor object
Running2
8
d
4
Ready
Control supervisor object
Ready
9
d
5
CtrlFromNet Control supervisor object
CtrlFromNet
15
d
6
RefFromNet AC/DC drive object
RefFromNet
29
d
7
AtReference AC/DC drive object
AtReference
3
d
The process data IN is mapped according to the table below.
Table 134. Process data in mapping to object data
Parameter name
Object
Attribute name
Attribute ID
Speed Reference
AC/DC drive object
SpeedRef
8d
Torque Reference
AC/DC drive object
TorqueRef
(ProcessDataIn1)
12d
Process Reference AC/DC drive object
ProcessRef
If Drive Mode is:
0 = ProcessDataIn1
4 = ProcessDataIn2
14d
Drive Mode
AC/DC drive object
DriveMode
6d
The process data OUT is mapped according to the
table below.
Table 135. Process data out mapping to object data
Parameter name Object
Attribute name
Attribute ID
Speed Actual
AC/DC drive object
SpeedActual
7d
Torque Actual
AC/DC drive object
TorqueActual
11d
Process Actual
AC/DC drive object
ProcessActual
(ProcessDataOut1)
13d
Drive State
Control supervisor object State
6d
The Speed Reference is updated to the drive only when
the NetRef bit is set to 1. The torque reference is updated
to the drive only when the motor control mode is
“Torque Control”.
Содержание OPTE9
Страница 1: ...FPO OPTE9 Dual port ethernet option board installation manual...
Страница 88: ...This Page Intentionally Left Blank...
Страница 89: ...This Page Intentionally Left Blank...