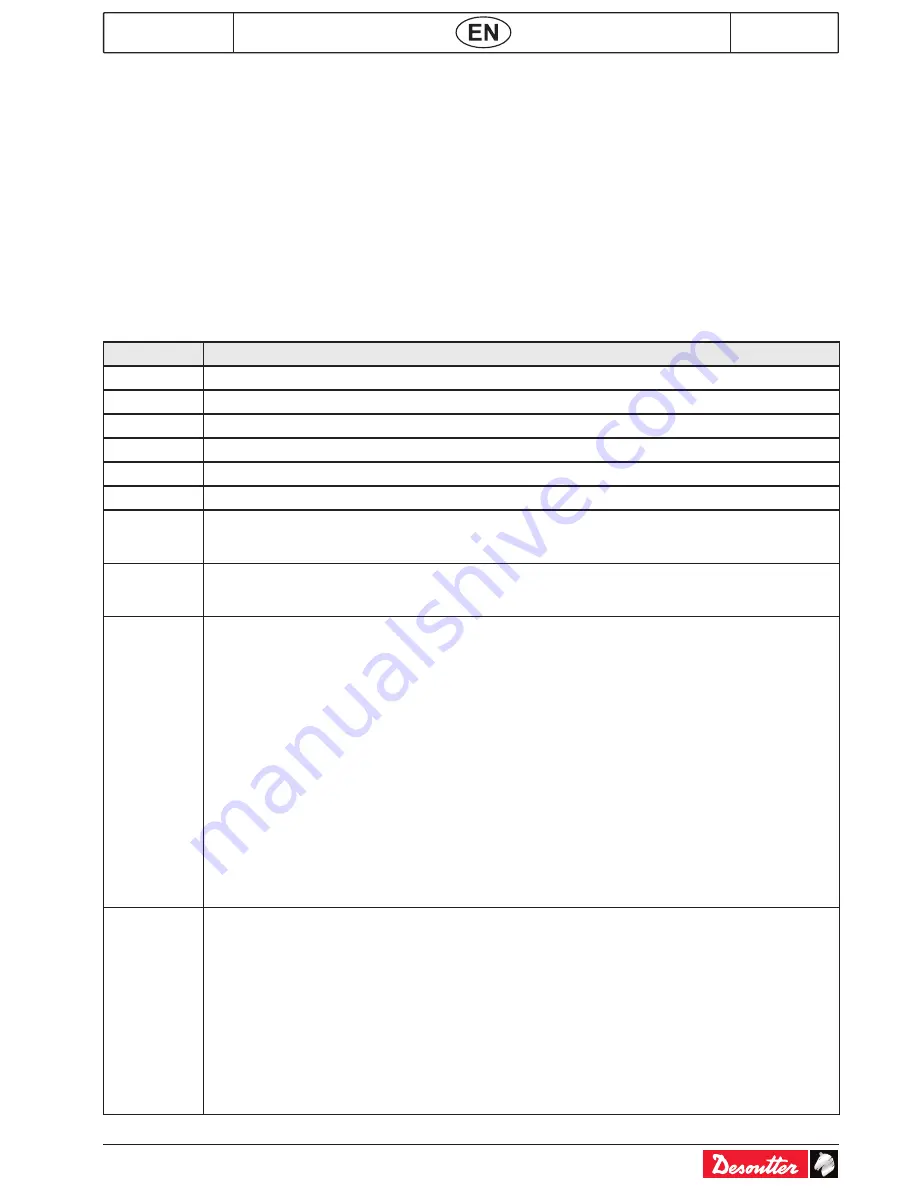
01/2018
67 / 80
6159933780
Issue no: 09
CVIL II
13 - TROUBLE SHOOTING HELP
13.1 - Warning
Choose one of these 2 methods to look for information in
this document:
● Locate the error message(s) displayed on the
screen of the controller among the messages listed
in the document. A detailed explanation helps you
understand the message(s). Cross-references
leading to the error causes are suggested whenever
this is possible.
● Select the relevant symptom among those listed.
Each possible cause is numbered to make the search
easier when cross-references are used.
13.2 - Report codes
Text
Comments
Accept
Accept report
Reject
Reject report
Tmin
The final torque at the end of the cycle is lower than minimum torque tolerance.
Tmax
The final torque at the end of the cycle is higher than the maximum torque tolerance.
Amin
The final angle at the end of the cycle is lower than the minimum angle tolerance.
Amax
The final angle at the end of the cycle is higher than maximum angle tolerance.
Scy
Cycle was aborted because the trigger switch was released prematurely.
If it happens only just before reaching the target torque, torque and angle results may be within the
programmed tolerances.
Time
Cycle was stopped after the time allocated for this phase or this cycle is elapsed and not by the
target parameter.
The programmed time out has to be modified to fit the application.
Err
EITHER the tool or the programmed cycles are not consistent with the station mode.
You can try the following:
● Make sure the station mode is set correctly, according to the tool.
● Go back to the cycle parameters and save it again, so that the station mode used for the cycle is
the current running one.
OR the speed is not constant when the torque is reached.
Torque measurement is cancelled during speed transitions.
This message mainly appears in case of hard joints. You can try the following adjustments:
● Reduce the final speed to increase the phase time (remain > 3%).
● Reduce final speed phase acceleration time to minimum (0.01 s) to reach the tightening speed as
quickly as possible.
● Reduce the run down speed phase to avoid high over torque when clamping and to limit the
speed gap between the run down and final speed phase.
If the Err message remains, it means that the joint is too hard to change the speed after clamping.
Try to program a new strategy: Angle run down + Final speed phase.
As the run down phase must end before clamping, the speed transition between the 2 phases no
longer needs to be rapid (0.3 s is sufficient).
NOT READY
List of errors preventing the controller from being ready:
● Over-current: Maximum servo drive current is reached.
● Differential: Earth ground connection opened (the controller does not check earth linkage). This
error is often due to a cable problem.
● Thermal contact: Maximum motor temperature is reached (100°C). This error remains activated
until the motor temperature falls below 80°C.
● SPI link error: The cycle was aborted due to a digital communication problem (SPI) between the
controller and the tool.
● FLEX version error
● Maximum current (Imax)
● Resolver: Position change or non zero speed detected when the motor start is not activated.
● Temperature: Power components over temperature.
Содержание CVIL II
Страница 2: ......
Страница 12: ...01 2018 12 80 6159933780 Issue no 09 CVIL II 4 2 2 Language selection 4 2 3 Setting the date and time...
Страница 77: ...01 2018 77 80 6159933780 Issue no 09 CVIL II...
Страница 78: ...01 2018 78 80 6159933780 Issue no 09 CVIL II...
Страница 79: ...01 2018 79 80 6159933780 Issue no 09 CVIL II...
Страница 80: ...www desouttertools com More Than Productivity Copyright 2016...