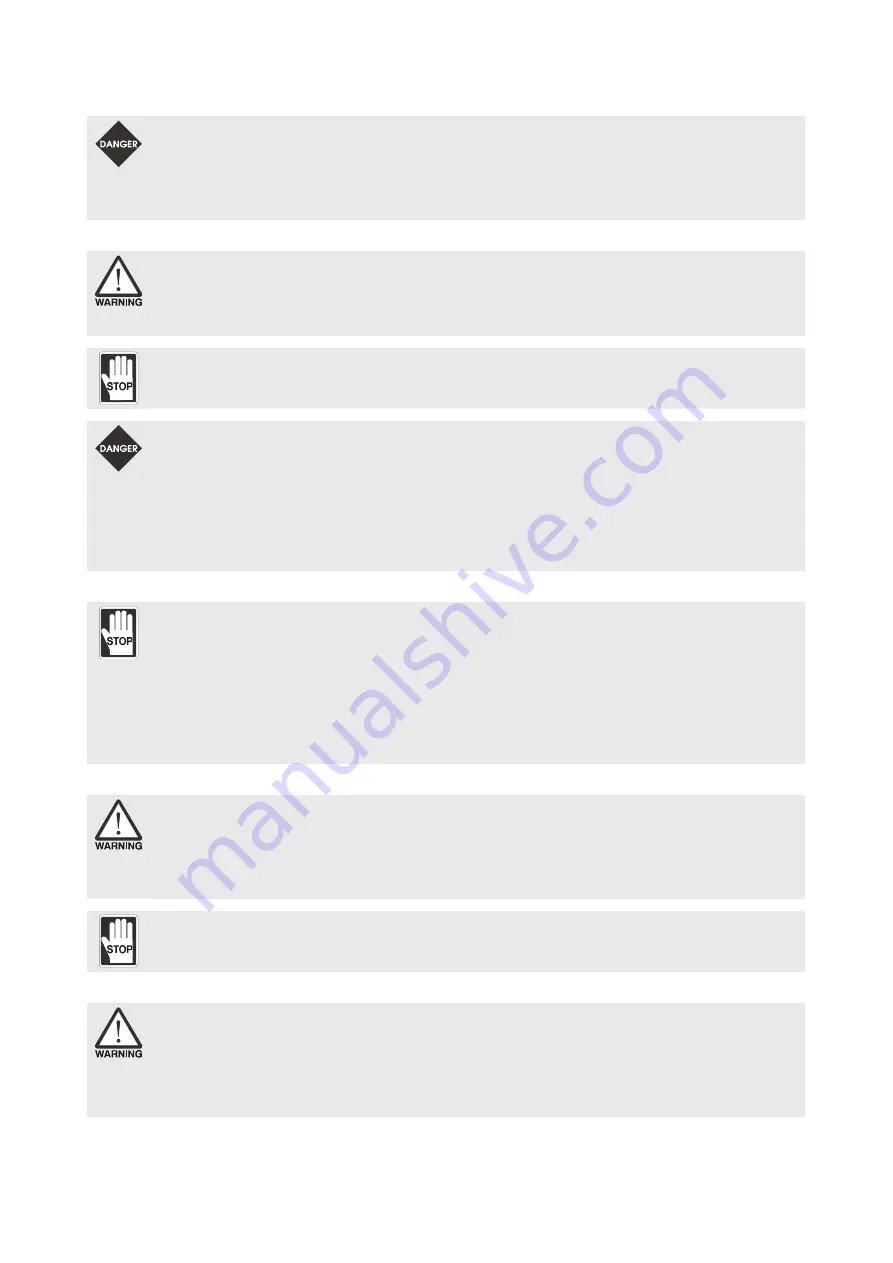
Preface
|
ASDA-AB Series
Revision January 2009
iii
Wiring
¾
Connect the ground terminals to a class-3 ground (Ground resistance should not exceed 100
Ω
). Improper grounding may result
in electric shock or fire.
¾
Do not connect any power supplies to the U, V, W terminals. Failure to observe this precaution may result in serious injury,
damage to the drive or fire.
¾
Ensure that all screws, connectors and wire terminations are secure on the power supply, servo drive and motor. Failure to
observe this caution may result in damage, fire or personal injury.
Operation
¾
Before starting the operation with a mechanical system connected, change the drive parameters to match the user-defined
parameters of the mechanical system. Starting the operation without matching the correct parameters may result in servo drive
or motor damage, or damage to the mechanical system.
¾
Ensure that the emergency stop equipment or device is connected and working correctly before operating the motor that is
connected to a mechanical system.
¾
Do not approach or touch any rotating parts (e.g. shaft) while the motor is running. Failure to observe this precaution may
cause serious personal injury.
¾
In order to prevent accidents, the initial trial run for servo motor should be conducted under no load conditions (separate the
motor from its couplings and belts).
¾
For the initial trial run, do not operate the servo motor while it is connected to its mechanical system. Connecting the motor to
its mechanical system may cause damage or result in personal injury during the trail run. Connect the servo motor once it has
successfully completed a trail run.
¾
Caution: Please perform trial run without load first and then perform trial run with load connected. After the servo motor is
running normally and regularly without load, then run servo motor with load connected. Ensure to perform trial run in this order
to prevent unnecessary danger.
¾
Do not touch either the drive heat sink or the motor during operation as they may become hot and personal injury may result.
Maintenance and Inspection
¾
Do not touch any internal or exposed parts of servo drive and servo motor as electrical shock may result.
¾
Do not remove the operation panel while the drive is connected to an electrical power source otherwise electrical shock may
result.
¾
Wait at least 10 minutes after power has been removed before touching any drive or motor terminals or performing any wiring
and/or inspection as an electrical charge may still remain in the servo drive and servo motor with hazardous voltages even after
power has been removed.
¾
Do not disassemble the servo drive or motor as electric shock may result.
¾
Do not connect or disconnect wires or connectors while power is applied to the drive and motor.
¾
Only qualified personnel who have electrical knowledge should conduct maintenance and inspection.
Main Circuit Wiring
¾
Install the encoder cables in a separate conduit from the motor power cables to avoid signal noise. Separate the conduits by
30cm (11.8inches) or more.
¾
Use multi-stranded twisted-pair wires or multi-core shielded-pair wires for signal, encoder (PG) feedback cables. The maximum
length of command input cable is 3m (9.84ft.) and the maximum length of encoder (PG) feedback cables is 20m (65.62ft.).
¾
As a charge may still remain in the drive with hazardous voltages even after power has been removed, be sure to wait at least 10
minutes after power has been removed before performing any wiring and/or inspection.
¾
It is not recommended to frequently power the drive on and off. Do not turn the drive off and on more than once per minute as
high charging currents within the internal capacitors may cause damage.
Main Circuit Terminal Wiring
¾
Please perform the wiring after the terminal blocks are all removed from the drive.
¾
Insert only one wire into one terminal on the terminal block.
¾
When inserting wires, please ensure that the conductors are not shorted to adjacent terminals or wires.
¾
Ensure to double check the wiring before applying power to the drive.
¾
If the wiring is in error, perform the wiring again with proper tools. Never use force to remove the terminals or wires. Otherwise,
it may result in malfunction or damage.
Содержание AC Servo Drive ASDA-AB
Страница 1: ......
Страница 13: ...Table of Contents ASDA AB Series Revision January 2009 This page intentionally left blank...
Страница 20: ...Chapter 1 Unpacking Check and Model Explanation ASDA AB Series Revision January 2009 1 7 110V models...
Страница 27: ...Chapter 3 Connections and Wiring ASDA AB Series 3 2 Revision January 2009 Figure 3 2 110V Servo Drive...
Страница 67: ...Chapter 3 Connections and Wiring ASDA AB Series 3 42 Revision January 2009 This page intentionally left blank...
Страница 85: ...Chapter 5 Trial Run and Tuning Procedure ASDA AB Series 5 8 Revision January 2009...
Страница 103: ...Chapter 5 Trial Run and Tuning Procedure ASDA AB Series 5 26 Revision January 2009 This page intentionally left blank...
Страница 149: ...Chapter 6 Control Modes of Operation ASDA AB Series 6 46 Revision January 2009 This page intentionally left blank...
Страница 246: ...Chapter 8 MODBUS Communications ASDA AB Series Revision January 2009 8 3 Cable Connection...
Страница 265: ...Chapter 9 Maintenance and Inspection ASDA AB Series 9 4 Revision January 2009 This page intentionally left blank...
Страница 275: ...Chapter 10 Troubleshooting ASDA AB Series 10 10 Revision January 2009 This page intentionally left blank...
Страница 282: ...Chapter 11 Specifications ASDA AB Series Revision January 2009 11 7 11 3 Servo Motor Speed Torque Curves...
Страница 307: ...Chapter 12 Application Examples ASDA AB Series 12 10 Revision January 2009...
Страница 333: ...Chapter 12 Application Examples ASDA AB Series 12 36 Revision January 2009 8 B A 2 5 Position SPEED Z pulse...
Страница 335: ...Chapter 12 Application Examples ASDA AB Series 12 38 Revision January 2009 Connecting to Delta DVP 01PU...
Страница 336: ...Chapter 12 Application Examples ASDA AB Series Revision January 2009 12 39 Connecting to Mitsubishi FX1PG...
Страница 337: ...Chapter 12 Application Examples ASDA AB Series 12 40 Revision January 2009 Connecting to Mitsubishi FX2N1PG...
Страница 338: ...Chapter 12 Application Examples ASDA AB Series Revision January 2009 12 41 Connecting to Mitsubishi AD75...
Страница 339: ...Chapter 12 Application Examples ASDA AB Series 12 42 Revision January 2009 This page intentionally left blank...
Страница 353: ...Appendix A Accessories ASDA AB Series A 14 Revision January 2009 This page intentionally left blank...
Страница 356: ...Appendix A Accessories ASDA AB Series Revision January 2009 B 3 Figure 1 Saddle on both ends Saddle on one end Figure 2...