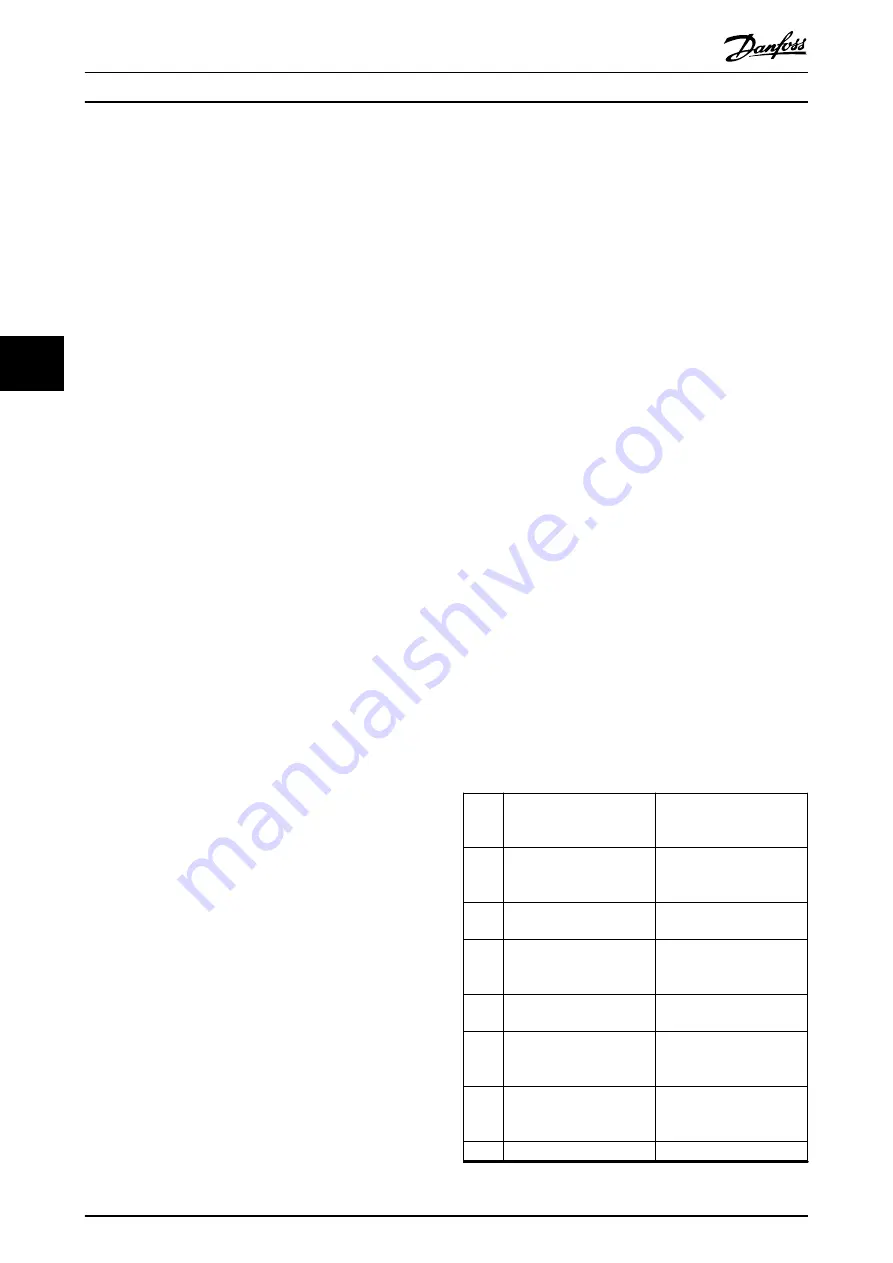
Check that
parameter 1-93 Thermistor Source
selects terminal 53 or 54.
•
When using terminal 18, 19, 31, 32, or 33 (digital
inputs), check that the thermistor is connected
correctly between the digital input terminal used
(digital input PNP only) and terminal 50. Select
the terminal to use in
parameter 1-93 Thermistor
Source
.
WARNING/ALARM 13, Over current
The peak current limit of the frequency converter (approxi-
mately 145–177% of the frequency converter rated current)
is exceeded. The warning lasts approximately 1.5 s, then
the frequency converter trips and issues an alarm. Shock
loading or quick acceleration with high-inertia loads can
cause this fault. If the acceleration during ramp-up is quick,
the fault can also appear after kinetic back-up.
If extended mechanical brake control is selected, a trip can
be reset externally.
Troubleshooting
•
Remove the power and check if the motor shaft
can be turned.
•
Check that the motor size matches the frequency
converter.
•
Check that the motor data is correct in
parameters
1-20
to
1-25
.
ALARM 14, Earth fault
There is current from the output phases to ground, either
in the cable between the frequency converter and the
motor or in the motor itself.
Troubleshooting
•
Remove power to the frequency converter and
repair the ground fault.
•
Check for ground faults in the motor by
measuring the resistance to ground of the motor
cables and the motor with a megohmmeter.
ALARM 16, Short circuit
There is short-circuiting in the motor or motor wiring.
Troubleshooting
•
Remove the power to the frequency converter
and repair the short circuit.
WARNING/ALARM 17, Control word timeout
There is no communication to the frequency converter.
The warning is only active when
parameter 8-04 Control
Word Timeout Function
is NOT set to
[0] Off
.
If
parameter 8-04 Control Word Timeout Function
is set to
[5]
Stop and Trip
, a warning appears, and the frequency
converter ramps down to a stop and shows an alarm.
Troubleshooting
•
Check the connections on the serial communi-
cation cable.
•
Increase
parameter 8-03 Control Word Timeout
Time
.
•
Check the operation of the communication
equipment.
•
Verify that proper EMC installation was
performed.
ALARM 30, Motor phase U missing
Motor phase U between the frequency converter and the
motor is missing.
Troubleshooting
•
Remove the power from the frequency converter
and check motor phase U.
ALARM 31, Motor phase V missing
Motor phase V between the frequency converter and the
motor is missing.
Troubleshooting
•
Remove the power from the frequency converter
and check motor phase V.
ALARM 32, Motor phase W missing
Motor phase W between the frequency converter and the
motor is missing.
Troubleshooting
•
Remove the power from the frequency converter
and check motor phase W.
ALARM 38, Internal fault
When an internal fault occurs, a code number defined in
is shown.
Troubleshooting
•
Cycle power.
•
Check that the option is properly installed.
•
Check for loose or missing wiring.
Note the code number before contacting the supplier or
Danfoss Service Department.
Code
num-
ber
Text
Troubleshooting
0
Serial port cannot be
initialized.
Contact the supplier or
Danfoss Service
Department.
256–
258
Power EEPROM data is
defective or too old.
Replace power card.
512–
519
Internal fault.
Contact the supplier or
Danfoss Service
Department.
783
Parameter value outside of
min/max limits
–
1024–
1284
Internal fault.
Contact the supplier or
Danfoss Service
Department.
1379–
2819
Internal fault.
Contact the supplier or
Danfoss Service
Department.
2561 Replace control card
–
Diagnostics and Troubleshoo...
VLT
®
DriveMotor FCP 106/FCM 106
124
Danfoss A/S © 11/2015 All rights reserved.
MG03N202
5
5