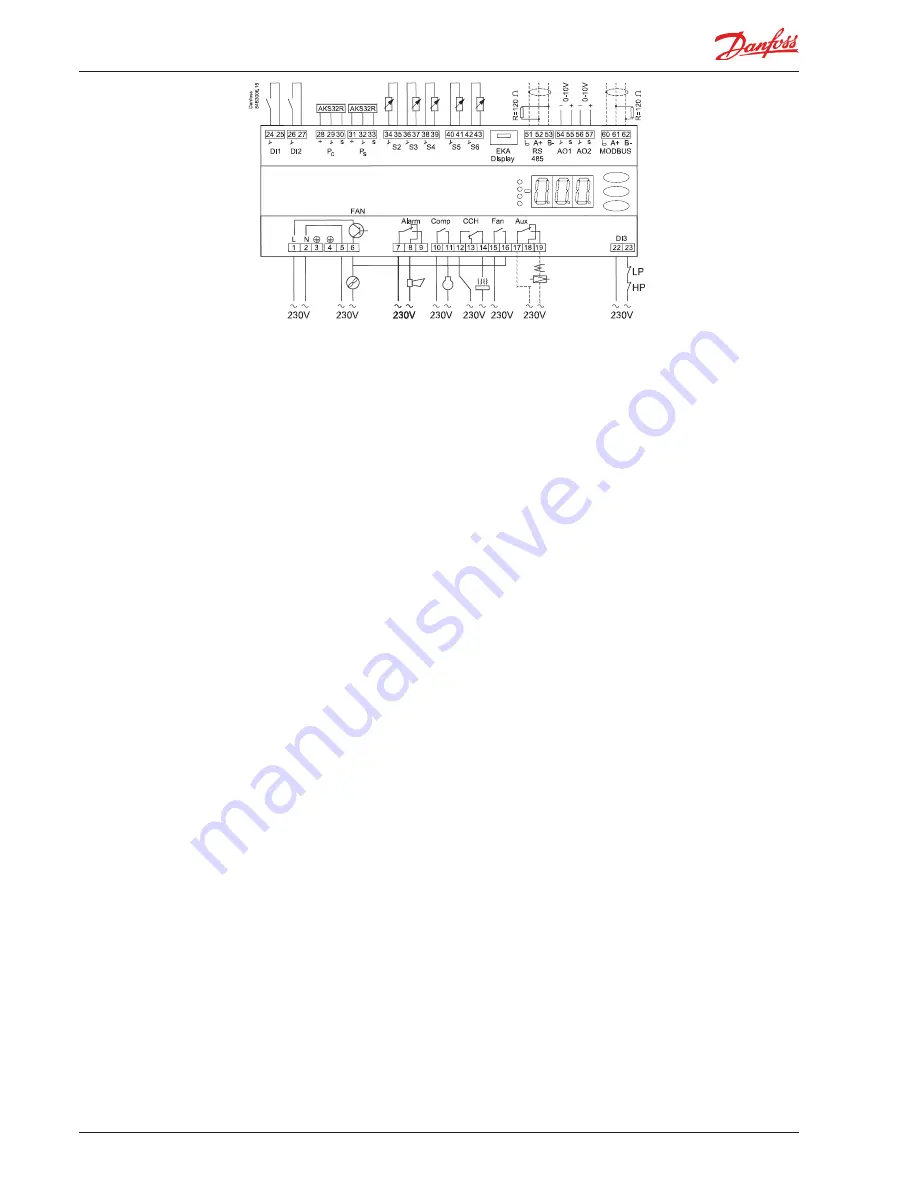
16
User
Guide RS8GD602 © Danfoss 2015-10
Optyma
Plus
TM
DI1
Digital input signal.
Used to start/stop cooling (room thermostat)
Starts when the input is short-circuited.
DI2
Digital input signal.
The defined function is active when the input is short-circuited/
opened. The function is defined in o37.
Pc
Pressure transmitter, ratiometric AKS 32R, 0 to 32 bar
Connect to terminal 28, 29 and 30.
Ps
Pressure transmitter, ratiometric e.g.
AKS 32R, -1 to 12 bar
Connected to terminal 31, 32 and 33.
S2
Air sensor, Tamb. Pt 1000 ohm sensor, eg. AKS 11
S3
Discharge gas sensor, Td. Pt 1000 ohm sensor, eg. AKS 21
S4
Suction gas temperature, Ts. Pt 1000 ohm sensor, eg. AKS 11
S5,
Extra temperature measurement, Taux. Pt 1000 ohm sensor, eg. AKS 11
S6,
Extra temperature measurement, S6. Pt 1000 ohm sensor, eg. AKS 11
EKA Display
If there is be external reading/operation of the controller, display type
EKA 163B or EKA 164B can be connected.
RS485 (terminal 51, 52,53)
For data communication, but only if a data communication module is
inserted in the controller. The module can be Lon.
If data communication is used, it is important that the installation of
the data communication cable is performed correctly.
See separate literature No. RC8AC…
AO1, terminal 54, 55
Output signal, 0-10 V. Must be used if the fan is equipped with internal
speed control and 0-10 V d.c. input, e.g. EC-motor.
AO2, terminal 56, 57
Output signal, 0-10 V. Must be used if the compressor is speed
controlled.
MODBUS (terminal 60, 61, 62)
Built in Modbus data communication.
If data communication is used, it is important that the installation of
the data communication cable is performed correctly.
See separate literature No. RC8AC…
(Alternatively the terminals can be connected to an external display
type EKA 163A or 164A, but then they cannot be used for data
communication. Any data communication must then be carried out
by one of the other methods.)
Supply voltage
230 V a.c. (This must be the same phase for all 230 V connections).
FAN
Fan connection. Speed controlled internally.
Alarm
There is a connection between terminal 7 and 8 in alarm situations
and when the controller is without power.
Comp
Compressor
.
There is a connection between terminal 10 and 11, when
the compressor is running.
CCH
Heating element in the crankcase
There is connection between terminals 12 and 14 when heating takes
place.
Fan
There is connection between terminals 15 and 16 when the fan's
speed is raised to over 95%. (Fan signal changes from terminal 5-6 to
15-16. Connect wire from terminal 16 to the fan.)
Aux
Liquid injection in suction line
There is connection between terminals 17 and 19, when the function
is active.
DI3
Digital input signal from low/high pressure monitoring.
The signal must have a voltage of 0 / 230 V AC.
Electric noise
Cables for sensors, DI inputs and data communication
must
be kept
separate from other electric cables:
- Use separate cable trays
- Keep a distance between cables of at least 10 cm.
- Long cables at the DI input should be avoided
Installation considerations
Accidental damage, poor installation, or site conditions, can give rise
to malfunctions of the control system, and ultimately lead to a plant
breakdown. Every possible safeguard is incorporated into our prod-
ucts to prevent this. However, a wrong installation, for example, could
still present problems. Electronic controls are no substitute for normal,
good engineering practice.
Danfoss will not be responsible for any goods, or plant components,
damaged as a result of the above defects. It is the installer's respon-
sibility to check the installation thoroughly, and to fit the necessary
safety devices. Special reference is made to the necessity of signals
to the controller when the compressor is stopped and to the need of
liquid receivers before the compressors.
Your local Danfoss agent will be pleased to assist with further advice,
etc.
Connections