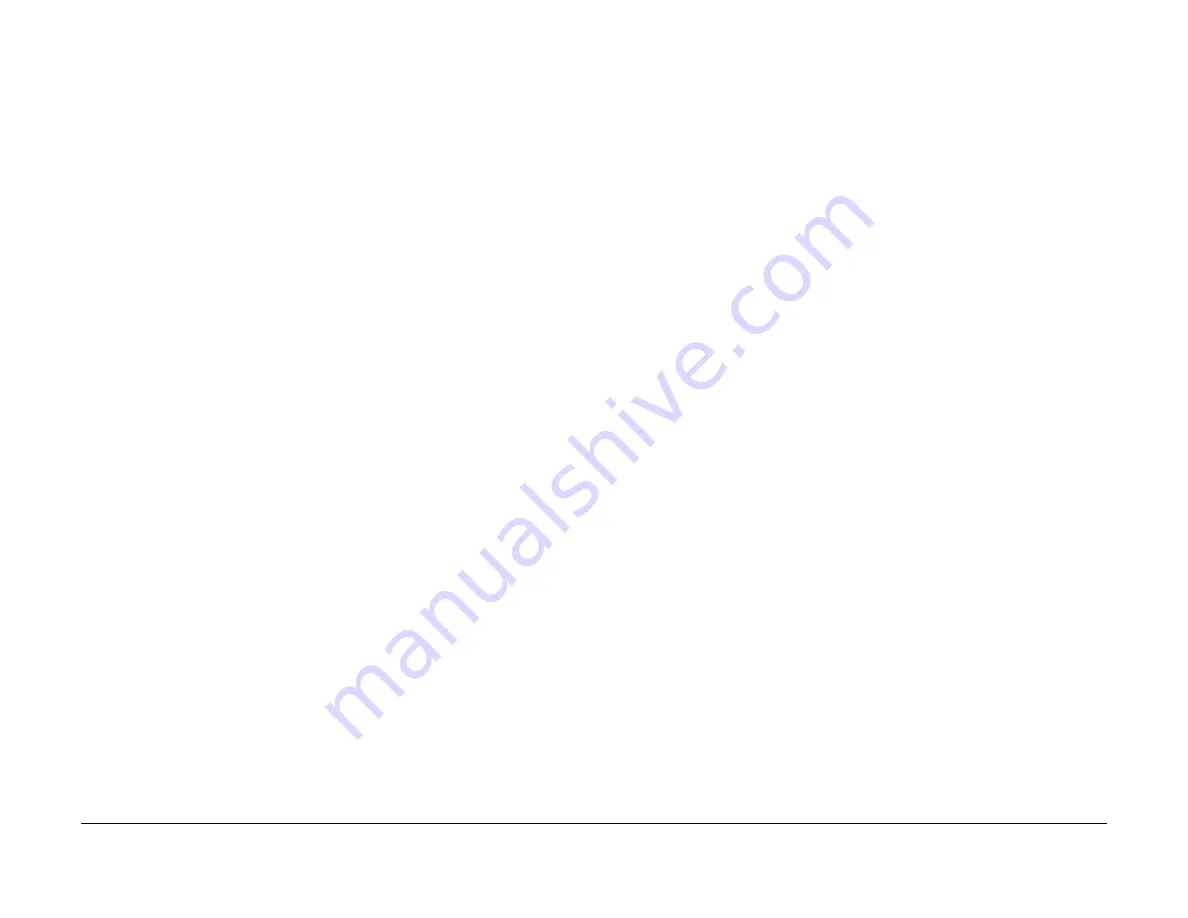
70
Cranesmart LMI Version R9
7. Press Accept twice to save.
8. Use the Up or Down arrows to select Top Menu to continue with Supervisor permission or, Select Exit to return to Primary Operating Screen
and Operator Permission level.
NOTE:
The weight displayed on the panel should indicate block or headache ball weight to the nearest 100 lbs. For example, if the headache ball is 160 lbs.
the display should indicate 200 lbs.
Known Weights
The minimum weight to be used for Load cell calibration depends on the Load Cell‟s single line pull rating. A known
weight of 50% or more of the single line pull capacity is best for re-calibrating the load cells.
Important Calibration/Weight Adjustment Information
In the system calibration modes a single push of the Up or Down arrows changes the increments by 100 pounds for
up to 16 parts-of-line.
If you require 17 or more parts-of-line, the increments for a single push of the Up or Down arrows, change by 100
pounds to start and change to 200 pounds.
Sheave friction can be a factor in Load system calibration. The Load cell measures force on one part-of-line (POL)
and multiplies it by the number of parts-of-line. If you are running 10 POL this may affect load calibration by 10%.
For best results always make sure sheave bearings are clean and well lubricated.
When the Calibration is complete, repeat the steps with each load cell on each winch, i.e. Main, Auxiliary One, etc.
Formula for known weights
(Maximum single line pull of winch X parts-of-line) ÷ 2 = minimum known weight required
Examples of Known Weights
Using a 15,000lbs. SLP load cell and running 4 parts-of-line, the ideal known calibration weight would be 30,000lbs.
Using a 25,000lbs. SLP load cell and running 6 parts-of-line, the ideal known calibration weight would be 75,000lbs.
Using a 40,000lbs. SLP load cell and running 8 parts-of-line, the ideal known calibration weight would be 160,000lbs.
NOTE:
You may utilise the factory restore function to self calibrate.
You can re-calibrate the system yourself by using a known weight and following the steps above.
Calibrating the Load Cells is a two-step process; first, ensure you have selected the correct Winch and Parts-of-line for the Load Cell, and then
calibrate Load Zero and Span for that Load Cell. Repeat these steps for each Load Cell on the crane.
Содержание LMI System
Страница 1: ...Cranesmart Systems LMI System User Manual May 11 2015 Rev 9...
Страница 23: ...22 Cranesmart LMI Version R9...
Страница 43: ...42 Cranesmart LMI Version R9 Basic Wiring Diagram...
Страница 45: ...44 Cranesmart LMI Version R9 Junction Box Wiring Diagram...
Страница 47: ...46 Cranesmart LMI Version R9 Alarm Hub Wiring Diagram...
Страница 91: ...90 Cranesmart LMI Version R9 Technical Specifications 7 500lb single line pull load cell...
Страница 92: ...91 Cranesmart LMI Version R9 15 000 single line pull load cell...
Страница 93: ...92 Cranesmart LMI Version R9 25 000lb single line pull load cell...
Страница 94: ...93 Cranesmart LMI Version R9 40 000lb single line pull load cell...
Страница 95: ...94 Cranesmart LMI Version R9 50 000lb single line pull load cell...
Страница 96: ...95 Cranesmart LMI Version R9 80 000lb single line pull load cell...
Страница 97: ...96 Cranesmart LMI Version R9 Anti 2 Block Switch...
Страница 98: ...97 Cranesmart LMI Version R9 Boom Angle Transducer...
Страница 99: ...98 Cranesmart LMI Version R9 Display Panel...
Страница 100: ...99 Cranesmart LMI Version R9 Alarm Hub...
Страница 101: ...100 Cranesmart LMI Version R9 Wind Speed Transducer...