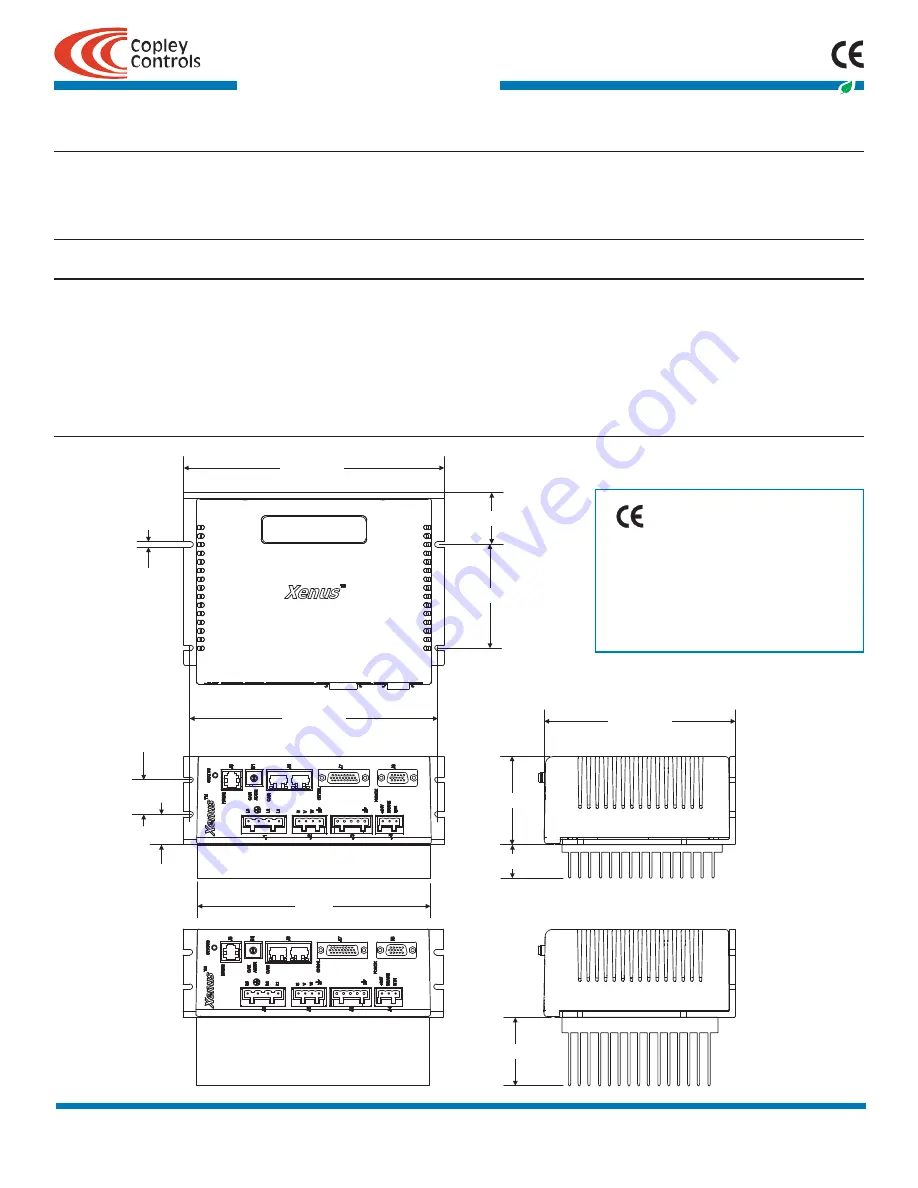
REGEN+
REGEN-
REGEN+
REGEN-
3.00 (76,2)
1.5 (38,1)
7.15 (181,6)
5.54 (140,7)
2.55 (64,8)
1.99 (50,5)
0.925 (23,5)
STANDARD
HEATSINK OPTION (-HS)
6.75
(171,5)
LOW-PROFILE
HEATSINK OPTION (-HL)
0.88 (22,4)
1.00 (25,4)
8 x 0.160
7.55 (191,7)
(4,1)
Chassis Grounding:
For CE compliance and machine
safety use external tooth lockwashers
between mounting screw head and
drive heatplate. Recommended screws
are #6-32 (M3.5) torqued to 8~10
lb·in (0.79~1.02 n·m).
Xenus XTL
™
DIGITAL SERVO DRIVE
for BRUSHLESS/BRUSH MOTORS
Copley Controls, 20 Dan Road, Canton, MA 02021, USA
Tel: 781-828-8090
Fax: 781-828-6547
Tech Support: E-mail: [email protected], Internet: http://www.copleycontrols.com
Page 4 of 30
RoHS
DIMEnSIOnS
Inches (mm)
RESOLVER
RESOLVER
Type
Brushless, single-speed, 1:1 to 2:1 programmable transformation ratio
Resolution
14 bits (equivalent to a 4096 line quadrature encoder)
Reference frequency
7.5 kHz
Reference voltage
2.8 Vrms, auto-adjustable by the drive to maximize feedback
Reference maximum current 100 mA
Maximum RPM
10,000+
EnCODER EMULATIOn
Resolution
Programmable to 16,384 counts/rev (4096 line encoder equivalent)
Buffered encoder outputs
26C31 differential line driver
MOTOR COnnECTIOnS
Phase U, V, W
PWM outputs to 3-phase ungrounded Wye or delta connected brushless motors
Resolver
R1, R2, S1, S2, S3, S4
Motemp [IN5]
Motor overtemperature sensor input. Active level programmable. 4.99 kΩ to +5 Vdc or ground
Disables drive when motor over-temperature condition occurs
Same input circuit as GP digital inputs
Signal ground
Return for temperature sensor
Brake [OUT4]
Current-sinking motor brake driver
+24 Vdc
From drive +24 Vdc power supply to power motor brake
Frame ground
For motor cable shield
FEEDBACk SPECIFICATIOnS (COnTInUED)