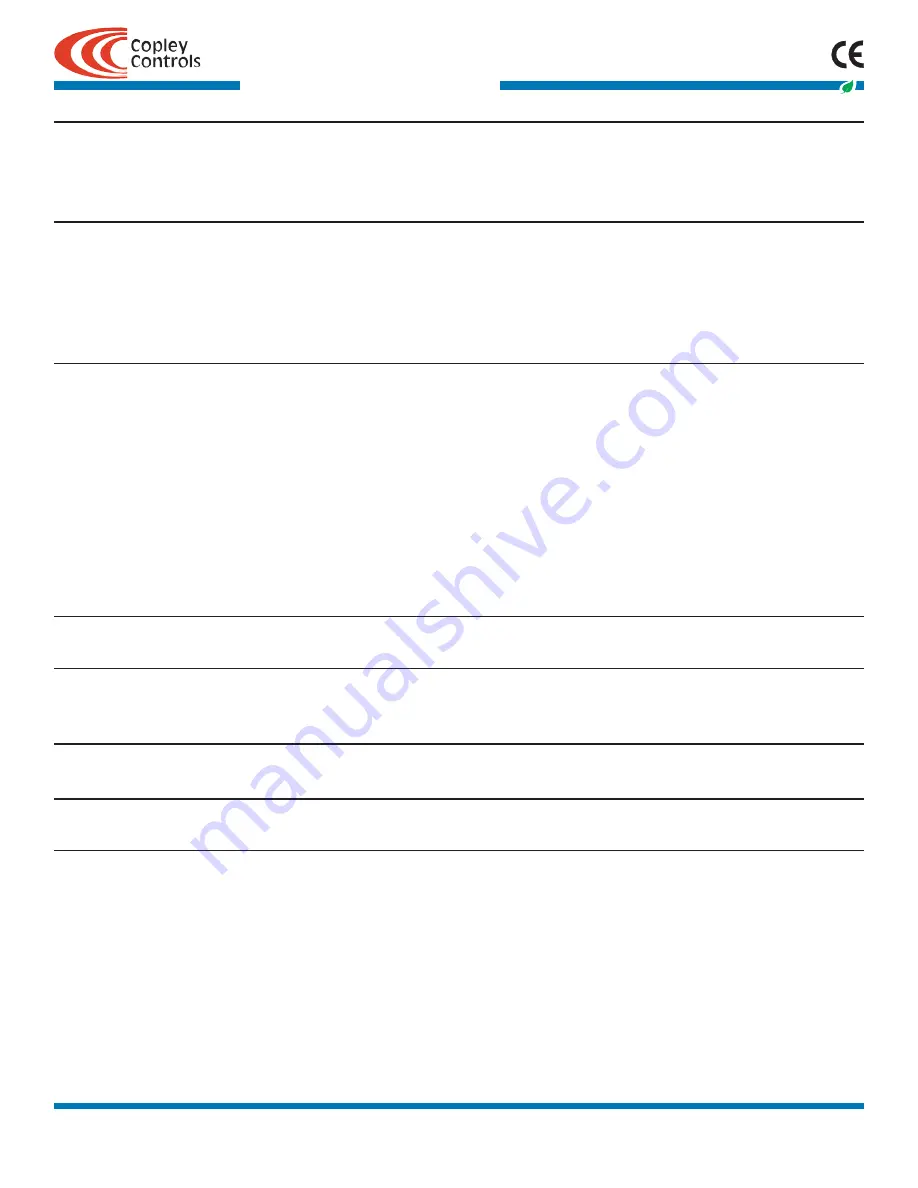
Xenus XTL
™
Copley Controls, 20 Dan Road, Canton, MA 02021, USA
Tel: 781-828-8090
Fax: 781-828-6547
Tech Support: E-mail: [email protected], Internet: http://www.copleycontrols.com
Page 3 of 30
RoHS
DIGITAL SERVO DRIVE
for BRUSHLESS/BRUSH MOTORS
EnCODER
DIGITAL QUAD A/B EnCODER
Type
Quadrature, differential line driver outputs
Signals
A, /A, B, /B, (X, /X, index signals optional)
Frequency
5 MHz line frequency, 20 MHz quadrature count frequency
AnALOG EnCODER
Type
Sin/cos, differential line driver outputs, 0.5 Vpeak-peak (1.0 Vpeak-peak differential)
centered about 2.5 Vdc typical. Common-mode voltage 0.25 to 3.75 Vdc
Signals
Sin(+), sin(-), cos(+), cos(-)
Frequency
230 kHz maximum line (cycle) frequency
Interpolation
10 bits/cycle (1024 counts/cycle)
DIGITAL HALLS
Type
Digital, single-ended, 120° electrical phase difference
Signals
U, V, W
Frequency
Consult factory for speeds >10,000 RPM
EnCODER POWER SUPPLy
Power Supply
+5 Vdc @ 400 mA to power encoders & Halls
Protection
Current-limited to 750 mA @ 1 Vdc if overloaded
Encoder power developed from +24 Vdc so position information is not lost when AC mains power is removed
MOTOR COnnECTIOnS
Phase U, V, W
PWM outputs to 3-phase ungrounded Wye or delta connected brushless motors
Hall U, V, W
Hall signals
Digital Encoder
A, /A, B, /B, X, /X, on standard models
Analog Encoder
Sin(+), sin(-), cos(+), cos(-), X, /X, on -S versions (X & /X index signals are digital)
Hall & encoder power
+5 Vdc @ 400 mA maximum
Motemp [In5]
Motor overtemperature sensor input, 4.99 k
Ω
to +5 Vdc or ground
Signal ground
Return for encoder, Halls, and temperature sensor
Brake [OUT4]
Current-sinking motor brake driver
+24 Vdc
From drive +24 Vdc power supply to power motor brake
Frame ground
For motor cable shield
FEEDBACk SPECIFICATIOnS
GEnERAL SPECIFICATIOnS (COnTInUED)
PROTECTIOnS
HV Overvoltage
+HV > 400 Vdc
Drive PWM outputs turn off until +HV is less than overvoltage
HV Undervoltage
+HV < 60 Vdc
Drive PWM outputs turn off until +HV is greater than undervoltage
Drive over temperature
IGBT > 80 °C ±3 °C
Drive PWM outputs turn off until IGBT temperature is below threshold
Short circuits
Output to output, output to ground, internal PWM bridge faults
I
2
T Current limiting
Programmable: continuous current, peak current, peak time
Motor over temperature
Drive shuts down when motor over-temperature switch changes to high-resistance state, or opens
Feedback power loss
Fault occurs if feedback is removed or +5 V is <85% of normal
MECHAnICAL & EnVIROnMEnTAL
Size
7.55 in (191,8 mm) X 5.57 in (141,5 mm) X 2.57 in (65,3 mm)
Weight
3.0 lb (1.36 kg) for drive without heatsink
1.9 lb (0.86 kg) for XTL-HS heatsink, 1.26 lb (0.57 kg) for XTL-HL heatsink
Ambient temperature
0 to +45 °C operating, -40 to +85 °C storage
Humidity
0% to 95%, non-condensing
Vibration
2 g peak, 10~500 Hz (sine), IEC60068-2-6
Shock
10 g, 10 ms, half-sine pulse, IEC60068-2-27
Contaminants
Pollution degree 2
Environment
IEC68-2: 1990
Cooling
Heat sink and/or forced air cooling required for continuous power output
AGEnCy STAnDARDS COnFORMAnCE
En 55011 : 1998
CISPR 11 (1997) Edition 2/Amendment 2:
Limits and Methods of Measurement of Radio Disturbance Characteristics of Industrial, Scientific, and
Medical (ISM) Radio Frequency Equipment
En 61000-6-1 : 2001
Electromagnetic Compatibility Generic Immunity Requirements
Following the provisions of EC Directive 89/336/EEC:
En 61010-1 2nd Ed.: 2004
Safety Requirements for Electrical Equipment for Measurement, Control, and Laboratory use
Following the provisions of EC Directive 2006/95/EC:
UL 508C 3rd Ed.: 2002
UL Standard for Safety for Power Conversion Equipment