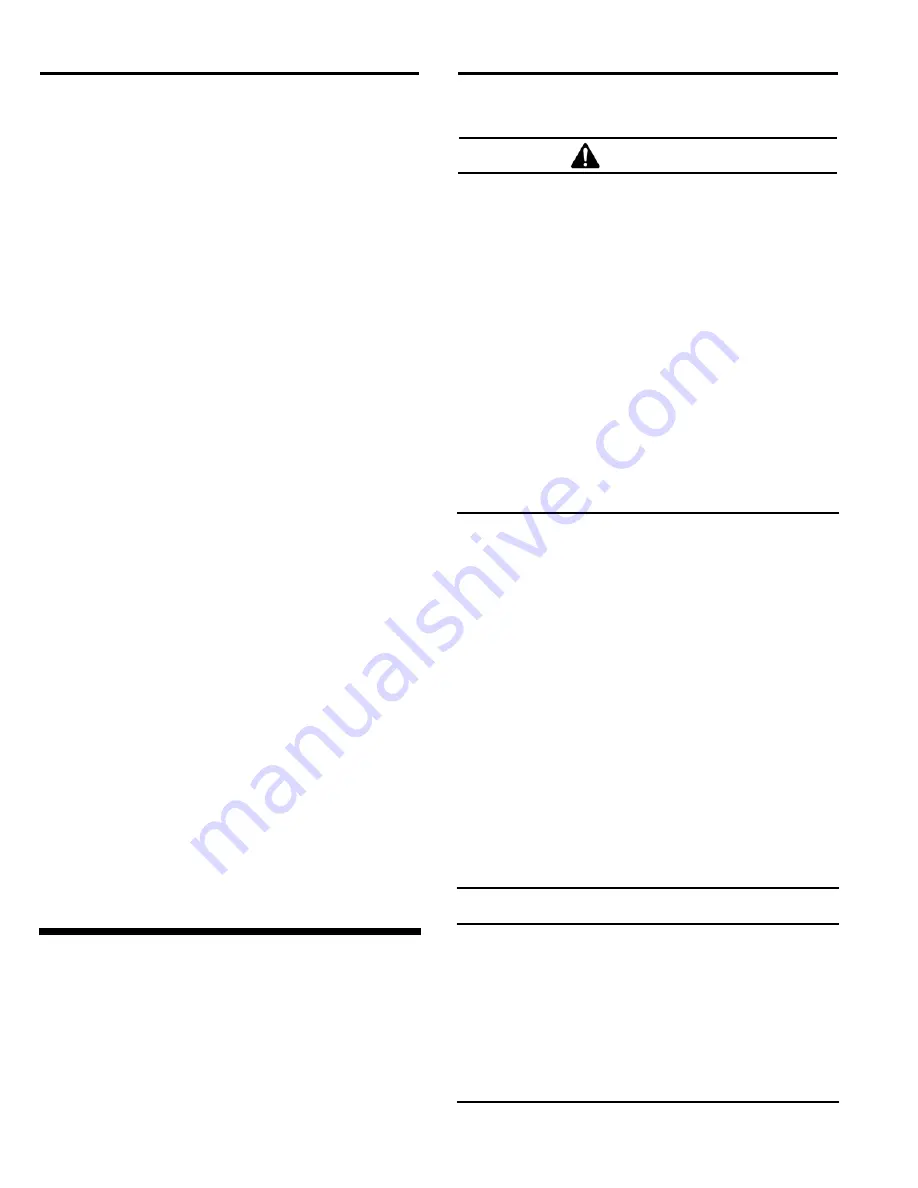
CLASSIC BLAST MACHINE with TLR-100/300 REMOTE CONTROLS
Page 6
© 2018 CLEMCO INDUSTRIES CORP.
www.clemcoindustries.com
Manual No. 22501, Rev. I 02/18
abrasives are especially sensitive to moisture and
require very dry air to prevent bridging in the metering
valve.
1.5.3 Sand:
Sand should never be used because of
the respiratory hazards associated with abrasives
containing free silica.
1.5.4 Slag:
Slag abrasives are compatible with the
blast machine fitted with an FSV metering valve or any
of the alternate metering valves. Obtain safety data
sheet (SDS) to identify hazardous substances.
1.5.5 Steel:
Steel shot and steel grit may be used with
machines fitted with an alternate Quantum or manual
PVR pinch-tube metering valve. Alternate valves are
shown in Section 8.5. Shot applications may require the
use of a pneumatically operated metering valve, such as
the Sentinel or Auto-Quantum, to prevent surging at
startup.
1.5.6
Silicon carbide, aluminum oxide, and garnet:
These are the most aggressive, high-volume abrasives
used in the blasting industry.
These abrasives may be
used, but the service life of any equipment components
which come in contact with the abrasive will be reduced.
Use a nozzle lined with boron carbide with these
abrasives.
1.5.7 Glass
bead:
Most beads are treated to ensure
free-flow operation even under moderately high-
humidity. Glass beads subjected to excessive moisture
may be reused after thorough drying and breaking up of
any clumps. Clean, dry air is a necessity. Glass bead
applications may require the use of a pneumatically
operated metering valve, such as the Sentinel or AQV
Auto-Quantum, which can help to prevent surging at
startup.
1.5.8 Lightweight
media:
Plastic media and most
agricultural media may be used occasionally in a
standard blast machine. Exclusive use of plastic, and
some other lightweight media, requires a blast machine
with a 60
o
conical bottom for continuous, uninterrupted
media flow.
2.0 INITIAL
SETUP
WARNING
Clemco supplies an exhaust muffler with all
blast machines of 2 cuft capacity and larger.
The muffler reduces exhaust noise and
prevents abrasive from exhausting upward or
sideways into the air. When the blast machine
is depressurized, the muffler body pops up to
diffuse the air and abrasive. When the machine
is fully depressurized, the muffler body drops,
permitting trapped abrasive to empty. For the
muffler to work properly, it must be installed
with the body facing up, as shown in Figure 1.
If an application requires the muffler to be
removed, the exhaust piping must be plumbed
to direct exhausting air in a direction that
ensures no persons will be exposed to high
velocity air and abrasive, which escapes when
the blast machine is depressurized.
2.1 Storage
Hopper
2.1.1
When a storage hopper is installed above the
blast machine, an umbrella mounted above the pop-up
opening is required. Refer to Section 8.5, Item 22 for
optional bolt-on umbrella.
2.2
Installation of a Pressure Regulator to
Reduce Blast Pressure
2.2.1
When installing a pressure regulator to reduce
blast pressure below 60 psi (80 psi when using an ACS),
install a tee upstream of the regulator as shown in the
insert in Figure 2, relocate the orifice to the tee, and plug
the orifice port in the inlet valve. This allows the
pneumatic control circuit to operate at line pressure.
2.3
Setup for Multiple Blast Machines Operating
From a Common Compressed-Air Supply
NOTICE
If multiple machines are operating from a
common compressed-air supply and a machine
is under pressure when another machine is
pressurized, the sudden, increased demand for
air could reverse air flow from the machine that
is under pressure and contaminate the
compressed-air supply with abrasive-laden air.
Install check valves at the piping inlet to
prevent the reversal of air.