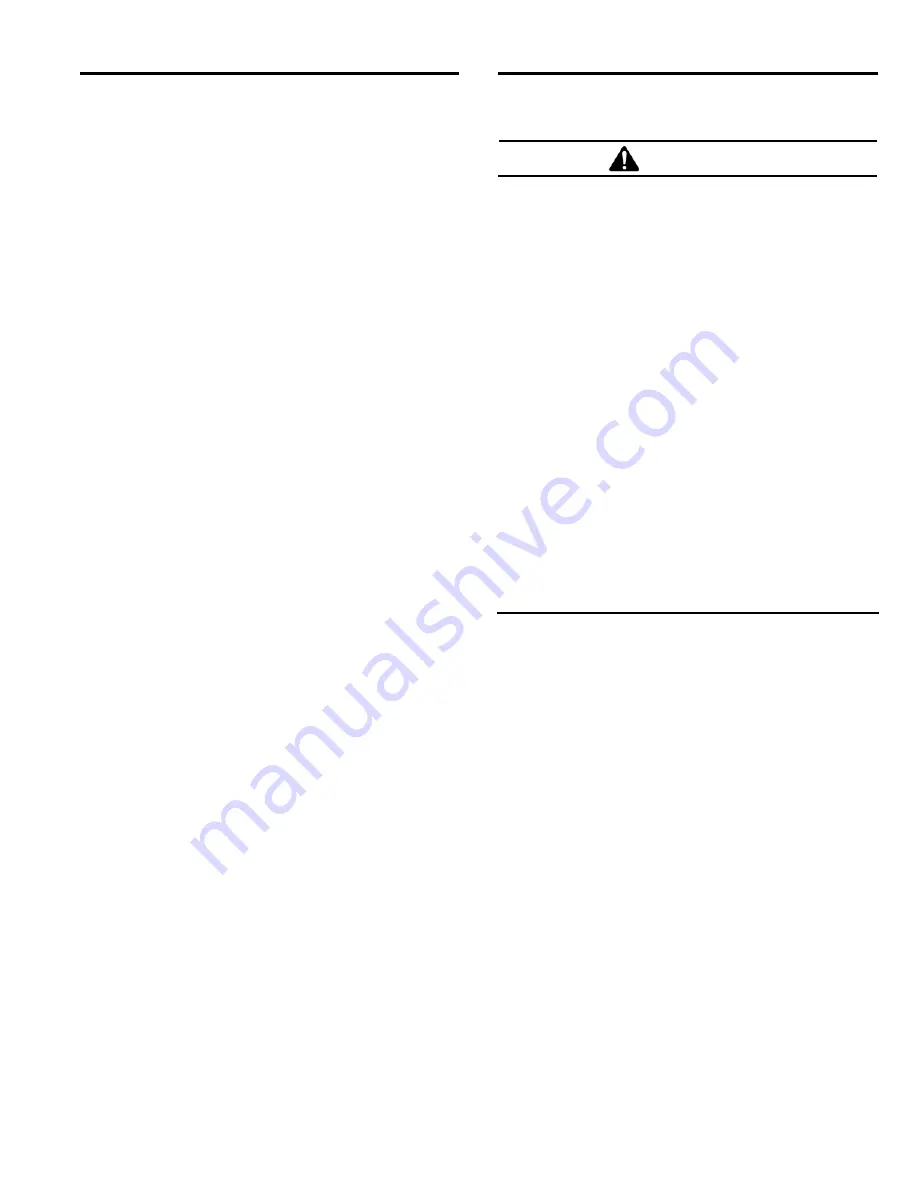
CLASSIC BLAST MACHINE with TLR-100/300 REMOTE CONTROLS
Page 5
© 2018 CLEMCO INDUSTRIES CORP.
www.clemcoindustries.com
Manual No. 22501, Rev. I 02/18
operator presses the control lever, a rubber button
seals the opening, and outbound air returns through
the inbound line to open the inlet valve and close the
outlet valve. This action pressurizes the blast machine
and begins the blasting. Releasing the handle
exhausts the control air, which causes the inlet valve to
close and the outlet valve to open to depressurize the
blast machine and stop the blasting.
1.4.4
Abrasive Cutoff System (ACS) Option
1.4.4.1
The abrasive cutoff switch is mounted on the
control handle. It closes the metering valve so that air
alone without abrasive exits the nozzle. This feature is
used to clear the blast hose and to blowdown the blast
surface.
NOTE: The ACS feature requires a pneumatically
operated abrasive metering valve. It is not available
on Lo-Pot blast machines, which do not have
adequate clearance for the metering valve.
1.4.4.2
Parts used with an optional ACS are shown in
Figure 9. In addition to the standard remote controls, an
ACS also includes a 50-ft. single-line hose, an additional
18-inch-long interconnecting hose, an RLX control
handle with ACS air switch assembly, and a
pneumatically operated metering valve. The metering
valve supplied with the system may differ from the one
shown. A separate owner’s manual is supplied with an
alternate metering valve.
1.4.5
Electric Control Alternate
1.4.5.1
Electric remote controls (electro-pneumatic) are
recommended when the nozzle and remote control
handle are farther than 100 feet from the blast machine.
Pressure drop of pneumatic systems over longer
distances increases response time, which prevents fast,
safe operation. Contact your local Clemco Distributor for
additional information.
1.5 Abrasive
WARNING
Abrasives and dust from blasting may contain
toxic materials (e.g., lead paint, silica) that are
hazardous to workers. Before blasting, obtain a
safety data sheet (SDS) for the blast abrasive
and identify all substances removed by the
blasting process.
• Silica sand (crystalline) can cause silicosis,
lung cancer, and breathing problems in
exposed workers.
• Slags can contain trace amounts of toxic
metals such as arsenic, beryllium, and
cadmium and have the potential to cause
lung disease.
NO DUST IS SAFE TO BREATH. DUST
PRODUCED FROM ANY ABRASIVE OR FROM
THE BLASTING PROCESS CAN CAUSE
SERIOUS LUNG DISEASE AND DEATH WHEN
INHALED. It is the employer’s responsibility to
train employees to identify hazardous
substances and to provide suitable policies,
procedures, monitoring, recordkeeping, and
personal protective equipment.
NOTE: Use only abrasives specifically manufactured
for blasting that are compatible with the surface
being blasted. Abrasives produced for other
applications may be inconsistent in size and shape
and produce an unsatisfactory finish, contain
particles that could jam the abrasive metering valve,
or cause irregular wear.
1.5.1
Selection of blasting abrasive can play a
significant part in worker health risk, job productivity, and
maintenance of the blast machine. DO NOT USE
abrasives containing more than 1% crystalline (free)
silica. Obtain safety data sheets (SDS) for the blasting
abrasive prior to blasting, paying particular attention to
worker health risks and presence of any hazardous/toxic
substances.
1.5.2
Abrasive Mesh Size
1.5.2.1
The choice of abrasive mesh size depends on
the desired profile, cleaning rate, nozzle orifice size, and
availability of clean, dry air. Generally, larger, denser
abrasives provide a deeper profile, while smaller
abrasives clean faster. Most abrasive blasting is done
with abrasive sizes between 16 and 80 mesh. Larger
sizes may be used if the nozzle orifice is large enough to
prevent particles to pass without jamming. Finer