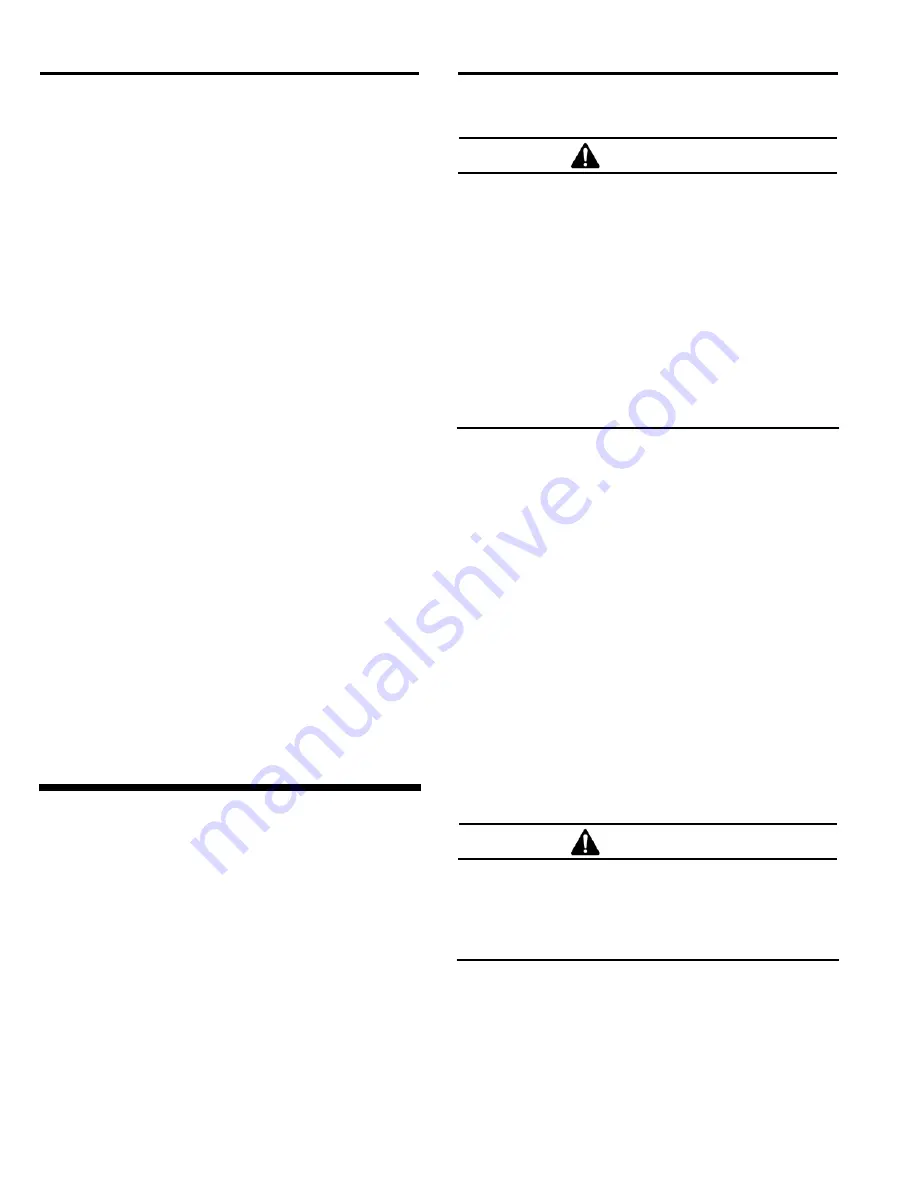
CLASSIC BLAST MACHINE with TLR-100/300 REMOTE CONTROLS
Page 18
© 2018 CLEMCO INDUSTRIES CORP.
www.clemcoindustries.com
Manual No. 22501, Rev. I 02/18
5.3 Monthly
Inspection
5.3.1
With the air OFF before blasting, do the
following:
Check the pop-up valve’s urethane coating for cracks
and grooves. Replace the pop-up valve at the first
sign of wear, per Section 6.7.
Inspect the rubber pop-up seal and replace at the first
sign of wear, drying, or cracking, per Section 6.8.
When an air filter is used, inspect the filter element
and clean the bowl.
5.4 Periodic
Inspection
5.4.1
The remote control system is a safety device.
For safe operation and to avoid unscheduled downtime,
periodically inspect the internal parts of the inlet valve,
outlet valve, and abrasive trap. Inspect for wear and
lubricate O-rings, pistons, springs, seals, and castings.
Refer to Service Maintenance in Sections 6.3, 6.4, or
6.5; and also in Section 6.6.
5.4.2
The control handle is the actuator of the remote
control system. Periodically clean around the springs,
handle lever, and safety lever lock to ensure that the unit
is free of abrasive and debris that may cause the handle
lever or safety lever lock to bind. Refer to the RLX
owner’s manual for service instructions.
5.5 Lubrication
5.5.1
Once per week while the air is OFF, put one or
two drops of lightweight machine oil in the inlet valve
through the safety petcock. This will lubricate the piston
and O-rings in the inlet and outlet valves.
6.0 SERVICE
MAINTENANCE
WARNING
To avoid serious injury from the sudden release
of compressed air, observe the following before
performing any maintenance:
Depressurize the blast machine.
Turn OFF the compressed-air supply.
Bleed the air-supply line to the blast
machine.
Lockout (be certain the air supply is OFF
and that it cannot be started while work is in
process) and tagout (be certain the air
supply is clearly marked to prevent re-
starting while work is in process) the
compressed-air supply.
6.1
Removing Damp Abrasive from the Blast
Machine
6.1.1
To clear a minor blockage caused by damp
abrasive, while blasting, rapidly open and close the
choke valve several times.
6.1.2
For more difficult blockages, refer to Section 6.2
to check for obstructions in the metering valve.
6.1.2.1
With the blast machine depressurized,
disconnect the blast hose and remove the gasket from
the quick coupling on the machine.
6.1.2.2
Close the choke valve and fully open the
abrasive
metering valve.
6.1.2.3
Place the machine so that the outlet is pointed
away from any objects or persons.
WARNING
The machine’s outlet must be pointed away
from any objects or persons. Stand clear of the
path of exiting abrasive. It may come out at high
velocity. Impact from exiting abrasive can
cause severe injury.
6.1.2.4
Pressurize the machine to force out any damp
abrasive.