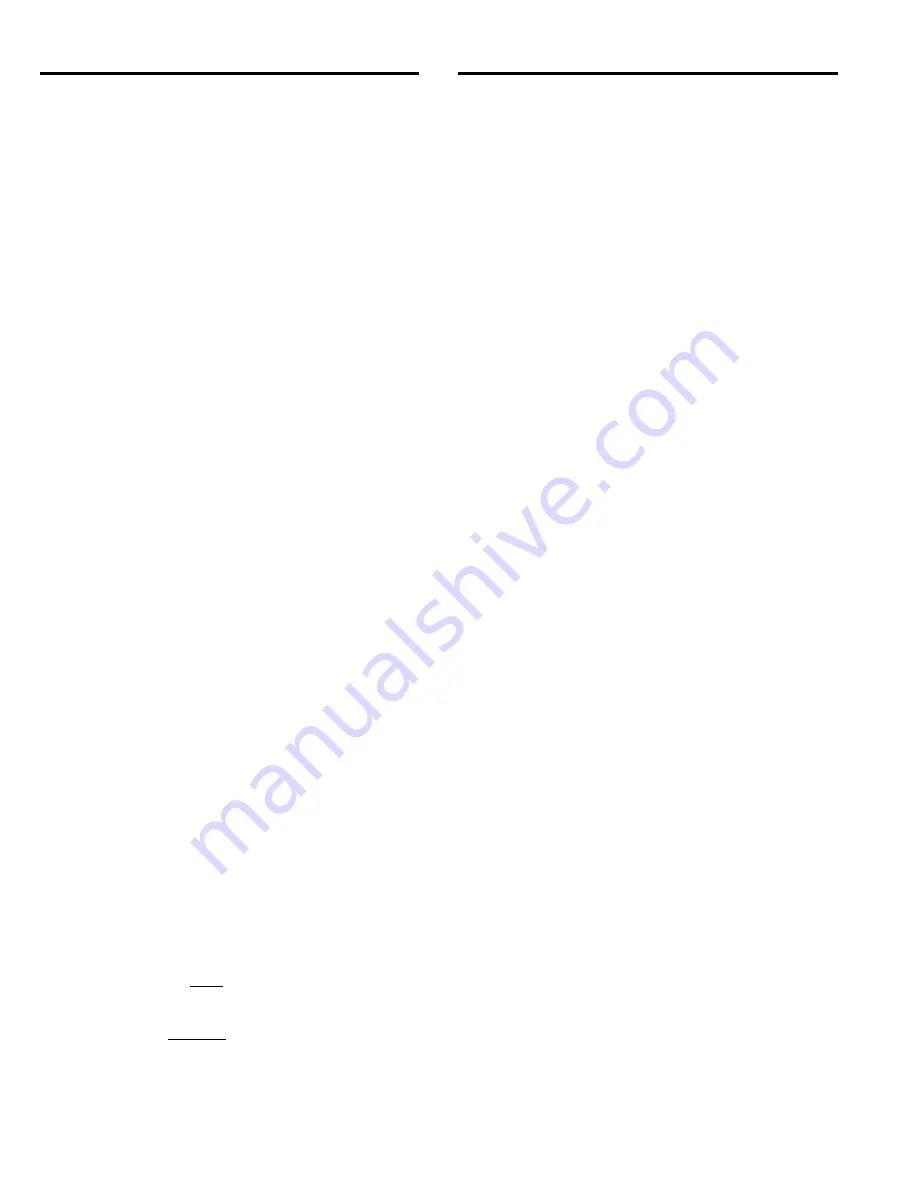
CLASSIC BLAST MACHINE with TLR-100/300 REMOTE CONTROLS
Page 26
© 2018 CLEMCO INDUSTRIES CORP.
www.clemcoindustries.com
Manual No. 22501, Rev. I 02/18
7.6.7
Open the safety petcock and press the control
handle lever; the same volume of air should exhaust from
the petcock as from the control handle before the handle
lever is pressed. If it does not, check the following:
Opening on the control handle is not sealed off.
Air leaks in control handle.
Line from the control handle to the upper fitting on
the inlet valve is blocked.
If a diaphragm outlet valve is used, check the
diaphragm for a split or damage.
If the same volume of air does come out the petcock, the
inlet valve is not functioning. Turn OFF the compressed-
air supply and service the inlet valve per Section 6.3.
7.6.8
Close the safety petcock and press the control
handle lever. Make sure no air escapes through the vent
hole in the cylinder body of the inlet valve body. Air
escaping from the vent indicates a worn piston or piston
O-ring. Service the inlet valve per Section 6.3.
7.6.9
Inlet valve malfunctioning. Inspect internal parts
for wear and lubrication. Refer to Section 6.3.
7.6.10
Compressor too small for the nozzle. Refer to
the compressed air and abrasive consumption table in
Figure 10 for nozzle air consumption.
7.6.11
Reduced air-supply hose or fittings between the
compressor and blast machine. Refer to Section 2.5.
7.6.12
Dirty element in optional air filter. Inspect filter
element.
7.6.13
Pop-up valve stuck, or internal piping worn or
out of alignment. Inspect internal piping.
7.7
Blast Machine Does Not Depressurize or
Depressurizes Too Slowly
7.7.1
Abrasive trap screen blocked, or abrasive trap
needs to be emptied. Inspect the screen and empty the
trap at least twice daily.
7.7.2
Exhaust muffler blocked. Inspect muffler per
Section 6.9.
7.7.3
After releasing the control handle, open the
safety petcock on the inlet valve:
If the machine does depressurizes, control air
remains in the control lines. Refer to Paragraphs
7.7.4, 7.7.5, 7.7.6, and 7.7.7.
If the machine does not depressurize, the inlet valve
is not fully closing or the outlet valve is not fully
opening. Refer to Paragraphs 7.7.8, 7.7.9, and
7.7.10.
7.7.4
Check the pneumatic adaptor gasket on the
control handle for swelling, which restricts air flow
through the handle exhaust opening. The RLX control
handle is covered in Manual No. 10574.
7.7.5
Inspect the exhaust opening in the control handle
pneumatic adaptor; make sure it is clear of obstruction that
restricts air from escaping through the opening.
7.7.6
Check for blockage in the control hose.
7.7.7
Make sure the lower fitting on the inlet valve
(Page 31: Figure 33, Item 4 or Figure 34, Item 4) has not
been switched for a fitting with a full-flow orifice. The
orifice on the 1/8" NPT end of the fitting (the end that
threads into the elbow) must be 1/16" diameter.
7.7.8
Make sure the inlet valve fully closes when the
control handle is released. If it does not seal off
incoming air, service the valve per Section 6.3.
7.7.9
Make sure the piston outlet fully valve opens
when the control handle is released. If it does not,
service the valve per Section 6.3.
7.7.10
Diaphragm in optional diaphragm outlet valve
has taken a set toward the blast machine. Reverse
diaphragm.
7.8
Outlet Valve Leaks Air During Blasting
7.8.1
Outlet valve requires service.
For piston outlet valve, refer to Section 6.4.
For diaphragm outlet valve, refer to Section 6.5.
7.9
Optional ACS Feature
7.9.1
No Abrasive When ACS Toggle is Moved to
ON, Blast Mode.
7.9.1.1
Make sure the machine contains abrasive.
7.9.1.2
Make sure the metering valve is not closed.
7.9.1.3
Make sure the ACS toggle is pointing in the ON
position away from the nozzle.
7.9.1.4
Check for leak or blockage in the single-line hose
or fittings from the control handle to the metering valve.
7.9.1.5
Obstruction in abrasive metering valve, or valve
requires service. Refer to the metering-valve manual for
operation of the valve.