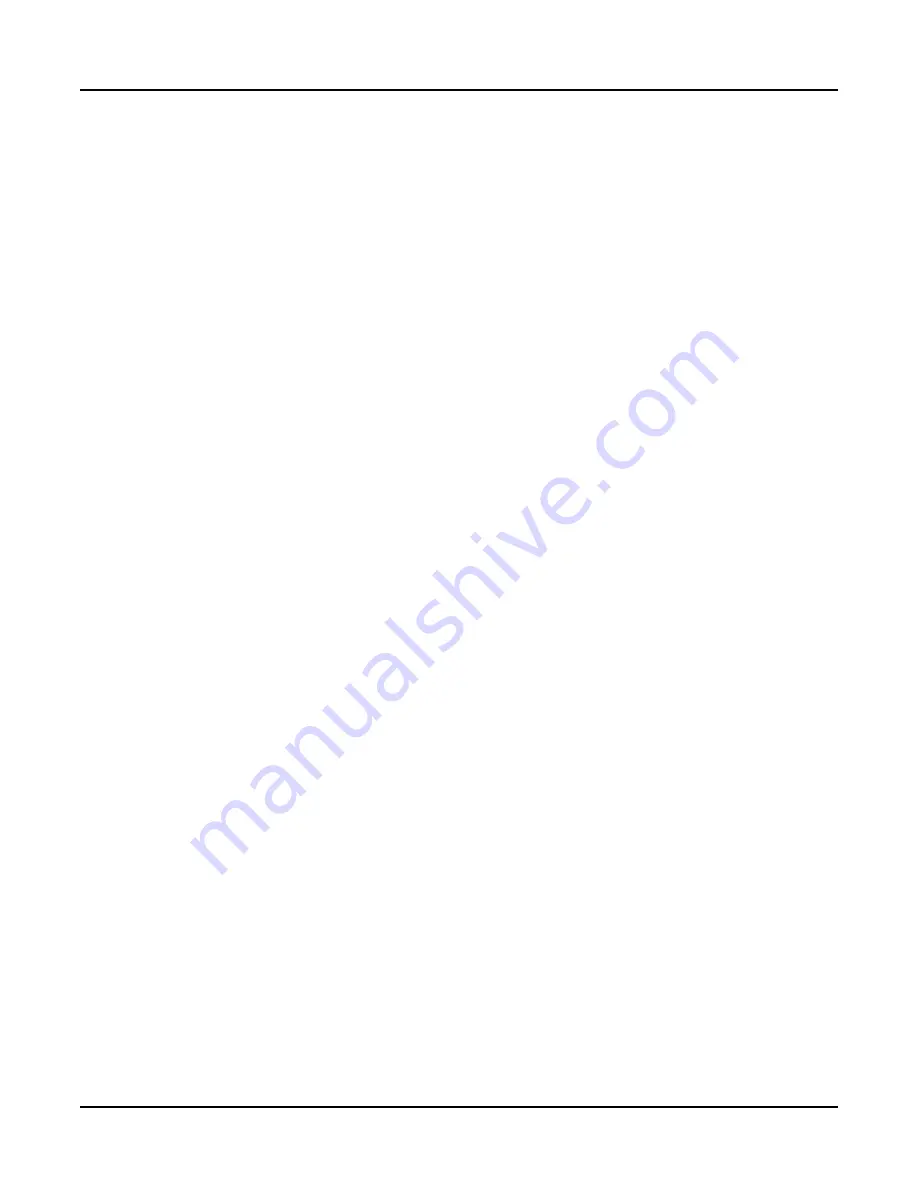
Chapter 5 — Starting and Operating Instructions
5-6
Part No. 750-184
If the oil supply tank is below the level of the oil pump, it is
MANDATORY that the suction line to the pump be completely filled
with oil prior to starting the pump to avoid the possibility of damage
to the pump gears. Non-lubricating fluids such as kerosene should
not be used for priming.
Prior to priming the suction line and the initial start, check to make
certain that all plugs, connections, etc., have been securely
tightened to prevent leaks.
If the fuel oil supply originates from a pressurized loop, it is
assumed that the pressure of the loop will be at a minimum of 75
psi. Under these conditions, the relief valve at the terminal block
should be adjusted to the point where it becomes inoperative (or
removed and openings plugged). To render inoperative, turn the
adjusting screw in as far as possible.
A standard equipped boiler has a selector switch incorporated in the
oil pump motor starter. Momentarily energize the starter to check for
proper pump rotation. With the rotation verified, operate the pump
to determine that oil circulation exists. Observe the regulated oil
pressure gauge for indication that flow is established. If no pressure
shows on the gauge after a few moments, stop the oil pump and re-
prime. If the supply tank is lower than the pump, it is possible that
the initial priming of the suction line, followed by operation of the
pump, will not establish oil flow. This might be caused by
obstruction in the suction line, excessive lift, inadequate priming,
suction line leaks, etc. If oil flow is not readily established, avoid
prolonged operation of the pump to minimize risk of damage to
internal parts of the pump.
If oil flow is not established after a
second or third priming attempt, a full investigation is required to
determine the cause.
A vacuum (or a compound pressure-vacuum) gauge should be
installed at the suction port of the pump and its reading observed
and recorded for future guidance. If a vacuum condition exists, the
reading will reveal the tightness of the system. It is advisable to
maintain the vacuum reading at less than 10" Hg. A vacuum in
excess of 10" Hg. may allow oil to vaporize, causing cavitation, loss
of prime, and unstable firing condition.
Oil Pressure
- Oil supply pressure is regulated by adjusting the
pressure relief valve at the oil terminal block (Figure 2-16). A
pressure gauge should be installed in the terminal block and the
relief valve adjusted to obtain a minimum reading of 75 psi when
the burner is firing at maximum rate.
When oil is supplied from a pressurized loop to a multiple boiler
installation, the relief valve in the loop should be properly adjusted
to provide this reading. In this circumstance, the relief valve at the
terminal block should be adjusted to the point when it will be
inoperative (or removed and openings plugged). To render
inoperative, turn the adjusting screw in as far as possible.
Adjustment may also be required to the regulator on the fuel oil
controller (Figure 2-17). The pressure regulating valve is equipped
with tubing that directs and adds atomizing air pressure to the
Содержание CB Ohio Special 100 HP
Страница 2: ...ii ...
Страница 8: ...viii ...
Страница 42: ...Chapter 2 Burner Operation and Control 2 22 Part No 750 184 ...
Страница 116: ...Chapter 6 Adjustment Procedures 6 28 Part No 750 184 ...
Страница 126: ...Chapter 8 Inspection and Maintenance 8 6 Part No 750 184 ...
Страница 153: ...Chapter 9 Parts Part No 750 184 9 3 Insulated Front Head Model CB LE ...
Страница 154: ...Chapter 9 Parts 9 4 Part No 750 184 Insulated Front Head Interior Model CB LE ...
Страница 155: ...Chapter 9 Parts Part No 750 184 9 5 Insulated Inner Door Model CB OS ...
Страница 156: ...Chapter 9 Parts 9 6 Part No 750 184 Insulated Rear Head CB LE ...
Страница 157: ...Chapter 9 Parts Part No 750 184 9 7 Insulated Rear Head CB LE ...
Страница 158: ...Chapter 9 Parts 9 8 Part No 750 184 Insulated Rear Head CB OS ...
Страница 159: ...Chapter 9 Parts Part No 750 184 9 9 Dry Oven Model CB LE ...
Страница 161: ...Chapter 9 Parts Part No 750 184 9 11 Motor Impeller Model CB LE ...
Страница 162: ...Chapter 9 Parts 9 12 Part No 750 184 Front Head Linkage ...
Страница 170: ...Chapter 9 Parts 9 20 Part No 750 184 Control Cabinet Hawk ICS ...
Страница 171: ...Chapter 9 Parts Part No 750 184 9 21 Control Panel Standard ...
Страница 172: ...Chapter 9 Parts 9 22 Part No 750 184 Entrance Box ...
Страница 173: ...Chapter 9 Parts Part No 750 184 9 23 Front Head Electrical CB LE ...
Страница 174: ...Chapter 9 Parts 9 24 Part No 750 184 Front Head Electrical CB LE ...
Страница 175: ...Chapter 9 Parts Part No 750 184 9 25 Front Head Electrical CB OS ...
Страница 176: ...Chapter 9 Parts 9 26 Part No 750 184 Front Head Electrical CB OS ...
Страница 179: ...Chapter 9 Parts Part No 750 184 9 29 Heavy Oil Piping 60 Steam CB LE ...
Страница 180: ...Chapter 9 Parts 9 30 Part No 750 184 Heavy Oil Piping 60 Steam CB LE SEE TABLE NEXT PAGE ...
Страница 181: ...Chapter 9 Parts Part No 750 184 9 31 Common Oil Parts Heavy Oil ...
Страница 182: ...Chapter 9 Parts 9 32 Part No 750 184 Side Mounted Air Compressor Piping ...
Страница 183: ...Chapter 9 Parts Part No 750 184 9 33 Air Compressor Piping CB OS ...
Страница 185: ...Chapter 9 Parts Part No 750 184 9 35 Light Oil Piping ...
Страница 186: ...Chapter 9 Parts 9 36 Part No 750 184 Light Oil Air Piping Front Head ...
Страница 187: ...Chapter 9 Parts Part No 750 184 9 37 Light Oil Air Piping Front Head PAGE 9 31 ...
Страница 191: ...Chapter 9 Parts Part No 750 184 9 41 Gas Train 125 150 HP ...
Страница 193: ...Chapter 9 Parts Part No 750 184 9 43 Gas Train 200 HP ...
Страница 195: ...Chapter 9 Parts Part No 750 184 9 45 Steam Pressure Controls ...
Страница 196: ...Chapter 9 Parts 9 46 Part No 750 184 Hot Water Temperature Controls ...
Страница 197: ...Chapter 9 Parts Part No 750 184 9 47 Water Column ...
Страница 198: ...Chapter 9 Parts 9 48 Part No 750 184 Water Column ...
Страница 199: ...Chapter 9 Parts Part No 750 184 9 49 Fireside Gaskets CB LE ...
Страница 200: ...Chapter 9 Parts 9 50 Part No 750 184 Fireside Gaskets CB OS ...