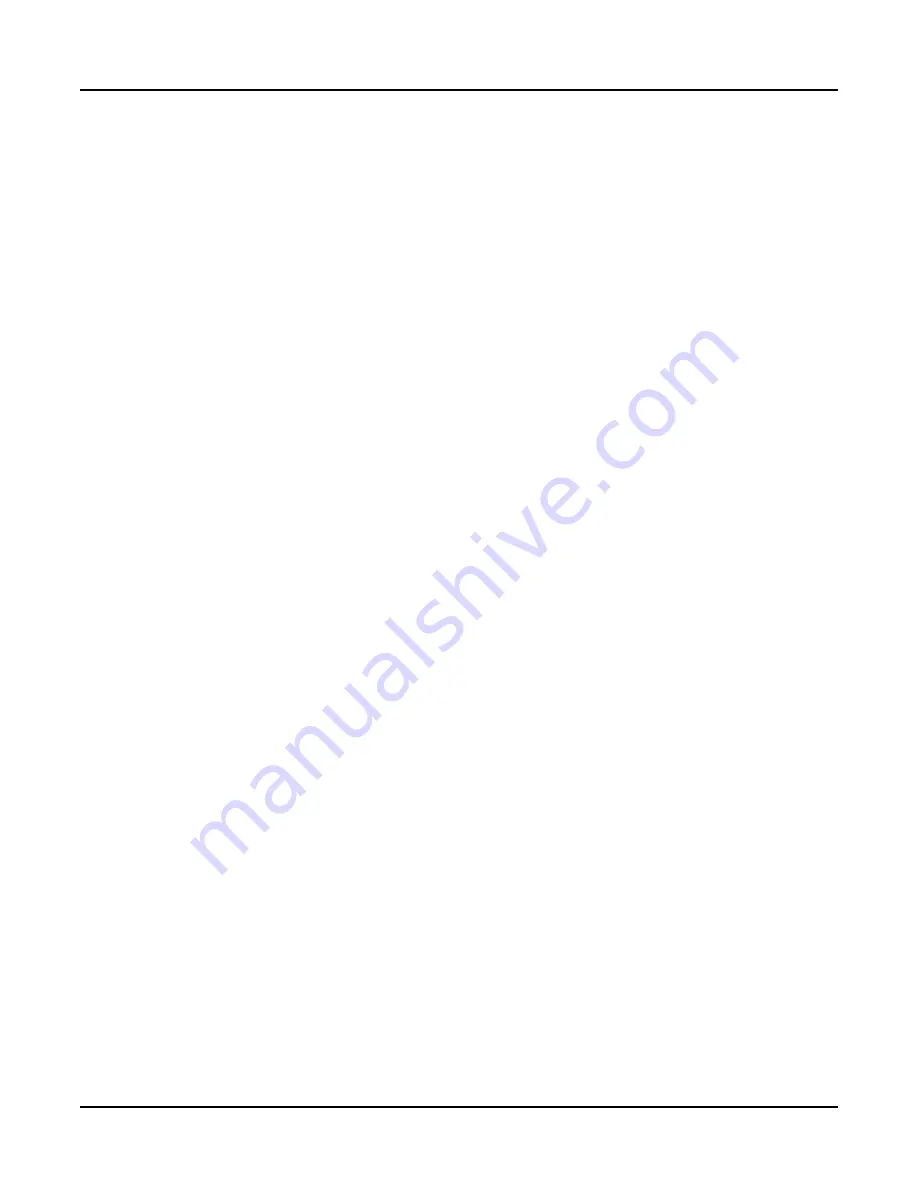
Chapter 8 — Inspection and Maintenance
8-4
Part No. 750-184
C. WATER LEVEL CONTROLS
The need to periodically check water level controls and the waterside of the
pressure vessel cannot be overemphasized. Most instances of major boiler
damage are the result of operating with low water, or the use of untreated
(or incorrectly) treated water.
Always be sure of the boiler water level. On steam boilers, the water column
should be blown down daily. Check samples of boiler water and condensate
in accordance with procedures recommended by your local Cleaver-Brooks
authorized representative. Refer to Sections G and H in Chapter 3
for
blowdown instructions and internal inspection procedures.
Since low water cutoff devices are generally set by the original manufacturer,
no attempt should be made to adjust these controls to alter the point of low
water cutoff or point of pump cut-in or cut-out. If a low water device should
become erratic in operation, or if its setting changes from previously
established levels, contact your local Cleaver-Brooks authorized
representative.
Steam Boiler
The CB Level Master (CB-LE high pressure steam boilers) facilitates
preventive maintenance by providing a daily reminder to the operator that a
water column blowdown is required. A switch on the Level Master control
panel (optional external switch) allows blowdown to be performed while the
boiler is running. Upon completion of the procedure, the Level Master will
indicate a successful blowdown and will time-stamp the event and record it
in controller memory.
The Level Master also has provisions to test the Auxiliary Low Water Cutoff
(ALWCO). To perform the test, open the bottom blowdown valves with the
boiler running. When the water level reaches the ALWCO setpoint, the Level
Master will shut down the boiler. Restore water level and reset the Level
Master controller to continue operation.
For complete information on the Level Master see CB manual #750-233.
CB-LE low pressure steam and CB-OS boilers utilize a snap switch type low
water cutoff. In addition to a normal blowdown routine, the head assembly
should be removed and waterside components inspected annually. Ensure
that the float chamber and equalizing piping are free of sediment and debris.
Hot Water Boiler
It is impractical to blow down the low water cutoff devices on a hot water
boiler since the entire water content of the system would become involved.
Many hot water systems are fully closed and any loss of water will require
make-up and additional feedwater treatment that might not otherwise be
necessary. Since the boiler and system arrangement usually make it
impractical to perform daily and monthly maintenance of the low water
cutoff devices, it is essential to verify proper operation. Remove the
operating mechanism from the bowl annually or more frequently, if possible,
to check and clean float ball, internal moving parts, and the bowl housing.
Also check the cross-connecting piping to be certain that it is clean and free
of obstruction.
Содержание CB Ohio Special 100 HP
Страница 2: ...ii ...
Страница 8: ...viii ...
Страница 42: ...Chapter 2 Burner Operation and Control 2 22 Part No 750 184 ...
Страница 116: ...Chapter 6 Adjustment Procedures 6 28 Part No 750 184 ...
Страница 126: ...Chapter 8 Inspection and Maintenance 8 6 Part No 750 184 ...
Страница 153: ...Chapter 9 Parts Part No 750 184 9 3 Insulated Front Head Model CB LE ...
Страница 154: ...Chapter 9 Parts 9 4 Part No 750 184 Insulated Front Head Interior Model CB LE ...
Страница 155: ...Chapter 9 Parts Part No 750 184 9 5 Insulated Inner Door Model CB OS ...
Страница 156: ...Chapter 9 Parts 9 6 Part No 750 184 Insulated Rear Head CB LE ...
Страница 157: ...Chapter 9 Parts Part No 750 184 9 7 Insulated Rear Head CB LE ...
Страница 158: ...Chapter 9 Parts 9 8 Part No 750 184 Insulated Rear Head CB OS ...
Страница 159: ...Chapter 9 Parts Part No 750 184 9 9 Dry Oven Model CB LE ...
Страница 161: ...Chapter 9 Parts Part No 750 184 9 11 Motor Impeller Model CB LE ...
Страница 162: ...Chapter 9 Parts 9 12 Part No 750 184 Front Head Linkage ...
Страница 170: ...Chapter 9 Parts 9 20 Part No 750 184 Control Cabinet Hawk ICS ...
Страница 171: ...Chapter 9 Parts Part No 750 184 9 21 Control Panel Standard ...
Страница 172: ...Chapter 9 Parts 9 22 Part No 750 184 Entrance Box ...
Страница 173: ...Chapter 9 Parts Part No 750 184 9 23 Front Head Electrical CB LE ...
Страница 174: ...Chapter 9 Parts 9 24 Part No 750 184 Front Head Electrical CB LE ...
Страница 175: ...Chapter 9 Parts Part No 750 184 9 25 Front Head Electrical CB OS ...
Страница 176: ...Chapter 9 Parts 9 26 Part No 750 184 Front Head Electrical CB OS ...
Страница 179: ...Chapter 9 Parts Part No 750 184 9 29 Heavy Oil Piping 60 Steam CB LE ...
Страница 180: ...Chapter 9 Parts 9 30 Part No 750 184 Heavy Oil Piping 60 Steam CB LE SEE TABLE NEXT PAGE ...
Страница 181: ...Chapter 9 Parts Part No 750 184 9 31 Common Oil Parts Heavy Oil ...
Страница 182: ...Chapter 9 Parts 9 32 Part No 750 184 Side Mounted Air Compressor Piping ...
Страница 183: ...Chapter 9 Parts Part No 750 184 9 33 Air Compressor Piping CB OS ...
Страница 185: ...Chapter 9 Parts Part No 750 184 9 35 Light Oil Piping ...
Страница 186: ...Chapter 9 Parts 9 36 Part No 750 184 Light Oil Air Piping Front Head ...
Страница 187: ...Chapter 9 Parts Part No 750 184 9 37 Light Oil Air Piping Front Head PAGE 9 31 ...
Страница 191: ...Chapter 9 Parts Part No 750 184 9 41 Gas Train 125 150 HP ...
Страница 193: ...Chapter 9 Parts Part No 750 184 9 43 Gas Train 200 HP ...
Страница 195: ...Chapter 9 Parts Part No 750 184 9 45 Steam Pressure Controls ...
Страница 196: ...Chapter 9 Parts 9 46 Part No 750 184 Hot Water Temperature Controls ...
Страница 197: ...Chapter 9 Parts Part No 750 184 9 47 Water Column ...
Страница 198: ...Chapter 9 Parts 9 48 Part No 750 184 Water Column ...
Страница 199: ...Chapter 9 Parts Part No 750 184 9 49 Fireside Gaskets CB LE ...
Страница 200: ...Chapter 9 Parts 9 50 Part No 750 184 Fireside Gaskets CB OS ...