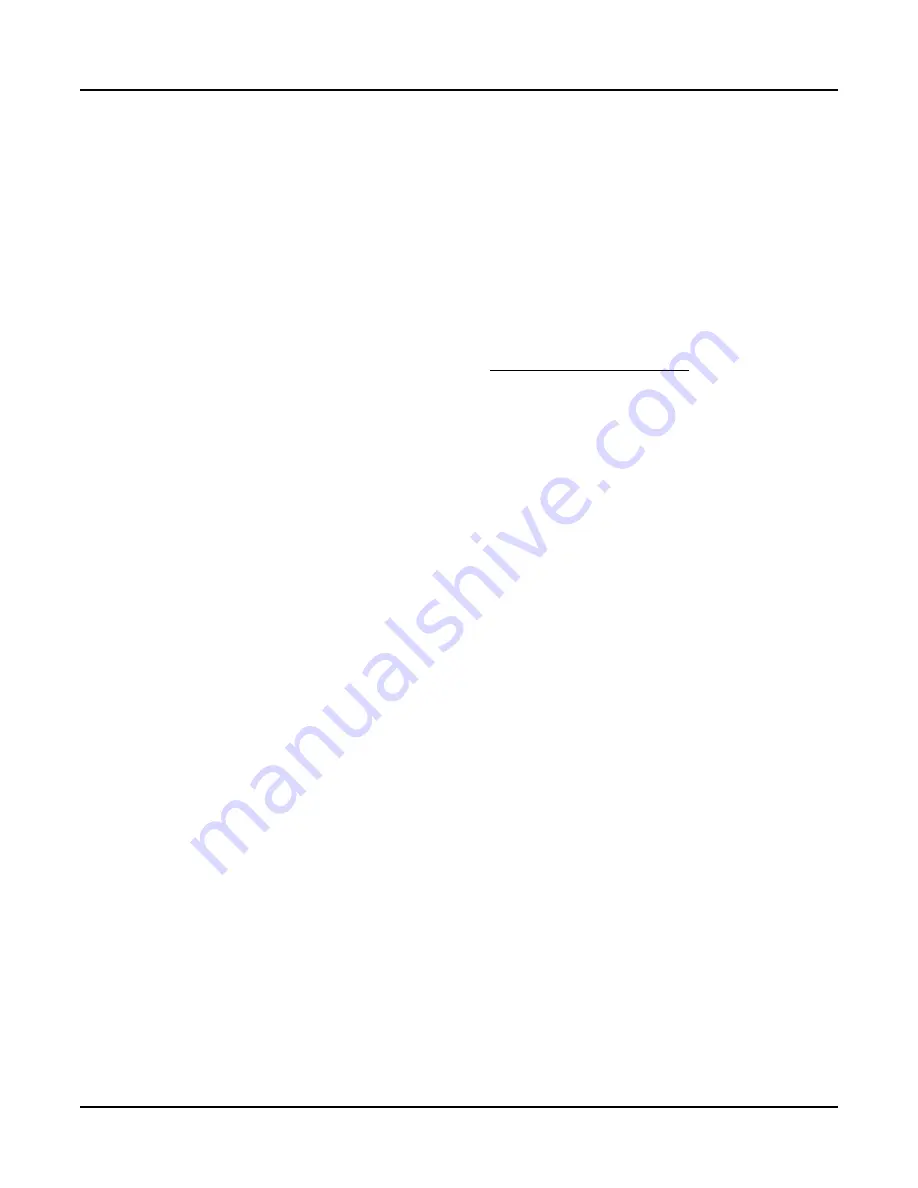
Chapter 4 — Sequence of Operation
4-6
Part No. 750-184
follow these instructions could result in serious personal injury or
death
Run Cycle
- With main flame established, the program relay releases the
modulating damper motor (MDM) from its low fire position to control by
either the manual flame control (MFC) or the modulating control (MC),
depending upon the position of the manual-automatic switch (MAS). This
allows operation in ranges above low fire.
With the manual-automatic switch (MAS) set at automatic, subsequent
modulated firing will be at the command of the modulating control (MC),
which governs the position of the modulating damper motor (MDM). The air
damper and fuel valves are actuated by the motor through a linkage and cam
assembly to provide modulated firing rates.
Notice
Note: Normal operation of the burner should be with the
switch in the manual-automatic position and under the
direction of the modulating control. The manual position is
provided for initial adjustment of the burner over the entire
firing range. When a shutdown occurs while operating in the
manual position at other than low fire, the damper will not be
in a closed position, thus allowing more air than desired to
flow through the boiler. Excess air flow subjects the
pressure vessel metal and refractory to undesirable
conditions. The effectiveness of nozzle purging is lost on a
No. 6 oil burner.
The burner starting cycle is now complete. The (LDL) and (FVL) lights on the
panel remain lit. Demand firing continues as required by load conditions.
Burner Shudown-Post Purge -
The burner will fire until steam pressure or
water temperature in excess of demand is generated. With modulated firing,
the modulating damper motor (MDM) should return to the low fire position
before the operating limit control (OLC) opens. When the limit control circuit
is opened, the following sequence occurs:
The main fuel valve circuit is deenergized, causing the main fuel valve
(MGV) or (OV) to close. The flame is extinguished. The control panel lights
(LDL) and (FVL) are turned off. The blower motor continues to run to force
air through the boiler for the post purge period.
On a No. 6 oil burner, the air purge valve (APV) is powered from the blower
motor start circuit via the contacts of the air purge relay (APR) to provide an
air purge of the oil nozzle. The damper motor returns to the low fire position
if it is not already in that position.
The blower motor start circuit is deenergized at the end of the post purge
cycle and the shutdown cycle is complete.
The program relay is now ready for subsequent recycling, and when steam
pressure or water temperature drops to close the contacts of the operating
control, the burner again goes through its normal starting and operating
cycle.
D. FLAME LOSS SEQUENCE
The program relay will recycle automatically each time the operating control
closes, or after a power failure. It will lockout following a safety shutdown
Содержание CB Ohio Special 100 HP
Страница 2: ...ii ...
Страница 8: ...viii ...
Страница 42: ...Chapter 2 Burner Operation and Control 2 22 Part No 750 184 ...
Страница 116: ...Chapter 6 Adjustment Procedures 6 28 Part No 750 184 ...
Страница 126: ...Chapter 8 Inspection and Maintenance 8 6 Part No 750 184 ...
Страница 153: ...Chapter 9 Parts Part No 750 184 9 3 Insulated Front Head Model CB LE ...
Страница 154: ...Chapter 9 Parts 9 4 Part No 750 184 Insulated Front Head Interior Model CB LE ...
Страница 155: ...Chapter 9 Parts Part No 750 184 9 5 Insulated Inner Door Model CB OS ...
Страница 156: ...Chapter 9 Parts 9 6 Part No 750 184 Insulated Rear Head CB LE ...
Страница 157: ...Chapter 9 Parts Part No 750 184 9 7 Insulated Rear Head CB LE ...
Страница 158: ...Chapter 9 Parts 9 8 Part No 750 184 Insulated Rear Head CB OS ...
Страница 159: ...Chapter 9 Parts Part No 750 184 9 9 Dry Oven Model CB LE ...
Страница 161: ...Chapter 9 Parts Part No 750 184 9 11 Motor Impeller Model CB LE ...
Страница 162: ...Chapter 9 Parts 9 12 Part No 750 184 Front Head Linkage ...
Страница 170: ...Chapter 9 Parts 9 20 Part No 750 184 Control Cabinet Hawk ICS ...
Страница 171: ...Chapter 9 Parts Part No 750 184 9 21 Control Panel Standard ...
Страница 172: ...Chapter 9 Parts 9 22 Part No 750 184 Entrance Box ...
Страница 173: ...Chapter 9 Parts Part No 750 184 9 23 Front Head Electrical CB LE ...
Страница 174: ...Chapter 9 Parts 9 24 Part No 750 184 Front Head Electrical CB LE ...
Страница 175: ...Chapter 9 Parts Part No 750 184 9 25 Front Head Electrical CB OS ...
Страница 176: ...Chapter 9 Parts 9 26 Part No 750 184 Front Head Electrical CB OS ...
Страница 179: ...Chapter 9 Parts Part No 750 184 9 29 Heavy Oil Piping 60 Steam CB LE ...
Страница 180: ...Chapter 9 Parts 9 30 Part No 750 184 Heavy Oil Piping 60 Steam CB LE SEE TABLE NEXT PAGE ...
Страница 181: ...Chapter 9 Parts Part No 750 184 9 31 Common Oil Parts Heavy Oil ...
Страница 182: ...Chapter 9 Parts 9 32 Part No 750 184 Side Mounted Air Compressor Piping ...
Страница 183: ...Chapter 9 Parts Part No 750 184 9 33 Air Compressor Piping CB OS ...
Страница 185: ...Chapter 9 Parts Part No 750 184 9 35 Light Oil Piping ...
Страница 186: ...Chapter 9 Parts 9 36 Part No 750 184 Light Oil Air Piping Front Head ...
Страница 187: ...Chapter 9 Parts Part No 750 184 9 37 Light Oil Air Piping Front Head PAGE 9 31 ...
Страница 191: ...Chapter 9 Parts Part No 750 184 9 41 Gas Train 125 150 HP ...
Страница 193: ...Chapter 9 Parts Part No 750 184 9 43 Gas Train 200 HP ...
Страница 195: ...Chapter 9 Parts Part No 750 184 9 45 Steam Pressure Controls ...
Страница 196: ...Chapter 9 Parts 9 46 Part No 750 184 Hot Water Temperature Controls ...
Страница 197: ...Chapter 9 Parts Part No 750 184 9 47 Water Column ...
Страница 198: ...Chapter 9 Parts 9 48 Part No 750 184 Water Column ...
Страница 199: ...Chapter 9 Parts Part No 750 184 9 49 Fireside Gaskets CB LE ...
Страница 200: ...Chapter 9 Parts 9 50 Part No 750 184 Fireside Gaskets CB OS ...