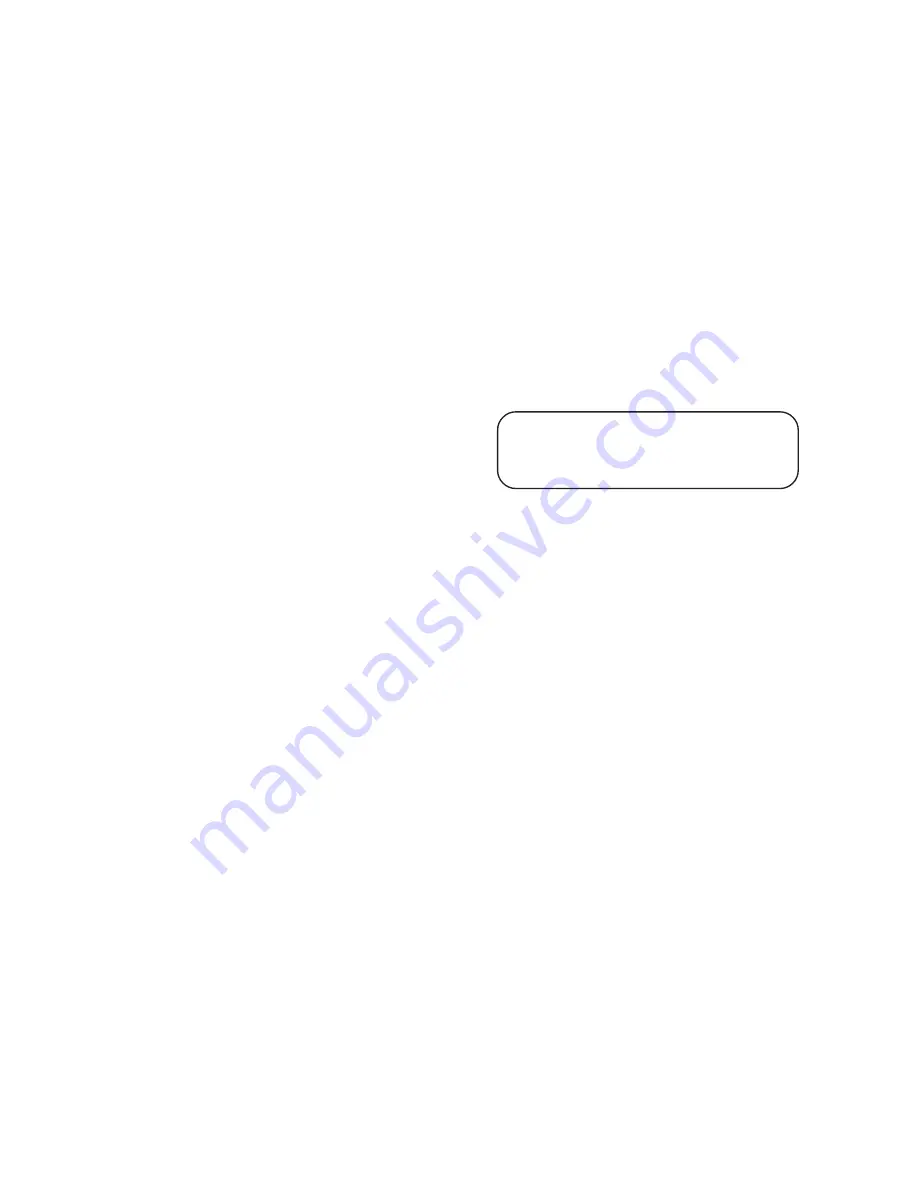
31
7:7 RECOMMENDED COMMISSIONING CHECK LIST - SHEET 1 OF 2
Customer...................................................................
Appliance Model...........................................
Site Address..............................................................
Serial No......................................................
.................................................................................. Fuel...................................................
Tick off each item.
OIL TANK
Is there sufficient oil, and of the correct grade for
the appliance?
Is the tank adequately supported?
Is a damp-proof membrane inserted between the
tank and support? (Non plastic tanks).
Does the tank slope at least 20 mm per metre of
length downwards towards the sludge cock? (Non
plastic tanks).
Is the tank painted or suitably protected exter-
nally?
Is the Tank fitted with the following:
Contents gauge
Suitable hinged combined fill and
vent cover, or capped fill and vent
pipes.
Outlet valve
Filter
Sludge cock. (Non plastic tanks).
HEIGHT OF TANK
Is the bottom of the tank above the oil pump if a
single pipe system is installed?
OIL SUPPLY LINE
Ensure that galvanised iron has not been used.
If black iron has been used, is it protected against
corrosion?
Ensure that soldered connections on copper pipes
have not been used.
Is the size of pipe adequate for the Heater
rating?
Are all joints leak proof?
Is a fire valve fitted?
Is a filter fitted? (correct way round)
Is the oil line connected to the correct inlet con-
nection of the pump?
Is the oil supply clean and free of water or other
contamination?
Disconnect oil supply as close to the burner as
possible and drain approximately a gallon of oil
into a very clean container. Inspect the oil for
impurities and repeat the process if necessary.
Do not re-connect the oil line until water
and all impurities have been removed from
the oil supply
.
IF NOT THIS MAY DAMAGE THE PUMP
Clean oil filters and de-sludge oil tank if neces-
sary.
TWO PIPE OIL SYSTEMS
Is a spring-loaded non-return oil valve fitted in
the suction line? (or a 3K Oil Deaerator).
Does the return oil line terminate in the tank at
the same level as the suction outlet?
Has an anti-syphon cut been made in the return
oil line (inside the tank)?
HEATER
Is the Heater standing on a level incombustible
hearth?
Are the thermostat sensors inserted in their pock-
ets?
Are the baffles and bottom insulation (where ap-
plicable) correctly located?
Is the Heater set for the fuel being supplied?
Is the Heater flueway inspection cover screwed
down sufficiently firmly to form a seal?
Is the central Screw in the Access Panel tight-
ened down finger tight to stop the baffles rattling?
9-04-02
Содержание COH110
Страница 60: ...14 Fig 4 9b Reillo bypass adjustment 9 04 02 Fig 4 9a Reillo bypass adjustment ...
Страница 63: ...17 9 04 02 ...
Страница 82: ...36 9 04 02 ...
Страница 83: ...37 Model 220 only Fig 8 3c Model 280 only Fig 8 3d Top Top Top 9 04 02 ...
Страница 86: ...40 9 3 BURNER PARTS 9 04 02 Model 110 443T58 ...
Страница 87: ...41 29 01 08 Model 180 459T55 3007708 ...
Страница 88: ...42 29 01 08 Model 220 464T55 3007708 ...
Страница 96: ...Station Lane Industrial Estate Witney Oxon Tel 01993 778855 Fax 01993 703407 Booklet 12 M3491 7 11 02 ...