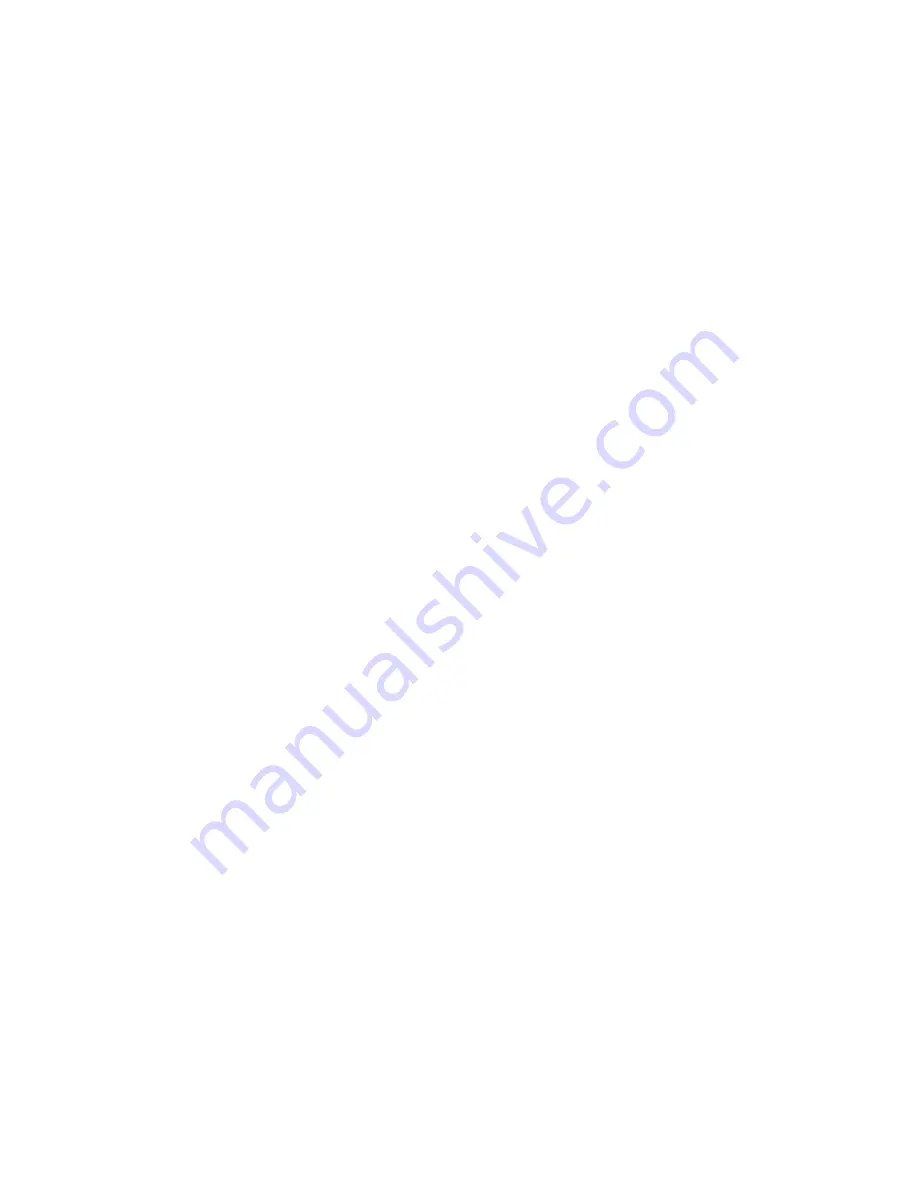
35
normal running mode, these limits will prevent stages from be-
ing added, or stages to be removed, as applicable. In test mode,
these limits are ignored, and the user may continue to operate all
stages. The point MODEDMDL (
Run Status
MODE
D.LMT
) is used to show if any Demand Limiting is in
effect that prevents the unit from operating either cooling or
heating at full-capacity.
NOTE: MODEDMDL may reflect that staging is NOT limited
even though Loadshed is active, or the network points are being
forced, if the stage limits in effect are not less than the stages pres-
ent in the unit.
If a more drastic mode of Demand Limiting is required, the
network point HVACDOWN (
Run Status
MODE
HV.DN
)
can be used to prohibit the unit from selecting any HVAC
mode, thus preventing the operation of the supply fan, com-
pressors, condenser fans, and heat stages. This point must also
be forced, and is reset automatically when not forced, and at
POR.
NOTE: HVACDOWN can be used as an immediate shutdown of
the unit before limiting capacity (ex. Generator switching).
Linkage
Comfort
Link controls do not require any configuration settings
to establish linkage with a Linkage Coordinator. This is done
automatically when the unit’s bus and element address are con-
figured in the Linkage Coordinator’s LINKAGE configuration
table. The linkage information that is supplied to the
Com-
fort
Link unit by the Linkage Coordinator is as follows:
• Reference zone temperature
• Reference zone occupied biased heating and cooling set
points
• Reference zone unoccupied heating and cooling set points
• Composite occupancy mode
The unit will control the equipment based on this information
and in return will provide the Linkage Coordinator with the
following data:
• Operating mode - Cooling, Heating, Free Cooling, Fire
Shutdown Evacuation, or Off
• Supply-air temperature
• Optimal Start Bias time (Based on worst case zone)
This synchronization of data optimizes the efficiency of the
unit and the zones to operate at peak system performance at all
times. This information can be seen in linkage maintenance ta-
bles of the Linkage Coordinator and the RTU; it is updated at
approximately 1-minute intervals.
Cooling and heating operation is slightly modified during
Linkage control. A PID loop is run to calculate required stages.
This is necessary because in stand alone operation, the unit
tries to anticipate the space. With Linkage, the unit must try to
satisfy the demand as soon as possible. The PID configurations
are in
Configuration
PID
. These values have been field test-
ed and the default values should NOT BE CHANGED.
For information on set up and configuration, see the Space
Temperature Control-CCN Linkage text in the Controls Quick
Start section of this book.
For additional information on the Linkage Coordinator or Zone
Controllers, please refer to their appropriate manuals.
Alarm Handling
There are a variety of different alerts and alarms in the system.
Alerts are indicated by TXXX (where XXX is the alert num-
ber) on the display and generally signify that the improperly
functioning circuit can restart without human interaction. If an
alarm occurs, indicated by AXXX (where XXX is the alarm
number), the damaged circuit will generally not restart without
an alarm reset via the scrolling marquee display or CCN.
The response of the control system to various alerts and alarms
depends on the seriousness of the particular alert or alarm. In
the mildest case, an alert does not affect the operation of the
unit in any manner. An alert can also cause a “strike.” A “strik-
ing” alert will cause the circuit to shut down for 15 minutes.
This feature reduces the likelihood of false alarms causing a
properly working system to be shut down incorrectly. If three
strikes occur before the circuit has an opportunity to show that
it can function properly, the circuit will strike out, causing the
shutdown alarm for that particular circuit. Once activated, the
shutdown alarm can only be cleared via an alarm reset.
However, circuits with strikes will be given an opportunity to
reset their strike counter to zero. As discussed above, a strike
typically causes the circuit to shut down. Fifteen minutes later,
that circuit will once again be allowed to run. If the circuit is
able to run for 1 minute, its replacement circuit will be allowed
to shut down (if not required to run to satisfy requested stages).
However, the “troubled” circuit must run continuously for a
user defined time (
Configuration
COOL
RST.C
) with no
detectable problems before the strike counter will be reset to
zero. Default value is 5 minutes.
CCN ALARM BROADCAST
Operators of CCN networks might not want to be notified of
“striking” alerts for refrigerant circuits until the circuit has
been shut down due to 3 strikes. Set the cooling configuration
of Alert Each Strike (
Configuration
COOL
ALM.N
on dis-
play, ALM_NOW on CCN) to YES to broadcast each circuit
strike alert. Set Alert Each Strike to NO to broadcast only cir-
cuit shut down. Alert Each Strike configuration is ignored
during Service Test and all alerts are broadcast.
ALARM RELAY OUTPUT
The alarm relay output is a normally open 24 vac output be-
tween field connection terminal board terminals C and X. Se-
lection of which alerts and alarms will result in closing of the
alarm relay may be set in the Alarm Relay Configuration (
Con-
figuration
ALM.O
). Setting a configuration to YES will re-
sult in the alarm output relay, ALRM, status of ON and 24 vac
between C and X on the field connection terminal board when
that particular condition is in an alarm state. Setting a configu-
ration to NO will result in no action by the alarm output relay
for that particular condition.
NOTE: An accessory filter switch can be used along with the
alarm relay output function to indicate dirty filter service need.
See the Troubleshooting section for more information on view-
ing, diagnosing, and clearing alerts and alarms.
EnergyX
®
Units
GENERAL
An EnergyX unit is a 48/50HC rooftop unit and energy recov-
ery ventilator (ERV). It operates the ERV module in an inte-
grated manner with the base rooftop unit. The base rooftop unit
functions per the base unit sequence of operation, for informa-
tion regarding
Comfort
Link controller operation see the
Com-
fort
Link Controls, Start-Up, Operations, and Troubleshooting
Instructions. The ERV will operate based on communication
from the
Comfort
Link controller. The following section dis-
cusses the ERV operation in detail. In summary, the ERV oper-
ates to provide pre-conditioned outside air for ventilation re-
quirements. If equipped with an optional economizer the ERV
can provide free cooling when the outside air conditions are
satisfactory.
In general the ERV monitors occupancy and indoor fan state of
the base unit to determine when to activate. The outside air
fan(s) bring in the outside air pass it through the enthalpy
wheel and into the rooftop mixing box. The building return air
is pulled through the enthalpy wheel by the exhaust fan(s) and
released outside. During operation the enthalpy wheel is rotat-
ing to use the building air to pre-condition the outside air.
Содержание /50HC 04-28
Страница 61: ...61 Fig 21 Saturated Condensing Temperature Thermistor Location 48 50HC 14 SCT B SCT A CIRCUIT B CIRCUIT A ...
Страница 69: ...69 Fig 24 Typical Control Diagram for 48HC 04 14 Units 48HC 08 09 shown ...
Страница 70: ...70 Fig 25 Typical Power Diagram for 48HC 04 14 Units 48HC 08 09 shown ...
Страница 71: ...71 Fig 26 Typical Control Diagram for 50HC 04 14 Units 50HC 14 shown ...
Страница 72: ...72 Fig 27 Typical Power Diagram for 50HC 04 14 Units 50HC 14 Non Humidi MiZer shown ...
Страница 73: ...73 Fig 28 Typical Control Diagram 48HC 17 28 Units ...
Страница 74: ...74 Fig 29 Typical Control Diagram 50HC 17 28 Units ...
Страница 75: ...75 Fig 30 Typical Humid MiZer Power Diagram and Component Arrangement 48 50HC 17 28 Units ...
Страница 76: ...76 Fig 31 Typical Non Humid MiZer Power Diagram and Component Arrangement 48 50HC 17 28 Units ...
Страница 89: ...89 Fig 42 Modulating ERV Wiring Schematic ...
Страница 90: ...90 Fig 43 EnergyX ERV Control Box Component Layouts ...
Страница 101: ...101 Fig 59 Exhaust Fan Assembly Removal Exhaust Fan Assembly ...
Страница 141: ......