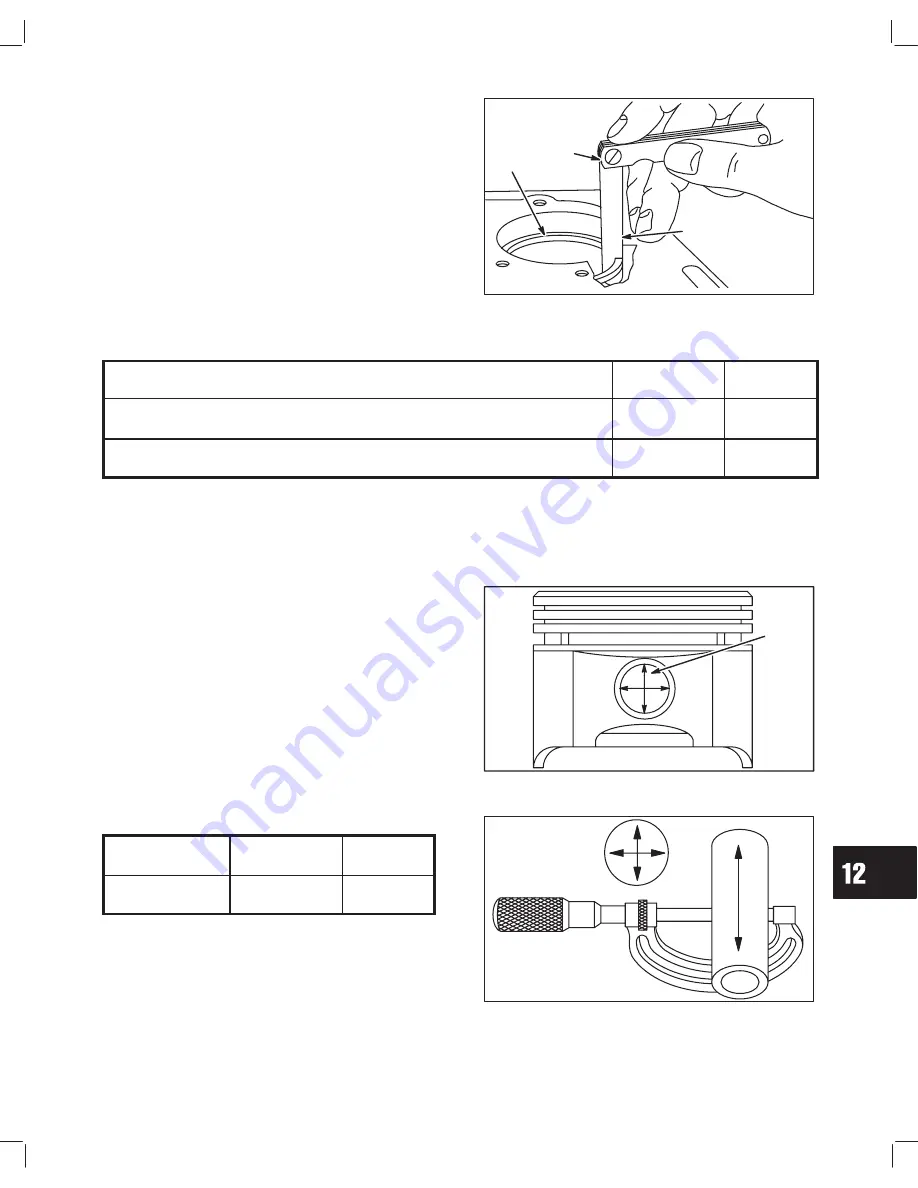
12
3
Check Rings
To check rings, first clean all carbon from the end of the
rings. Insert old rings one at a time, approximately one
inch down into the cylinder bore.
Check ring end gap with feeler gauge, Fig. 5. If ring end
gap is greater than shown in Table No. 1, the ring is
worn and should be replaced.
A worn ring will usually show scratches caused by
abrasives and/or have a shiny appearance. Also, the
top and bottom edges of the ring may be extremely
sharp. Never reuse worn piston rings.
ÇÇ
ÇÇ
ÇÇ
Fig. 5 – Checking Ring Gap
FEELER
GAUGE
RING
SEE CHART
Ring End Gap Rejection Size
ÁÁÁÁÁÁÁÁÁÁÁÁÁÁÁÁÁÁÁÁÁÁÁÁÁ
ÁÁÁÁÁÁÁÁÁÁÁÁÁÁÁÁÁÁÁÁÁÁÁÁÁ
ÁÁÁÁÁÁÁÁÁÁÁÁÁÁÁÁÁÁÁÁÁÁÁÁÁ
Basic Model
Series
ÁÁÁÁÁÁ
ÁÁÁÁÁÁ
ÁÁÁÁÁÁ
Compression
Ring
ÁÁÁÁÁ
ÁÁÁÁÁ
ÁÁÁÁÁ
Oil
Ring
ÁÁÁÁÁÁÁÁÁÁÁÁÁÁÁÁÁÁÁÁÁÁÁÁÁ
ÁÁÁÁÁÁÁÁÁÁÁÁÁÁÁÁÁÁÁÁÁÁÁÁÁ
ÁÁÁÁÁÁÁÁÁÁÁÁÁÁÁÁÁÁÁÁÁÁÁÁÁ
401400, 401700, 421400, 421700
ÁÁÁÁÁÁ
ÁÁÁÁÁÁ
ÁÁÁÁÁÁ
.035”
(.89 mm)
ÁÁÁÁÁ
ÁÁÁÁÁ
ÁÁÁÁÁ
.045”
(1.14 mm)
ÁÁÁÁÁÁÁÁÁÁÁÁÁÁÁÁÁÁÁÁÁÁÁÁÁ
ÁÁÁÁÁÁÁÁÁÁÁÁÁÁÁÁÁÁÁÁÁÁÁÁÁ
ÁÁÁÁÁÁÁÁÁÁÁÁÁÁÁÁÁÁÁÁÁÁÁÁÁ
400400, 400440, 400700, 400770, 402400, 402440, 402700, 402770, 404400,
404440, 404700, 404770, 422400, 422440, 422700, 422770, 462700
ÁÁÁÁÁÁ
ÁÁÁÁÁÁ
ÁÁÁÁÁÁ
.030”
(.76 mm)
ÁÁÁÁÁ
ÁÁÁÁÁ
ÁÁÁÁÁ
.035”
(.89 mm)
NOTE: If new piston rings are going to be installed in a cylinder that is within specification, the cylinder bore should
be reconditioned, using a rigid hone with finishing stones, to restore the proper cross hatch angle in the
cylinder bores. The proper cylinder cross hatch ensures proper lubrication and piston ring rotation. See
Section 11, Cylinder Finish (Cross Hatch), for procedure for applying cross hatch to cylinder bore.
Check Piston Pin and Piston Pin Bore
If piston pin is worn .0005” (.01 mm) out of round or
below reject sizes shown in Table No. 2, it should be
replaced. If piston pin bore Fig. 6 is worn above reject
sizes, Table No. 2, oversize piston pin .005” (.13 mm) is
available. See Illustrated Parts List.
Fig. 6 – Checking Piston Pin Bore
PISTON
PIN
BORE
Piston Pin & Piston Pin Bore Reject Sizes
ÁÁÁÁÁÁÁ
ÁÁÁÁÁÁÁ
ÁÁÁÁÁÁÁ
Model Series
ÁÁÁÁÁÁ
ÁÁÁÁÁÁ
ÁÁÁÁÁÁ
Piston Pin
ÁÁÁÁÁ
ÁÁÁÁÁ
ÁÁÁÁÁ
Piston Pin
Bore
ÁÁÁÁÁÁÁ
ÁÁÁÁÁÁÁ
ÁÁÁÁÁÁÁ
ALL MODELS
ÁÁÁÁÁÁ
ÁÁÁÁÁÁ
ÁÁÁÁÁÁ
.799”
(20.29 mm)
ÁÁÁÁÁ
ÁÁÁÁÁ
ÁÁÁÁÁ
.802”
(20.37 mm)
Fig. 7 – Check Piston Pin
Содержание Twin Cylinder L-Head
Страница 1: ...For Briggs Stratton Discount Parts Call 606 678 9623 or 606 561 4983 www mymowerparts com ...
Страница 55: ......
Страница 129: ......
Страница 151: ......
Страница 163: ......