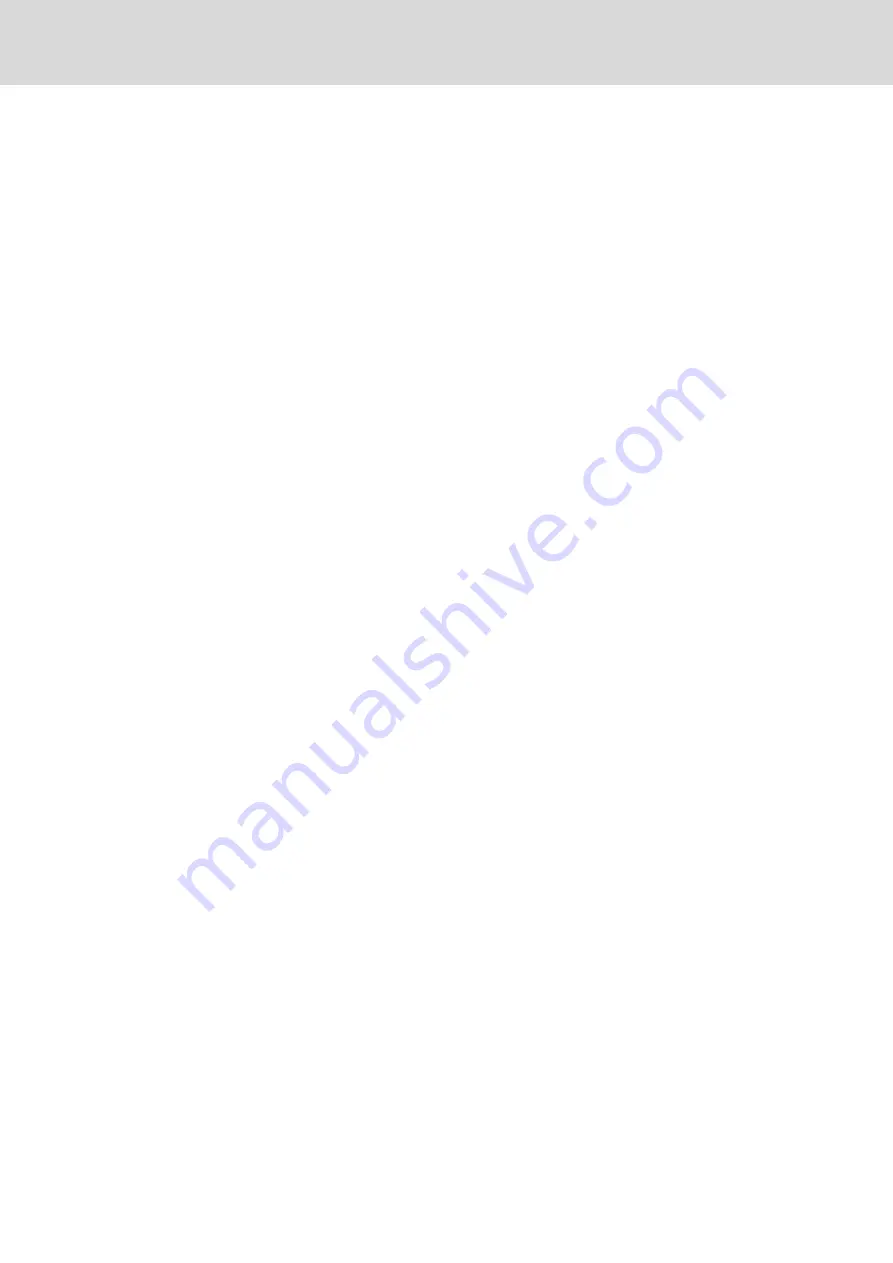
you can establish the contact to varnished surfaces by using tooth lock wash‐
ers.
Metal surfaces
Always use connection elements (screws, nuts, plain washers) with a highly
conductive surface.
Highly conductive surfaces are those with bare, zinc-coated or tinned metal
surfaces.
Poorly conductive surfaces are those with anodized, yellow chromatized,
black gunmetal finished or lacquered metal surfaces.
Ground wires and shield connec‐
tions
When connecting ground wires and shield connections, what is important is
not the cross section of the wire, but the area of the contact surface, since
high-frequency interference currents mainly flow on the surface of the con‐
ductor.
Always connect cable shields, especially shields for the motor power cables,
to ground potential over a large surface area.
Installing signal lines and signal cables
Line routing
For measures to prevent interference, see the Project Planning Manuals for
each device. We also recommend the following:
●
Route signal and control lines away from power cables at a minimum
distance of d5 = 100 mm (see
Division into areas (zones), page 172
) or
with a grounded separating sheet. The best way is to route them in sep‐
arate cable ducts. If possible, only route signal lines into the control cab‐
inet at one point.
●
If signal lines cross power cables, route them at an angle of 90° in order
to avoid interference injection.
●
Ground unused and connected spare cables at both ends at least in or‐
der to avoid an antenna effect.
●
Do not use more line than is necessary.
●
Run cables as close to grounded metal surfaces as possible (reference
potential). Closed, grounded cable ducts or metal pipes are ideal, but
are only needed to meet strict requirements (sensitive instrument leads).
●
Avoid suspended lines or lines routed along synthetic carriers, because
they function like reception antennas (noise immunity) and transmitting
antennas (emission of interference). Exceptional cases are flexible ca‐
ble tracks over short distances of at most 5 m.
Shielding
Connect the cable shield immediately at the devices in the shortest and most
direct way possible and over the largest possible surface area.
Connect the shield of analog signal lines at one end over a large surface
area, normally in the control cabinet at the analog device. Make sure the con‐
nection to ground/housing is short and over a large surface area.
Connect the shield of digital signal lines at both ends over a large surface
area and in short form. In case of potential differences between line begin‐
ning and end, run an additional bonding conductor in parallel. This prevents
compensating current from flowing via the shield. The recommended cross
section is 10 mm
2
.
Separable connections absolutely must be equipped with connectors that
have a grounded metal housing.
In case of unshielded lines belonging to the same circuit, twist feeder and re‐
turn cable.
DOK-INDRV*-HCS01******-PR05-EN-P
Bosch Rexroth AG
179/341
Rexroth IndraDrive CsDrive Systems with HCS01
Mounting and installation
Содержание Rexroth IndraDrive CsDrive System with HCS01
Страница 1: ...Rexroth IndraDrive Cs Drive Systems with HCS01 Project Planning Manual R911322210 Edition 05 ...
Страница 30: ...Bosch Rexroth AG DOK INDRV HCS01 PR05 EN P 28 341 Rexroth IndraDrive CsDrive Systems with HCS01 ...
Страница 250: ...Bosch Rexroth AG DOK INDRV HCS01 PR05 EN P 248 341 Rexroth IndraDrive CsDrive Systems with HCS01 ...
Страница 314: ...Bosch Rexroth AG DOK INDRV HCS01 PR05 EN P 312 341 Rexroth IndraDrive CsDrive Systems with HCS01 ...
Страница 318: ...Bosch Rexroth AG DOK INDRV HCS01 PR05 EN P 316 341 Rexroth IndraDrive CsDrive Systems with HCS01 ...
Страница 332: ...Bosch Rexroth AG DOK INDRV HCS01 PR05 EN P 330 341 Rexroth IndraDrive CsDrive Systems with HCS01 ...
Страница 342: ...Notes Bosch Rexroth AG DOK INDRV HCS01 PR05 EN P 340 341 Rexroth IndraDrive CsDrive Systems with HCS01 ...
Страница 343: ...Notes DOK INDRV HCS01 PR05 EN P Bosch Rexroth AG 341 341 Rexroth IndraDrive CsDrive Systems with HCS01 ...