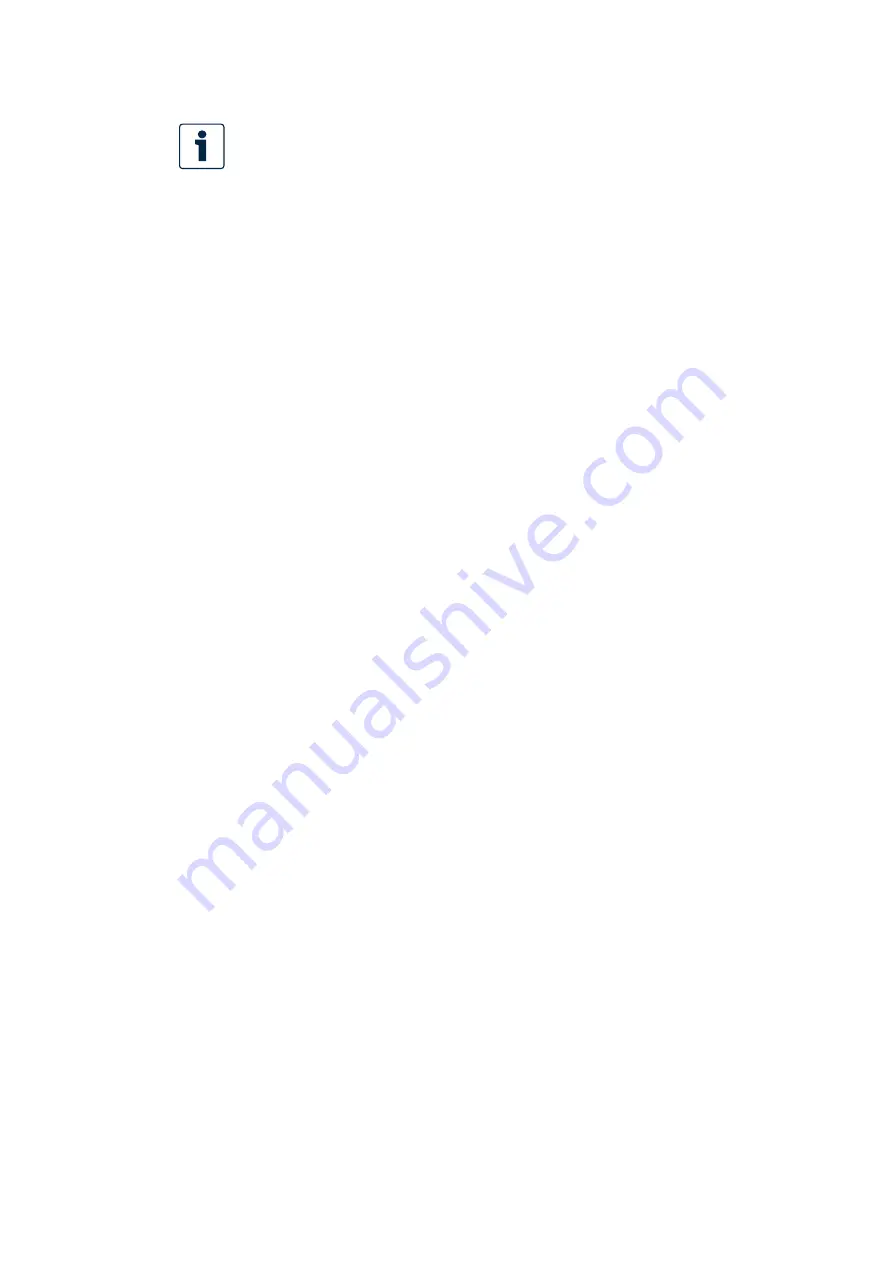
34
/104
A4... with HS5E(V)(L) control system Series 1x and 30
| About this product
Bosch Rexroth AG, RE 92076-01-B/2021-04-22
Notes
:
– For the configuration of analog command value specification, see the
HydraulicDrive functional description (see data sheet 30338).
– The port for the pump's position transducer is not drawn in.
– As an option, you can install the coupling element (relay, analog switch) to
regulate both pumps independently from one another. With the slave pump, this
means that it is possible in the suggestion shown here to carry out both swivel
angle and pressure control.
– For "master/slave" operating mode, signal p
set
(II) must be switched to the
maximum (+10 V).
– If closed-loop pressure control is to be realized also in the "master/slave"
operating mode, only the pressure transducer of the master is evaluated
for controlling purposes. If you also want to run in hydraulically separated
operation, a separate pressure transducer is required for the slave.
– You must parameterize the slave pumps as slaves in the configuration of the
HS5E pilot control valve.
– If there is no special circuitry of the signal branch of the slave pump’s pressure
transducer, its pressure controller intervenes in an undesirable way in swivel
angle control when the actual pressure value p
actual
(II) reaches values in the
range from about 80% of the command value p
set
(II) onward. You can avoid this
by switching a 0 V signal on pin 10 instead of the pressure transducer output
signal via a second channel of coupling element "K1" in "master/slave" mode.
Make sure that the P and D controller parameters on the slave are not set higher
than on the master. Slave units can be calibrated by means of the corresponding
calibration cycle.
5.7.1.1 Switching over to (analog) master/slave mode
The 0 V reference potential of the PLC/command value source and M0/L0 of the
HS5E pilot control valve must be connected.
At low working pressure, the system uses a change-over contact that is suitable for
extra-low signal voltages (or, as an alternative, a non-wearing analog switch) to
disconnect the swivel angle command value of the slave pump that previously came
from the control and to connect the swivel angle actual value coming from the HS5E
pilot control valve of the master pump.
The pressure command value of the slave pump is set to 100% (possibly by means
of a second change-over contact or in software) so that the pressure control virtually
switches off this unit.
▶ Actuate both pumps shortly
before
switching over to pressure control (low, equal
pressure level), still hydraulically decoupled from one another. Here, the optimum
situation would be if the swivel angle actual values were approximately the same.
The two flow command values (generally 100%) come from the control.
All of the analog inputs that are not used, e.g. the actual pressure value input in the
case of swivel angle control, must be interconnected with 0 Volts.
Notwithstanding, unused differential amplifier inputs can also be short-circuited.
Starting point
Switching over to master/
slave operation
Switching off master/slave
operation
Connection of unused,
electrical signal inputs