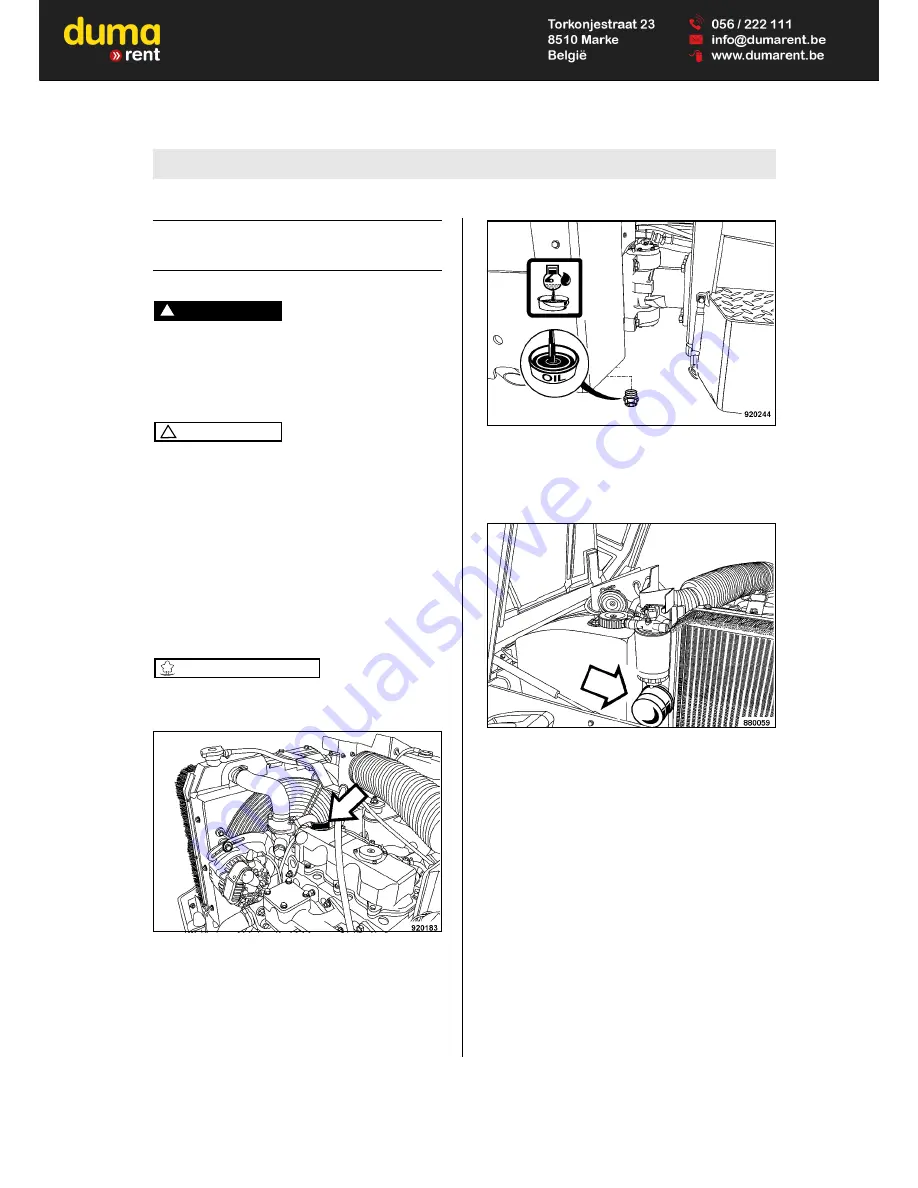
Every 250 operating hours
BOMAG
89
BW 100/120/125 AD-4/AC-4
Every 250 oper ating hours
6.17 Changing engine oil and oil
filter
Danger
!
Danger of scalding!
When draining off hot oil.
By hot oil when unscrewing the engine oil fil-
ter.
Caution
!
The oil change at 250 operating hours refers to
the use of oils of oil quality class API CF, CF-4,
CG-4, CH-4 or CI-4 and a fuel sulphur content
of less than 0.5%.
When using fuels with a sulphur content high-
er than 0.5% the oil change intervals must be
halved.
Drain the engine oil only when the engine is
warm.
For quality and quantity of oil refer to the "table
of fuels and lubricants".
Environment
Catch running out oil and dispose of environ-
mentally together with the oil filter cartridge.
Fig. 133
l
Unscrew the oil filler plug (Fig. 133).
Fig. 134
l
Unscrew the drain plug (Fig. 134) and catch
running out oil.
l
Turn the drain plug tightly back in.
Fig. 135
l
Unscrew the filter cartridge (Fig. 135) using an
appropriate filter wrench.
l
Clean the sealing face on the filter carrier from
any dirt.
Содержание BW 100 AC-4
Страница 2: ......
Страница 8: ...Table of Contents BOMAG 8 BW 100 120 125 AD 4 AC 4...
Страница 9: ...BOMAG 9 BW 100 120 125 AD 4 AC 4 2 Technical Data...
Страница 14: ...Technical Data BOMAG 14 BW 100 120 125 AD 4 AC 4 1 Subject to technical alterations...
Страница 16: ...Technical Data BOMAG 16 BW 100 120 125 AD 4 AC 4...
Страница 17: ...BOMAG 17 BW 100 120 125 AD 4 AC 4 3 Safety regulations...
Страница 30: ...Safety regulations BOMAG 30 BW 100 120 125 AD 4 AC 4...
Страница 31: ...BOMAG 31 BW 100 120 125 AD 4 AC 4 4 Indicators and Controls...
Страница 32: ...Indicators and Controls BOMAG 32 BW 100 120 125 AD 4 AC 4 Fig 20...
Страница 44: ...Indicators and Controls BOMAG 44 BW 100 120 125 AD 4 AC 4...
Страница 45: ...BOMAG 45 BW 100 120 125 AD 4 AC 4 5 Operation...
Страница 71: ...BOMAG 71 BW 100 120 125 AD 4 AC 4 6 Maintenance...
Страница 80: ...Maintenance BOMAG 80 BW 100 120 125 AD 4 AC 4...
Страница 88: ...Every 50 operating hours BOMAG 88 BW 100 120 125 AD 4 AC 4...
Страница 98: ...Every 250 operating hours BOMAG 98 BW 100 120 125 AD 4 AC 4...
Страница 102: ...Every 500 operating hours BOMAG 102 BW 100 120 125 AD 4 AC 4...
Страница 110: ...Every 2000 operating hours BOMAG 110 BW 100 120 125 AD 4 AC 4...
Страница 112: ...Every 3000 operating hours BOMAG 112 BW 100 120 125 AD 4 AC 4...
Страница 118: ...As required BOMAG 118 BW 100 120 125 AD 4 AC 4...
Страница 119: ...BOMAG 119 BW 100 120 125 AD 4 AC 4 7 Trouble shooting...
Страница 123: ...BOMAG 123 BW 100 120 125 AD 4 AC 4 8 Disposal...
Страница 125: ......
Страница 126: ...Powered by TCPDF www tcpdf org...