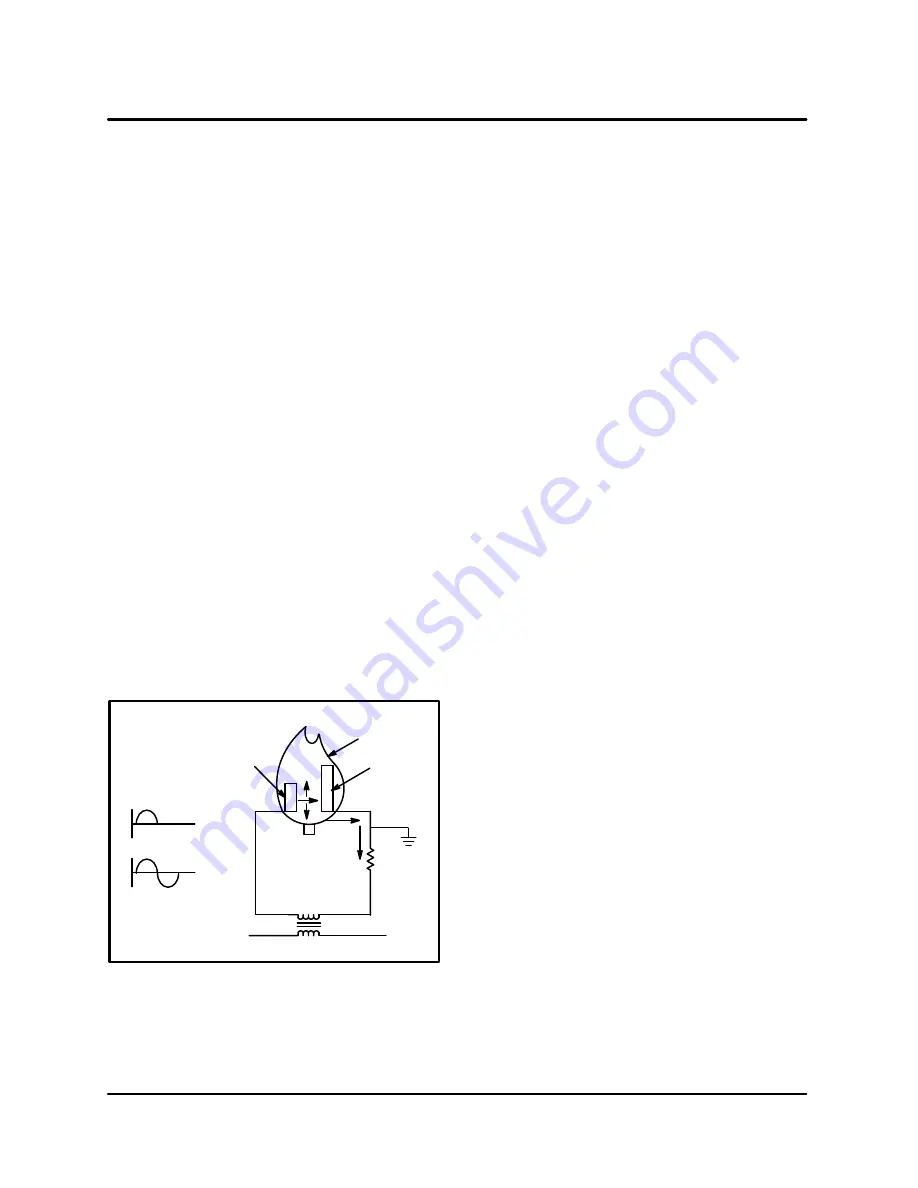
MT2136
6-1
INTERMITTENT IGNITION SYSTEM
PRINCIPLES OF OPERATION
Pilot flame sensing is a very important aspect of the
ignition controls operation. Three zones are needĆ
ed to give the proper airĆgas ratio to produce a blue
pilot flame.
Zone 1
- an inner cone that will not burn because
excess fuel is present.
Zone 2
- around the inner, fuel rich cone is a blue
envelope. This zone contains a mixture of vapor
from the fuel rich inner cone and the secondary or
surrounding air. This is where combustion occurs,
and is the area of highest importance for proper
flame sensor location.
Zone 3
- Outside the blue envelope is third zone
that contains an excessive quantity of air.
FLAME RECTIFICATION
To identify a current conducted by the flame, we
use flame rectification. Place two probes in Zone 2
of the pilot flame. When the surface area of one
probe is larger than the other, current tends to flow
more in one direction. DC current flows in only one
direction, as opposed to AC current, which alterĆ
nates its direction. The current is rectified from AC
to DC by increasing the surface area of one probe
and decreasing the surface area of the other.
+
-
AC Voltage
Transformer
Ground
DC
Current
DC
Current
Flame
Negative
Probe
Positive
Probe
+
DC
Current
+
AC
Voltage
-
FIGURE 1
In the IID system the probes exposed to the pilot
flame are the Flame Sensor and the Pilot Burner
Hood. Since the surface area of the pilot hood is
larger than the flame sensor, the current rectificaĆ
tion process takes place. Current is conducted
from terminal 4 at the control through the flame
sensor cable to the flame sensor. As the current is
conducted through the flame to the pilot hood, it is
rectified from AC to DC because of the difference
in surface area. The pilot hood is grounded back
to the control, thereby completing the circuit.
Flame Sensing Circuit Current
For the ignition control to function properly, a miniĆ
mum amount of current must flow through the
flame sensing circuit.
As the pilot flame is established and current begins
to flow in the flame sensing circuit, the current enĆ
ergizes a relay. A minimum amount of current is reĆ
quired to pullĆin the relay. When the relay pulls in,
one set of contacts opens which shuts off the high
energy spark. Another set of contacts closes, puttĆ
ing 24 volts on terminal 3 which opens the main
gas valve.
Current vs. Voltage
In normal operation an AC voltage will be present
from terminal 4 to ground and a current will be
present in the flame sensing circuit.
Even though an AC voltage is present, flame rectifiĆ
cation occurs and a DC current flows in the sensing
circuit.
For service checkout purposes, measuring these
voltages and currents can provide useful informaĆ
tion regarding the integrity of the ignition control.
Measuring the current flow rather than voltage is
the preferred procedure. Due to the internal circuitĆ
ry of the ignition control and varying input impedĆ
ance of voltmeters, the measured voltage will vary
depending on type and model of voltmeter being
used. However, measuring the current provides a
more precise evaluation of the ignition control and
flame sensing circuit.
A proper reading not only indicates a functional
control, but also verifies all components of the cirĆ
cuit such as flame sensor, cable and ground.
Содержание MT2136 Series
Страница 4: ...INTRODUCTION CHAPTER 1 ...
Страница 15: ...MT2136 1 11 35 30 35 29 39 28 38 33 34 31 37 36 26 27 32 EXTERIOR COMPONENTS FIGURE 3 ...
Страница 17: ...MT2136 1 13 CE GAS BURNER COMPONENTS Control Box not Shown 16 17 FIGURE 5 ...
Страница 18: ...INTRODUCTION 1 14 CONTROL PLATE ASSEMBLY 18 25 16 26 21 19 20 24 23 22 EXCLUSIVE TO CE 40 41 42 43 FIGURE 6 ...
Страница 19: ...MT2136 1 15 This page intentionally left blank ...
Страница 20: ...ASSEMBLY CHAPTER 2 ...
Страница 23: ...MT2136 2 3 This page intentionally left blank ...
Страница 24: ...OPERATION CHAPTER 3 ...
Страница 49: ...MT2136 3 25 16 17 18 19 20 21 12 13 13 13 4 7 15 3 2 1 14 8 9 10 6 11 5 5 FIGURE 4 ...
Страница 50: ...OPERATION 3 26 16 17 20 19 18 15 3 12 13 13 13 4 14 7 1 2 8 9 10 6 11 5 5 FIGURE 5 ...
Страница 51: ...MT2136 3 27 22 23 24 25 26 21 19 18 18 18 4 7 1 3 2 20 5 5 11 12 13 14 15 16 8 17 6 9 10 FIGURE 6 ...
Страница 52: ...OPERATION 3 28 25 26 27 29 28 2 24 23 22 21 21 21 3 1 7 20 4 16 17 18 19 14 15 8 10 6 11 12 13 9 5 5 FIGURE 7 ...
Страница 53: ...MT2136 3 29 1 17 3 2 4 16 16 16 15 21 5 13 14 14 10 18 19 6 7 8 20 9 12 11 FIGURE 8 ...
Страница 54: ...OPERATION 3 30 1 18 16 16 16 16 17 15 22 5 3 2 4 13 10 19 20 6 7 8 21 9 12 11 14 14 FIGURE 9 ...
Страница 55: ...MT2136 3 31 1 21 21 21 17 16 22 18 20 19 14 3 2 4 11 6 13 12 15 10 7 8 9 5 FIGURE 10 ...
Страница 56: ...OPERATION 3 32 1 8 8 8 8 6 7 16 15 17 18 3 2 4 11 5 9 9 12 13 14 FIGURE 11 ...
Страница 57: ...MT2136 3 33 1 6 9 8 19 22 21 7 16 17 2 3 4 18 5 10 14 20 12 11 13 15 25 25 25 24 FIGURE 12 ...
Страница 58: ...OPERATION 3 34 1 FIGURE 13 ...
Страница 60: ...CALIBRATION AND ADJUSTMENT CHAPTER 4 ...
Страница 77: ...MT2136 4 17 This page intentionally left blank ...
Страница 78: ...TROUBLESHOOTING CHAPTER 5 ...
Страница 86: ...TECHNICAL APPENDIX CHAPTER 6 ...