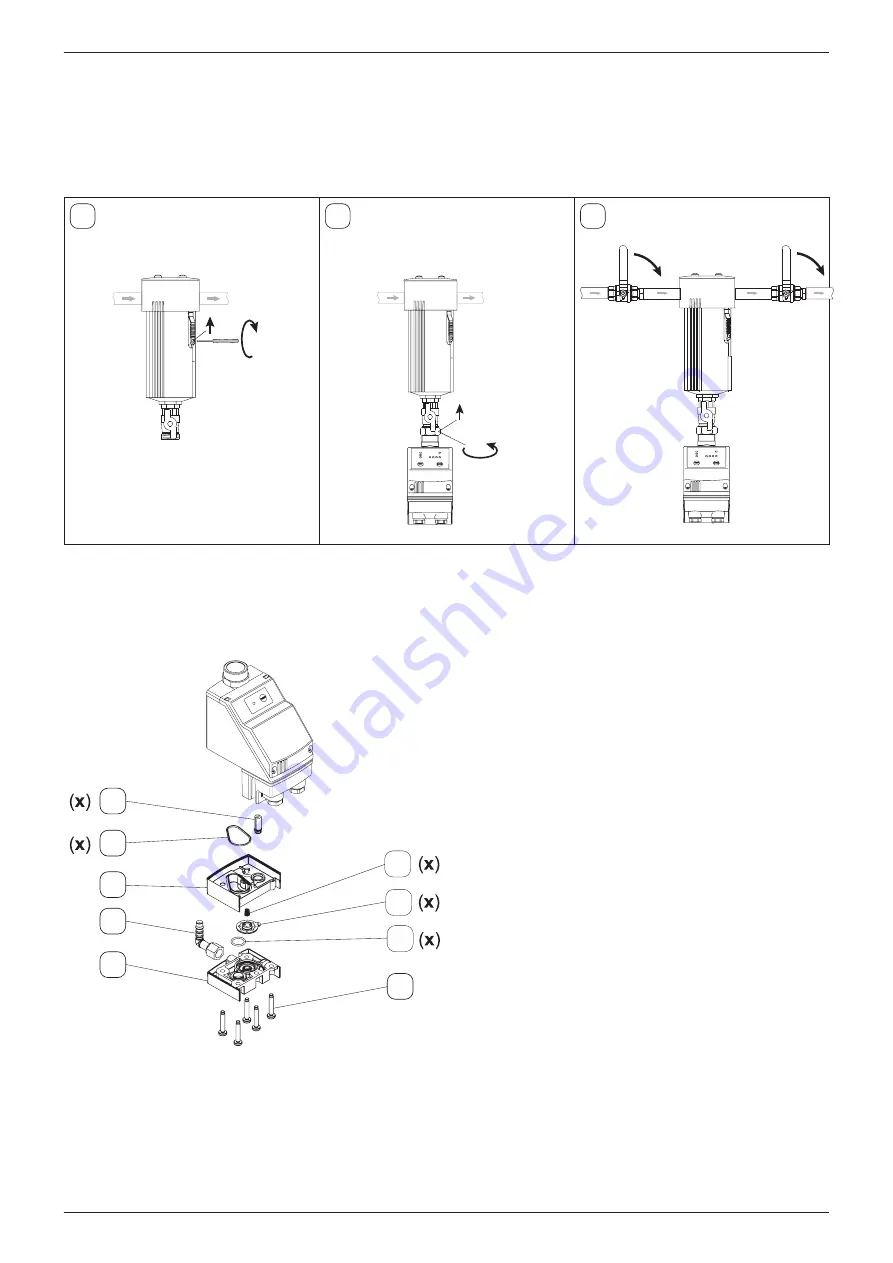
EN
Installation and operating manual
DRYPOINT
®
AC 410 – 495 | DRYPOINT
®
AC 410 – 495 MS
39
9. Lock the slider and tighten the screw.
10. Mount the BEKOMAT
®
.
11. Slowly pressurise the filter by carefully opening the shut-off valves.
Note down the next filter element change date in the maintenance schedule and on the supplied adhesive label.
Apply the label to the filter housing body in a position where it is clearly visible. Check your stock and order new
elements, if necessary.
9
10
11
2
1
1
2
1
2
7.4. Maintenance of BEKOMAT
®
20 FM condensate drain
Preparation:
• Depressurise the BEKOMAT
®
!
• De-energize the BEKOMAT
®
!
28
29
30
1
12
9
13
14
15
Maintenance recommendation:
• Unscrew the elbow connector (14).
•
Open the inlet side fitting of the
BEKOMAT
®
.
• Loosen the 5 TORX screws (1) and
remove the parts (9, 12 - 15 and 28 - 30).
• Caution: Do not remove the core guide
pipe.
• Clean the parts.
• Replace the wearing parts (x).
• Reassemble and install the BEKOMAT
®
.
Содержание DRYPOINT AC 410
Страница 2: ...Installation and operating manual EN 2 DRYPOINT AC 410 495 DRYPOINT AC 410 495 MS ...
Страница 52: ...Installation and operating manual EN 52 DRYPOINT AC 410 495 DRYPOINT AC 410 495 MS ...
Страница 55: ...EN Installation and operating manual DRYPOINT AC 410 495 DRYPOINT AC 410 495 MS 55 ...