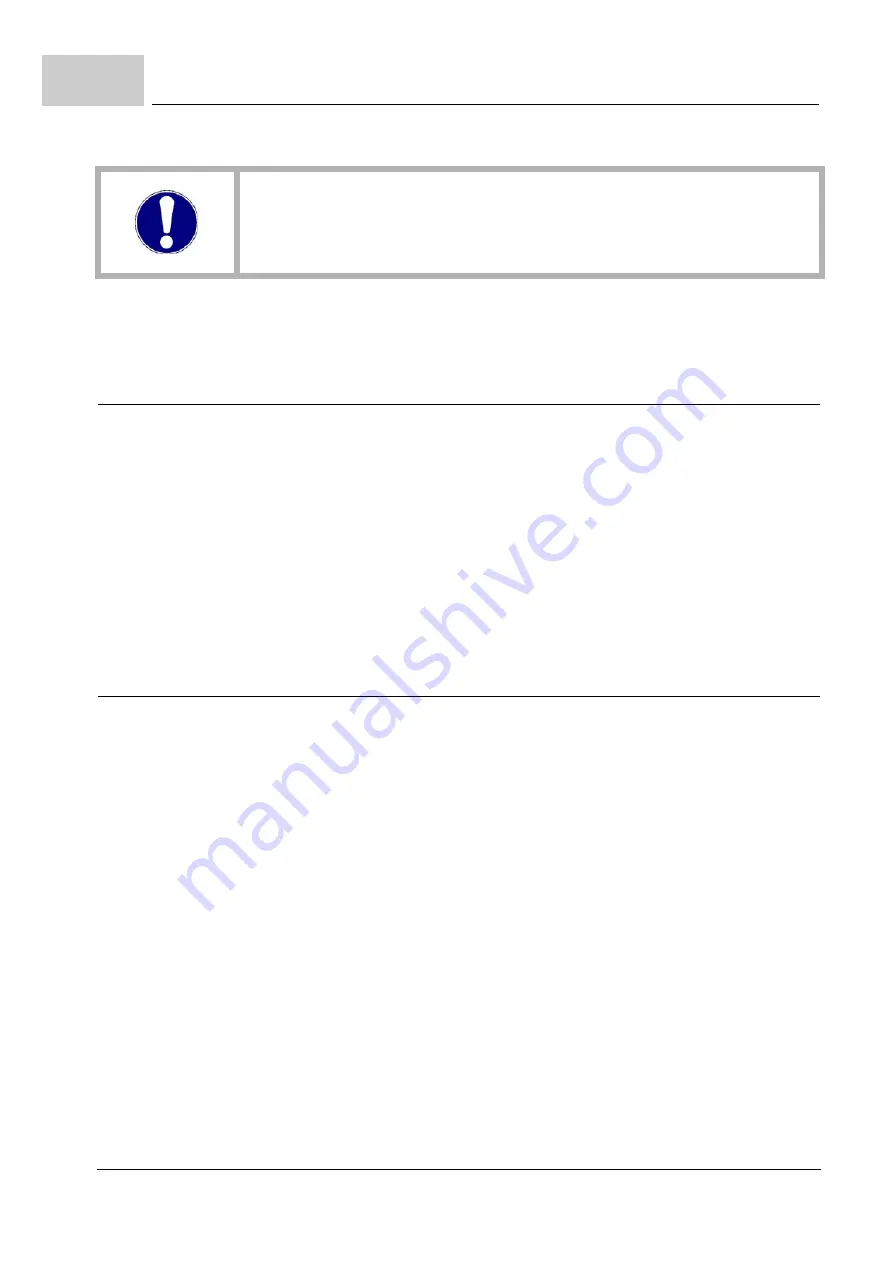
Description of the operation modes, RUN/STOP switch
Operation Manual
b maXX safe PLC
BMC-M-SAF-02
Document no.: 5.07020.04
Baumüller Nürnberg GmbH
60
11.1
Please take note of
Troubleshooting and rectification
rectifying errors during the commissioning process.
11.1 Description of the operation modes, RUN/STOP switch
Due to the run-time system implemented, the safety system consists of two function units,
namely the standard PLC and the safety PLC.
The IEC application program is run on the standard PLC. The programming is carried out
in ProProg with the full extent of IEC languages. The standard motion control function is
also available.
The safe IEC application program is run on the safety PLC. The programming is carried
out in ProSafety in function diagram/ladder diagram. The standard motion control function
is also available.
The configuration for both function units is conducted in ProMaster (see
>
Application
Manual b maXX safe PLC
<
). There are the following two operation modes for the safety
control in relation to the function units.
11.1.1 Solitary safety PLC
If the functions of the standard PLC are not needed, then the safety PLC can be run by
itself. This way, it puts the full scope of functions of a conventional safety control at your
disposal.
The operation mode is set when an IEC project is not transferred to the standard PLC or
when an existing project is erased. The safe parameter for the distribution of computing
time between safety PLC and standard PC should be set on 90% for this operation mode
(see
Determination of the device parameters
Running the safety PLC in solitary operation will result in the following behavior:
Safety IEC projects including configuration files can be transferred to the safety PLC. The
bus configurations must be transferred to the standard PLC, by downloading in ProMas-
ter, for example (see
>
Application Handbook b maXX safe PLC
<
).
The safety PLC can be started and stopped using the RUN/STOP switch (see
switch/button for changing operating statuses of the BMC-M-SAF-02
onward), or using debug operation in ProSafety. If the safety PLC is supposed to start up
after being turned on, a project must be present and the RUN/STOP switch must be in
the “RUN” position.
If a new bus configuration is loaded on the standard PLC, the safe communication will be
interrupted by the idleness of the standard communication, after that it will start back up
again. If there are dependencies on the standard communication, then additional slaves
CAUTION!
Adjusting the safe cycle time is only permissible if the reaction times established in
the planning phase are complied with. In this case, computational evidence will have
to be provided.
Содержание b maXX BMC-M-SAF-02
Страница 8: ...Operation Manual b maXX safe PLC BMC M SAF 02 Document no 5 07020 04 Baumüller Nürnberg GmbH 8 of 118 ...
Страница 16: ...Operation Manual b maXX safe PLC BMC M SAF 02 Document no 5 07020 04 Baumüller Nürnberg GmbH 16 of 118 ...
Страница 58: ...Operation Manual b maXX safe PLC BMC M SAF 02 Document no 5 07020 04 Baumüller Nürnberg GmbH 58 of 118 ...
Страница 82: ...Operation Manual b maXX safe PLC BMC M SAF 02 Document no 5 07020 04 Baumüller Nürnberg GmbH 82 of 118 ...
Страница 90: ...Operation Manual b maXX safe PLC BMC M SAF 02 Document no 5 07020 04 Baumüller Nürnberg GmbH 90 of 118 ...
Страница 92: ...Operation Manual b maXX safe PLC BMC M SAF 02 Document no 5 07020 04 Baumüller Nürnberg GmbH 92 of 118 ...
Страница 100: ...Operation Manual b maXX safe PLC BMC M SAF 02 Document no 5 07020 04 Baumüller Nürnberg GmbH 100 of 118 A ...
Страница 119: ......