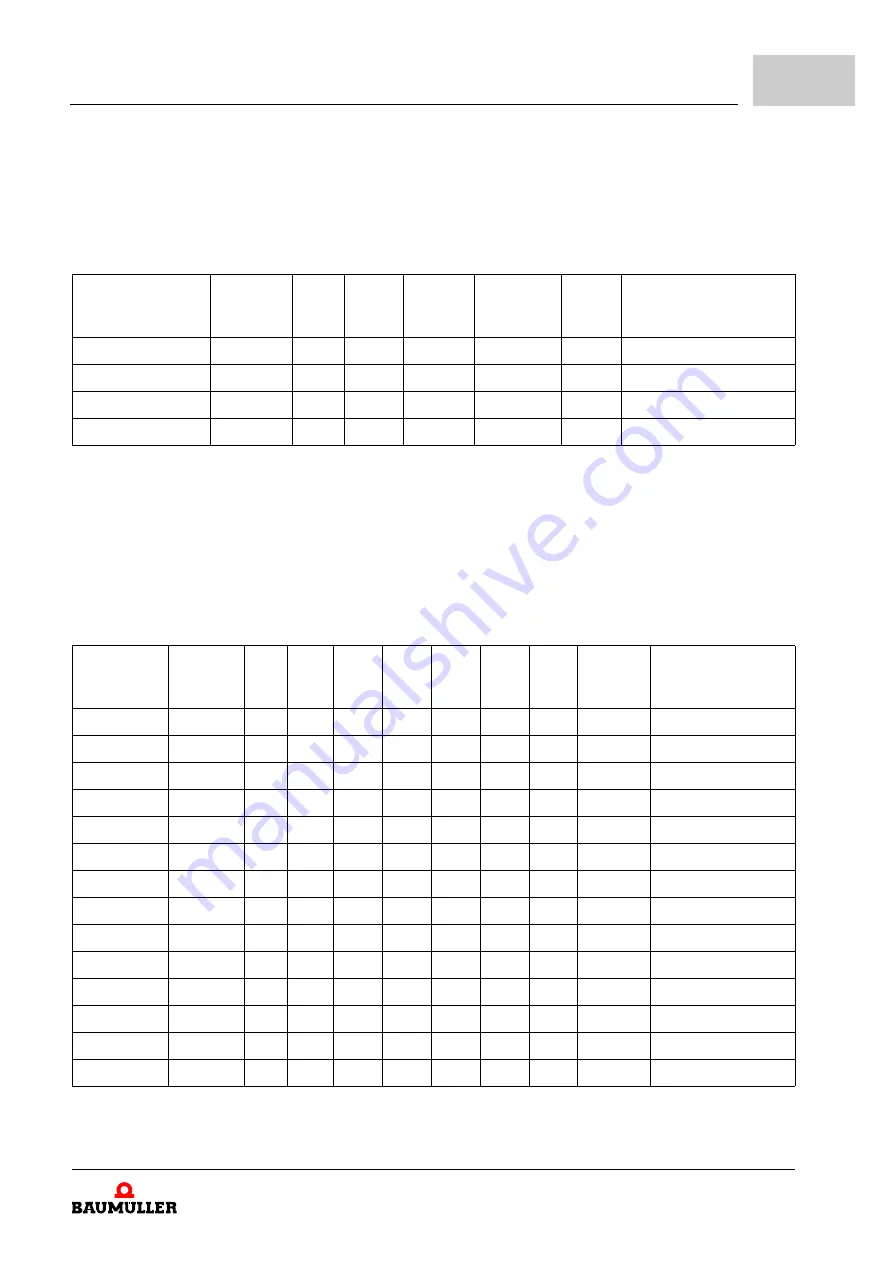
Accessories and spare parts
Instruction handbook
b maXX
5000
Document No.: 5.09021.16
277
11
Electrical data
Rated voltage max. 550 V, rated frequency 50/60 Hz, flat connector, IP 00,
rated voltage 400 V, u
K
= 4% (50 Hz) / 4.8% (60 Hz),
operating temperature for I
AC
up to 80 A up to 45 °C and for I
AC
over 80 A up to 40 °C,
with a derating of the current by 1% per °C up to 55 °C.
Power choke
Part No.
I
AC
[A]
I
DC
[A]
L
[mH]
Power
loss
[W]
Weight
[kg]
Use in operation at
rated power
1)
BK3-0025/0030
368377
25
30
1.18
65
6
BM5030, BM5031
BK3-0040/0050
368378
40
50
0.72
79
7
BM5032
BK3-0080/0100
368380
80
100
0.36
134
12
BM5043
BK3-0165/0200
368382
165
200
0.18
192
23
BM5044
1)
With minimal output in continuous operation, chokes with lower rated currents are also usable. Chokes with larger rated currents are
necessary for cyclical utilization of the overload capacity of the devices. If overcurrent is only needed momentarily and non-recurringly
(once per hour, for a maximum of 60 s), then the chokes suggested for operation at the rated power are also sufficient.
UL approval
The chokes are design-tested in accordance with UL (e.g. UL1561) and signified by the
„
ú“
“ symbol.
Dimensions
BK3-
Part No.
I
AC
[A]
I
DC
[A]
a
[mm]
b
[mm]
c
[mm]
d
[mm]
e
[mm]
f
g
[mm]
Flat connector
Cu terminals
[mm
mm]
0025/0030
368377
25
30
155
130
132
130
72
8
12
20
2 for M6
0040/0050
368378
41
50
190
120
158
170
58
8
12
20
2 for M6
0065/0080
368379
66
80
190
140
158
170
78
8
12
20
2 for M6
0080/0100
368380
82
100
230
165
202
180
98
8
12
25
3 for M8
0115/0140
368381
115
140
230
190
202
180
122
8
12
25
3 for M10
0165/0200
368382
164
200
240
195
211
190
125
11
15
25
3 for M10
0195/0240
368383
197
240
265
195
230
215
126
11
15
25
3 for M10
0275/0340
368384
297
340
300
225
271
240
145
11
15
30
5 for M10
0365/0450
368385
369
450
360
220
320
310
125
11
15
40
5 for M10
0450/0550
368386
451
550
360
260
320
310
140
11
15
50
5 for M12
0530/0650
368387
533
650
360
260
320
310
140
11
15
50
5 for M12
0615/0750
368388
615
750
420
285
375
370
151
11
15
60
5 for M12
0750/0920
368389
754
920
420
285
375
370
151
11
15
60
5 for M12
0900/1100
368390
902 1100
420
285
380
370
166
11
15
60
10 for M12
Содержание b maXX 5000
Страница 101: ...Design and Operation Instruction handbook b maXX 5000 Document No 5 09021 16 101 of 328 4 ...
Страница 220: ...Fieldbus communication Instruction handbook b maXX 5000 Document No 5 09021 16 Baumüller Nürnberg GmbH 220 of 328 8 4 ...
Страница 240: ...Error handling Instruction handbook b maXX 5000 Document No 5 09021 16 Baumüller Nürnberg GmbH 240 of 328 10 4 ...
Страница 298: ...Instruction handbook b maXX 5000 Document No 5 09021 16 Baumüller Nürnberg GmbH 298 of 328 A ...
Страница 299: ...299 of 328 Operation Manual b maXX 5000 Document no 5 09021 16 APPENDIX B DECLARATION OF CONFORMITY ...
Страница 324: ...Instruction handbook b maXX 5000 Document No 5 09021 16 Baumüller Nürnberg GmbH 324 of 328 Table of Figures ...
Страница 328: ...Instruction handbook b maXX 5000 Document No 5 09021 16 Baumüller Nürnberg GmbH 328 of 328 Notes ...
Страница 329: ......