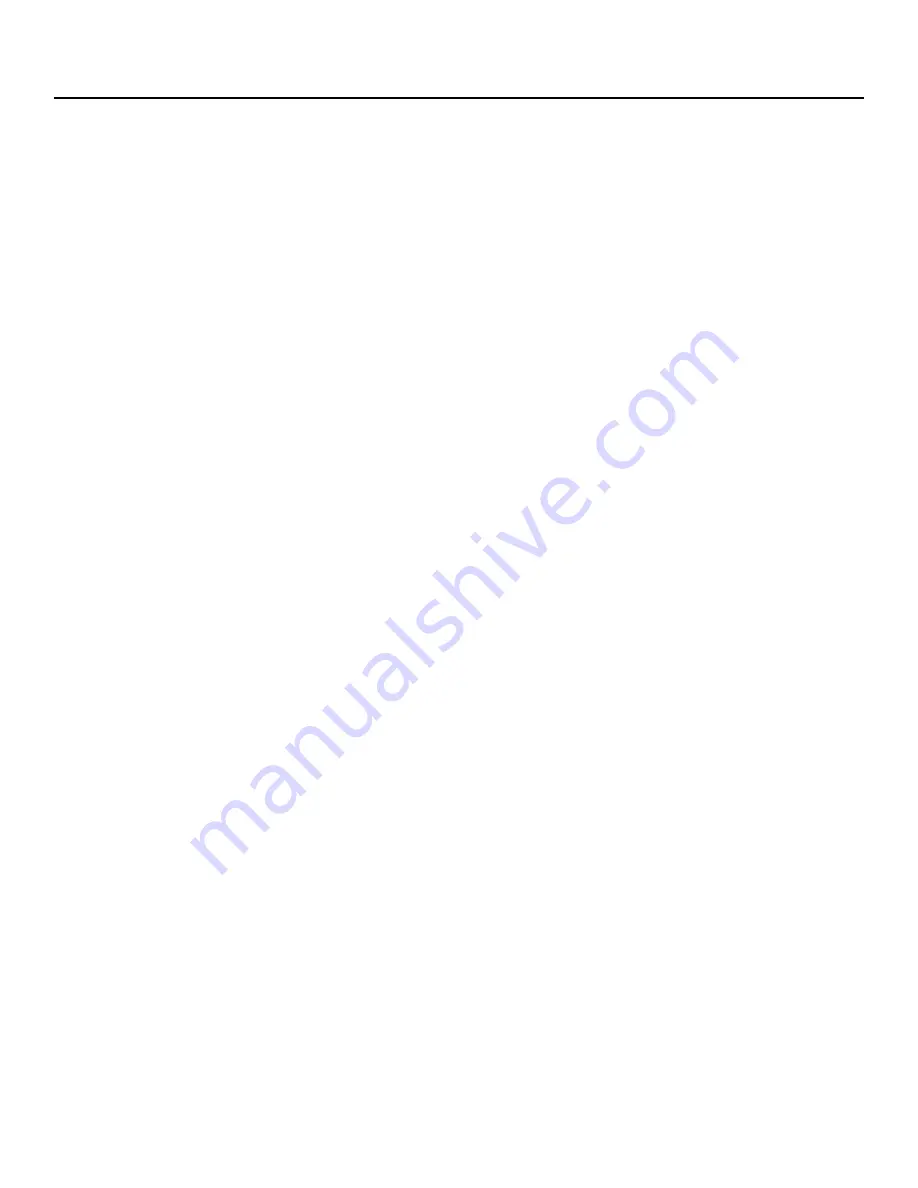
MAN - BBR3 - REV: Original | Appendix D: Image Glossary
49
Appendix D: Image Glossary
Figure A.1 - ATS Sample Data Tag ...........................................................................................................................2
Figure C.1 - Front of BBR3 Unit.................................................................................................................................5
Figure C.2 - Back of BBR3 Unit ................................................................................................................................6
Figure C.3 - Load Frame ...........................................................................................................................................7
Figure C.4 - Tank Interior ..........................................................................................................................................8
Figure C.5 - Gauge Kit ..............................................................................................................................................8
Figure C.6 - Load Frame without Anvil Adapters ......................................................................................................11
Figure C.7 - Load Frame with Anvil Adapters ...........................................................................................................11
Figure C.8 - BBR3 Step Disk ....................................................................................................................................13
Figure C.9 - Internal Controls ....................................................................................................................................14
Figure C.10 - Data Instruments .................................................................................................................................15
Figure C.11 - Basic Unit Controls ..............................................................................................................................16
Figure D.1 - Load frame screw location ....................................................................................................................18
Figure D.2 - Foam Inside Load Shroud .....................................................................................................................18
Figure D.3 - Unscrew the Lower Portion of the Load Shroud ...................................................................................18
Figure D.4 - Set Screw Location on Load Nose ........................................................................................................19
Figure D.5 - Tightening the Set Screw ......................................................................................................................19
Figure D.6 - Upper portion of shroud attached to Load Cell .....................................................................................19
Figure D.7 - Attaching lower portion of Load Shroud ................................................................................................19
Figure D.8 - Attaching lower portion of Load Shroud ................................................................................................19
Figure D.9 - Attached Load Nose with Shroud .........................................................................................................19
Figure D.10 - Connecting the BBR3 ..........................................................................................................................20
Figure D.11 - Load Frame Hook Ups .........................................................................................................................21
Figure D.12 - Chiller Communication Cable in RS-485 Port. ....................................................................................21
Figure D.13 - Chiller Communication Cable in BBR3 Chiller Communication Port. .................................................21
Figure E.1 - BBR3 Software Screen map .................................................................................................................24
Figure E.2 - Main Menu screen .................................................................................................................................25
Figure E.3 - Edit Users dialog ...................................................................................................................................25
Figure E.4 - “Bath Temperature” Field on Setup Screen ..........................................................................................27
Figure E.5 - Standardization Screen .........................................................................................................................27
Figure E.6 - Step disk positioned under locater pin ..................................................................................................29
Figure E.7 - Verification main screen
........................................................................................................................30
Figure E.8 - Confidence beam in place during verification.
......................................................................................31
Figure E.9 - System Verification
................................................................................................................................32
Figure E.10 - Test Setup Main Screen ......................................................................................................................33
Figure E.11 - Add images to test dialog .....................................................................................................................34
Figure E.12 - Standard Report ..................................................................................................................................35