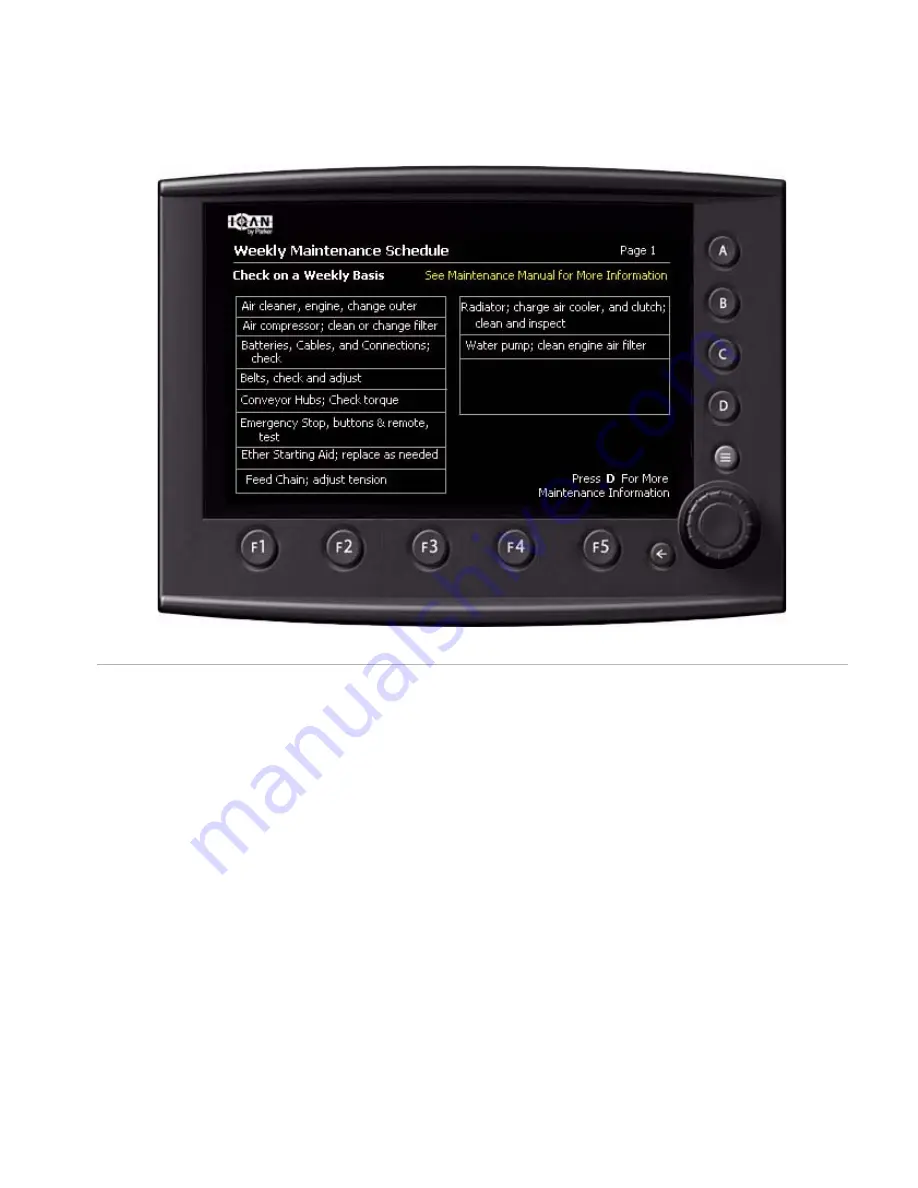
C
H A P T E R
4
D
I S P L A Y I N G
M
A C H I N E
I
N F O R M A T I O N
8 1 7 8 5 C
6 7 0 0 B G
R I N D E R
O
P E R A T O R
S
A F E T Y
M
A N U A L
1 2 7
Weekly Maintenance Schedule
The Weekly Maintenance Schedule (Figure 149) lists
suggested maintenance procedures for your machine.
Use this schedule and your
6700B Maintenance Manual
to properly maintain your machine.
Press
D
for more maintenance information.
Important
The maintenance schedule screens for daily,
weekly, monthly, and other maintenance are pro-
vided for your convenience. They might not include
all recommended service intervals. For a detailed
list of service intervals, refer to “Maintenance
Schedule” in Section 0000, Scheduled Mainte-
nance in the 6700B Maintenance Manual.
F05752
Figure 149: Weekly Maintenance Schedule
Содержание Peterson 6700B
Страница 6: ...C O N T E N T S 4 6 70 0 B G R I N D E R O P E R A T O R S A F E T Y M A N U A L 81785C ...
Страница 10: ...A B O U T TH I S M A N U A L 8 6 70 0 B G R I N D E R O P E R A T O R S A F E T Y M A N U A L 81785C ...
Страница 150: ...I N D E X 14 8 6 70 0 B G R I N D E R O P E R A T O R S A F E T Y M A N U A L 81785C ...
Страница 151: ......
Страница 152: ......