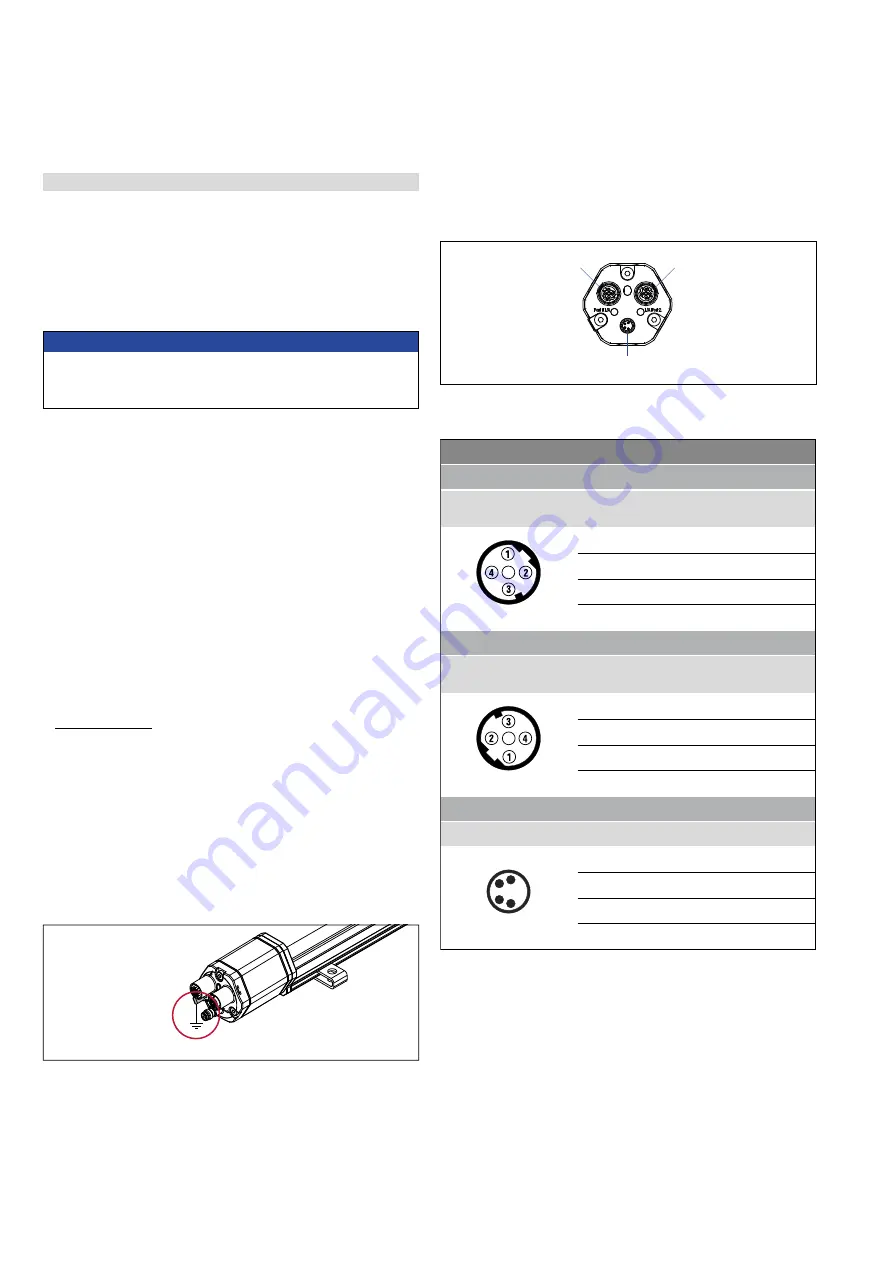
Temposonics
®
R-Series
V
POWERLINK
Operation Manual
I 30 I
4.9 Electrical connection
Placement of installation and cabling have decisive influence on
the sensor‘s electromagnetic compatibility (EMC). Hence correct
installation of this active electronic system and the EMC of the entire
system must be ensured by using suitable metal connectors, shielded
cables and grounding. Overvoltages or faulty connections can damage
its electronics despite protection against wrong polarity.
Instructions for connection
• Use low-resistant twisted pair and shielded cables. Connect
the shield to ground externally via the controller equipment.
• Keep control and signal cables separate from power cables and
sufficiently far away from motor cables, frequency inverters,
valve lines, relays, etc..
• Use only connectors with metal housing and connect the shielding
to the connector housing.
• Keep the connection surface at both shielding ends as large
as possible. Connect the cable clamps to function as a ground.
• Keep all non-shielded leads as short as possible.
• Keep the earth connection as short as possible with a large
cross section. Avoid ground loops.
• With potential differences between machine and electronics earth
connections, no compensating currents are allowed to flow across
the cable shielding.
Recommendation:
Install potential compensating leads with large cross section,
or use cables with separate double shielding, and connect only
one end of the shield.
• Use only stabilized power supplies in compliance with the
specified electrical ratings.
Grounding of profile and rod sensors
Connect the sensor electronics housing to machine ground. Ground
R-Series
V
sensors via ground lug as shown in Fig. 47.
In addition
you can ground the sensor types RH5 and RFV via thread.
Fig. 47: Grounding via ground lug on the example of an RP5 sensor
NOTICE
1. Do not mount the sensors in the area of strong magnetic or
electric noise fields.
2. Never connect/disconnect the sensor when voltage is applied.
Connector wiring
Connect the sensor directly to the control system, indicator or other
evaluating systems as follows:
Fig. 48: Location of connections
MS/ER
NS/RN
Port 2
Port 1
Power supply
D56
Port 1 – Signal
M12 female connector
(D-coded)
Pin
Function
View on sensor
1
Tx (+)
2
Rx (+)
3
Tx (−)
4
Rx (−)
Port 2 – Signal
M12 female connector
(D-coded)
Pin
Function
View on sensor
1
Tx (+)
2
Rx (+)
3
Tx (−)
4
Rx (−)
Power supply
M8 male connector
Pin
Function
2
4
1
3
View on sensor
1
+12…30 VDC (±20 %)
2
Not connected
3
DC Ground (0 V)
4
Not connected
Fig. 49: Connector wiring D56