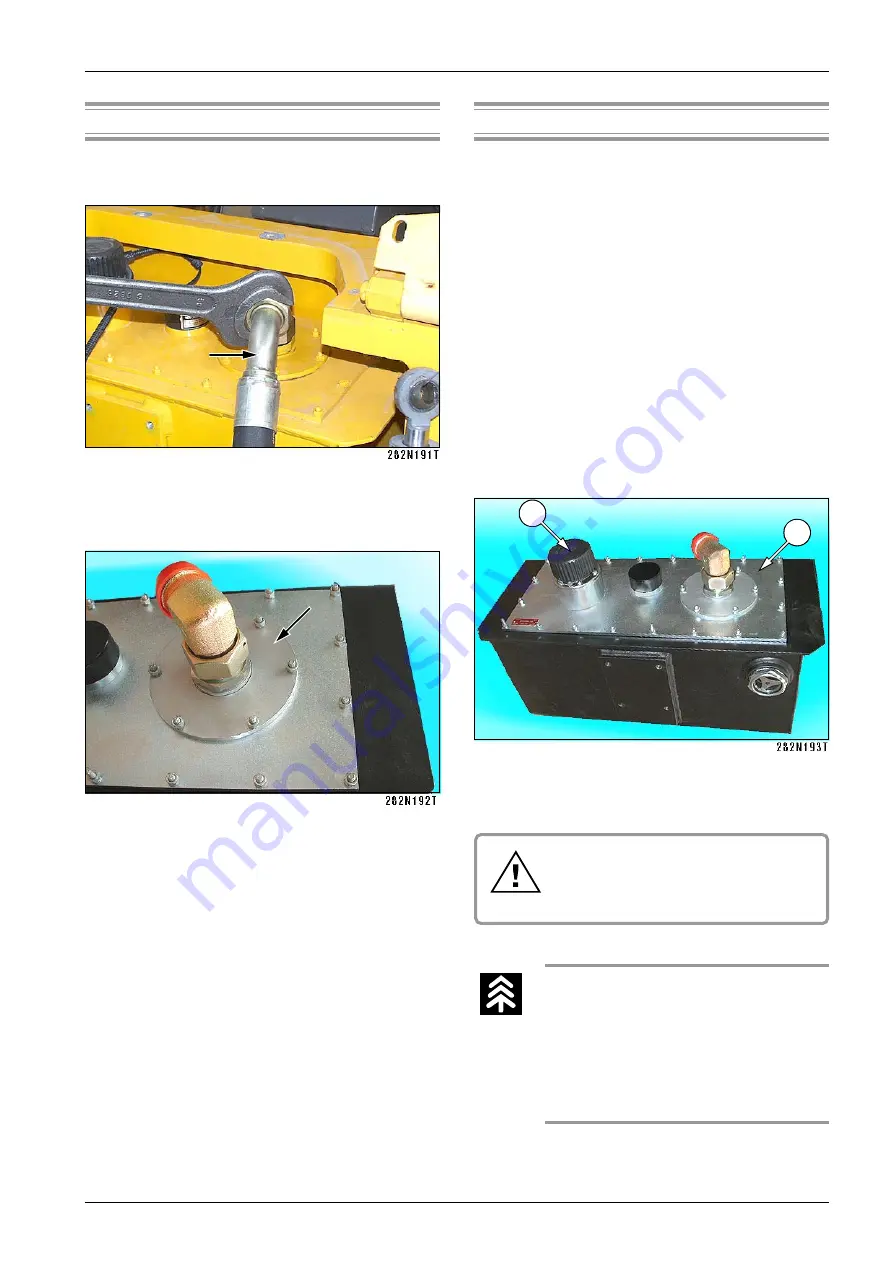
169
ASC200/ASC250
MAINTENANCE MANUAL
4
3
Every 2000 Hours or Every 2 Years
Every 2000 Hours or Every 2 Years
•
Dismantle suction hose.
•
Dismantle cover with suction strainer.
•
Dismantle the suction strainer from the suction pipe.
Wash the suction strainer and blow the strainer with
pressure air from inside.
•
Check the condition of the suction strainer; replace
the strainer in case of damaged filter part.
•
Check the inside of the tank. Carefully clean the bot-
tom and flush it with new oil if there are any impurities
on the bottom.
•
Reassemble and wipe the ”O” ring with clean oil.
NOTE
For easier cleaning it is possible to dismantle the whole
upper cover 3 with the filler 4. If you dismantled the whole
upper cover 3, use a new teflon sealing strip.
Drain oil after it has cooled
down below 50 °C (122 °F).
Follow the fire safety measures!
After disconnecting the hydraulic
circuits blind all holes with plugs.
Collect drained oil; do not leave it
soak into the soil.
Used oil is environmentally danger-
ous waste - have them liquidated.
Содержание ASC 200 Series
Страница 1: ...Operating manual E ASC 200 and ASC 250 CUMMINS TIER III 1 2008...
Страница 4: ...4 ASC200 ASC250...
Страница 10: ...10 ASC200 ASC250...
Страница 11: ...11 ASC200 ASC250 1 SPECIFICATION MANUAL ASC 200 and ASC 250 Cummins tier 3...
Страница 37: ...37 ASC200 ASC250 SPECIFICATION MANUAL N s e t o...
Страница 38: ...38 ASC200 ASC250...
Страница 40: ...40 ASC110 ASC130 ASC150 ASC200 ASC250...
Страница 58: ...58 ASC110 ASC130 ASC150 ASC200 ASC250 Controls and control devices 2 6 Controls and control devices...
Страница 64: ...64 ASC110 ASC130 ASC150 ASC200 ASC250 2 6 Controls and control devices...
Страница 66: ...66 ASC110 ASC130 ASC150 ASC200 ASC250 2 6 Controls and control devices...
Страница 68: ...68 ASC110 ASC130 ASC150 ASC200 ASC250 2 6 Controls and control devices...
Страница 70: ...70 ASC110 ASC130 ASC150 ASC200 ASC250 2 6 Controls and control devices...
Страница 72: ...72 ASC110 ASC130 ASC150 ASC200 ASC250 2 6 Controls and control devices...
Страница 87: ...87 ASC110 ASC130 ASC150 ASC200 ASC250 OPERATING INSTRUCTIONS...
Страница 121: ...121 ASC110 ASC130 ASC150 ASC200 ASC250 OPERATING INSTRUCTIONS N s e t o...
Страница 122: ...122 ASC110 ASC130 ASC150 ASC200 ASC250 N s e t o...
Страница 123: ...123 ASC200 ASC250 3 MAINTENANCE MANUAL ASC 200 and ASC 250 Cummins tier 3...
Страница 124: ...124 ASC200 ASC250...
Страница 132: ...132 ASC200 ASC250 3 4 Lubrication and Maintenance Chart...
Страница 133: ...133 ASC200 ASC250 MAINTENANCE MANUAL...
Страница 134: ...134 ASC200 ASC250 3 5 Lubrication Chart...
Страница 186: ...186 ASC200 ASC250 3 6 Individual Operations of Maintenance...
Страница 189: ...189 ASC200 ASC250 MAINTENANCE MANUAL...
Страница 190: ...190 ASC200 ASC250 3 8 Appendixes...
Страница 191: ...191 ASC200 ASC250 MAINTENANCE MANUAL MAINTENANCE MANUAL...
Страница 193: ...193 ASC200 ASC250 MAINTENANCE MANUAL MAINTENANCE MANUAL...
Страница 195: ...195 ASC200 ASC250 MAINTENANCE MANUAL MAINTENANCE MANUAL...
Страница 196: ...196 ASC200 ASC250 N s e t o...
Страница 197: ...197 ASC200 ASC250 MAINTENANCE MANUAL N s e t o...
Страница 198: ...N s e t o...