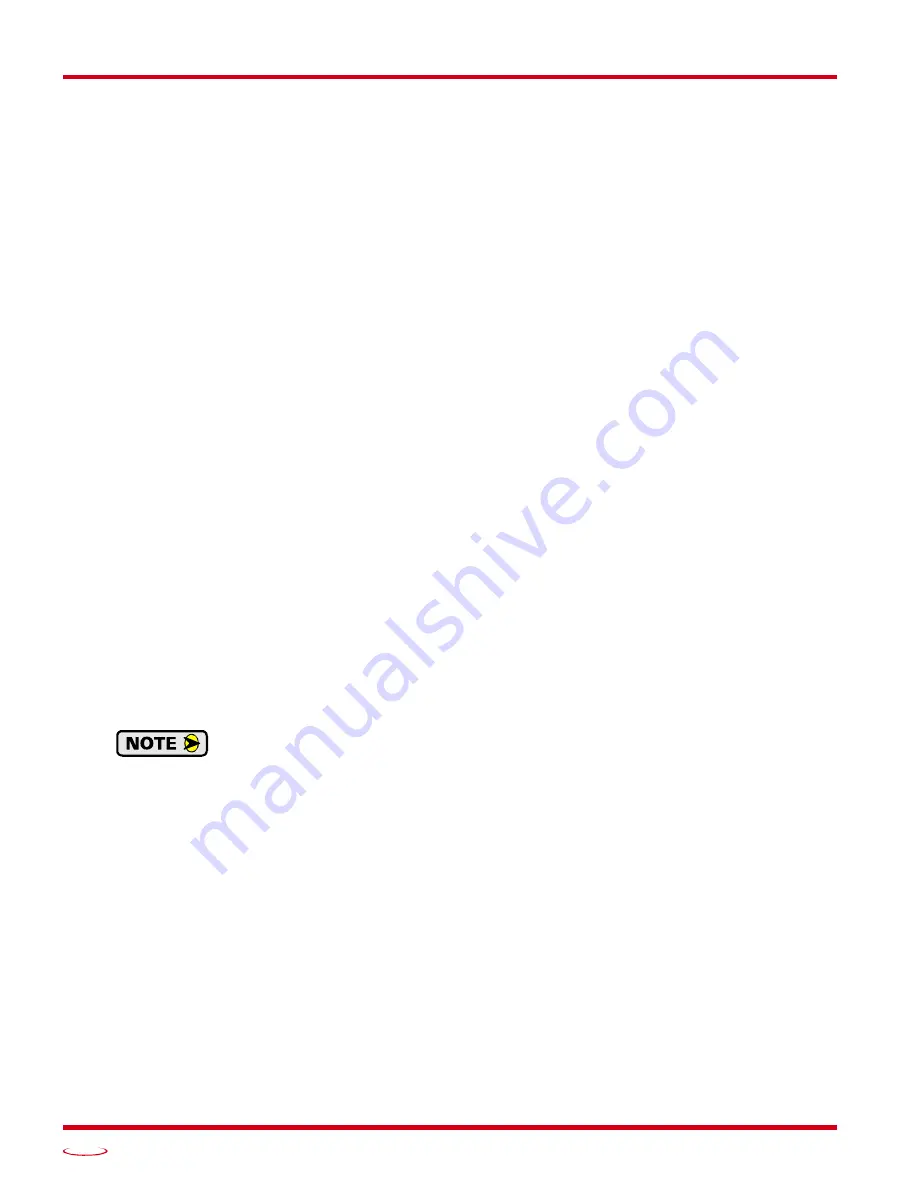
M
OTION
C
ONTROL
Networked Indexer/Driver User Manual
ADVANCED MICRO CONTROLS INC.
42
Electronic Gearing (continued)
Advanced Ratio Control
The ELGearing Multiplier and Divisor values give you a great deal of control over the ratio of motor turns per
encoder turn, but you can achieve even finer control by adjusting the Motor_Resolution parameter.
The Z pulse is not used to correct the encoder position once per turn, so you can actually program the
Motor_Resolution parameter to any value you want within its valid range. For example, if your encoder out-
puts 4,096 pulse per turn (a 1,024 line encoder) and you set the Motor_Resolution parameter to 8,192, you
will have built a 2:1 gear down into your system before applying the ELGearing Multiplier and Divisors.
(Two rotations of the encoder = 8,192 counts = 1 motor rotation.)
This technique allows you to set a median gear ratio in your system that you can adjust on-the-fly by using the
ELGearing Multiplier and Divisor parameters.
Stall Detection
Another feature available when using an encoder is stall detection. The encoder must be mounted on the
motor controlled by the Networked Driver, which means that you cannot use Stall Detection when using the
Electronic Gearing feature. When Stall Detection is enabled, the Networked Driver monitors the encoder
inputs for changes while a move is in progress. If the encoder inputs do not change as expected, the move
stops and an error bit is reported to your host controller.
In order for the Stall Detection to work correctly, you must program the
Encoder_Resolution
parameter to its
correct value in the Configuration Data of the Networked Driver. The Networked Driver always uses X4
decoding when determining the encoder position value, so the
Encoder_Resolution
parameter must be set to
four times the number of encoder lines. (When using a 1,024 line encoder, the
Encoder_Resolution
parameter
must equal 4,096 for stall detection to work correctly.)
Idle Current Reduction
Idle Current Reduction allows you to prolong the life of your motor by reducing its idling temperature. Values
for this parameter range from 0% (no holding torque when idle) to 100%.
Idle current reduction should be used whenever possible. By reducing the current, you are reducing the I
2
R
losses in the motor. Therefore, the temperature drop in the motor is exponential, not linear. This means that
even a small reduction in the idle current can have a large effect on the temperature of the motor.
Note that the reduction values are “to” values, not “by” values. Setting a motor current to
4Arms and the current reduction to 25% will result in an idle current of 1Apk. (The Networked
Driver always switches from RMS to peak current control when the motor is idle to prevent
motor damage due to excessive heating.)
Содержание SD17060E2
Страница 1: ...MICRO CONTROLS INC ADVANCED U s e r M anual Manual 940 0S172 E2 Technology E2 Technology...
Страница 10: ...ABOUT THIS MANUAL Networked Indexer Driver User Manual ADVANCED MICRO CONTROLS INC 10 Notes...
Страница 22: ...UL CUL RECOGNIZED INSTALLATIONS Networked Indexer Driver User Manual ADVANCED MICRO CONTROLS INC 22 Notes...
Страница 54: ...CALCULATING MOVE PROFILES Networked Indexer Driver User Manual ADVANCED MICRO CONTROLS INC 54 Notes...
Страница 88: ...COMMAND MODE DATA FORMAT Networked Indexer Driver User Manual ADVANCED MICRO CONTROLS INC 88 Notes...
Страница 106: ...INSTALLING AN AMCI NETWORKED DRIVER Networked Indexer Driver User Manual ADVANCED MICRO CONTROLS INC 106 Notes...
Страница 130: ...ETHERNET IP EXPLICIT MESSAGING Networked Indexer Driver User Manual ADVANCED MICRO CONTROLS INC 130 Notes...
Страница 134: ...MODBUS TCP CONFIGURATION Networked Indexer Driver User Manual ADVANCED MICRO CONTROLS INC 134 Notes...
Страница 144: ...LEADERS IN ADVANCED CONTROL PRODUCTS ADVANCED MICRO CONTROLS INC...